By Prajakta Pingulkar
Various companies need to use, store, transport, or handle liquids and chemicals that are hazardous in nature. Hence, it’s imperative to take some precautionary and counteractive measures for containing an accidental spill. It may be easier to, at times, neglect the rudiments of sustaining a safe workplace, especially when you are responsible for smoothly running a business. Nevertheless, failure to take precautionary measures for spill containment can put your company at risk for hefty fines by OSHA or EPA. It also can impact the health of the workers, leading to massive downtime at work.
Thus, spill containment products at workplaces are indispensable for avoiding leaks, spills, or unanticipated mishaps. This article broadly speaks about four must-do strategies to implement for spill containment in workplaces. Let’s dive in!
1. REGULAR MAINTENANCE AND INSPECTION OF THE INDUSTRIAL MACHINERY
The maintenance group should be appointed to examine all equipment routinely to ensure they are in the midst of safe and stable working conditions. It’s also a good practice to report their checking and audits in an inspection log for easy tracking. Additionally, in case of any observed issues, the safety manager should be promptly notified.
You can even develop your own preventative maintenance program for spill containment. An effective preventative maintenance program for spill containment will help distinguish all segments required to be examined, then set a timeline for inspecting and repairing the components, and finally include a record for easy tracking.
Below are a few things your maintenance personnel should check while inspecting the industrial machinery:
- Spraying or splashing
- Tight connections
- Drip marks or slow drips
- Corrosion
- Pooling or puddling
- Various tools and machinery are in the desirable working state
- Any leaks or spills in the pipes, seams, or containment pans
2. ENSURE THAT THE VESSELS AND SPILL CONTAINMENT BERMS USED ARE IN GOOD SHAPE
Ensure that you examine storage tanks and bulk storage vessels frequently through visual inspections and integrity testing. Drip marks, gaps, corrosion, cracks, or discoloration are some of the things that you need to look out for, among others. On noticing any of these aforementioned symptoms, make sure that you replace the containers as soon as possible. Also, in case you are qualified for SPCC, you must definitely conduct integrity testing while also judiciously examining bulk storage containers with an enormous capacity, as listed below:
- Double-walled containers
- Large bulk storage containers that are field-constructed or field-erected
- Small bulk storage containers for shops
- Vessels that are partially located/ buried/ bunkered/vaulted in or off the ground wherever positioned
It’s a smart practice to ensure that these containers are guarded with quality secondary spill containment, to avoid any unforeseen disaster.
3.CHECK AND EVALUATE YOUR COMPANY’S SPILL RECORDS
Ensure that you analyze your company’s track record history concerning leaks, spills, and even slips and drops for each tool and device used in the work area and also, the surroundings of your department. Do study the data for identifying the major pain points, and then accordingly design a suitable plan of action based on your verdicts. Not every spill gets documented at all times. At times, only the EPA or the OSHA reportable spills get documented.
Nevertheless, some techniques can be implemented for ascertaining the records of spills in your company. For instance, you can analyze how many spill kits have been employed in your workplace for spill containment. Below are a few guidelines:
- Whenever a spill kit or an absorbent is used, the safety supervisor should be informed about it.
- When you employ various spill containment services, maintain records regarding their utilization.
- Regularly speak with the different machine workers in your workplace to gather information regarding the non-reportable spills or leaks.
Going forward, it’s the best practice to keep a record of all kinds of spills, big or small, to avoid manual hassles later on.
4. ANALYZE AND ASSESS THE SPILL CONTAINMENT PLAN
In case your primary spill containment solution, such as a storage container defaults, a qualitative secondary spill containment solution is your holy grail of a shield for containing accidental spills and leaks. In an unprecedented development of a leak or spill, a secondary spill containment solution will help counter the liquid from spreading. Hence, ensure that you have an active as well as a passive spill containment solution in place.
An active spill containment solution implicates a containment solution that needs an individual to take a relevant action when a spill transpires. This may entail using a spill kit or the mops to clean the spill, putting down the drain covers, or up a temporary containment wall, among others. Meanwhile, passive spill containment involves a solution that is already in place if and when a spill happens. This may include secondary spill containment berms, absorbent mats or pads, drip pads, and safety floor mats.
Ensure to run a meticulous 360-degree inspection of all the storage vessels, and tanks, that may be prone to oil leaks or spillage of any other fluids. If there’s a storage failure, ensure the secondary spill containment solution employed intercepts the liquid from reaching the drains or pathways.
FOR MORE INFORMATION
Basic Concepts, Inc. is the world leader in the portable spill containment market because they offer high quality products that have features that customers prefer year after year. Customers can discuss their secondary containment requirements with one of BCI’s experienced, on-staff technical sales representatives. BCI gladly supplies references, comparative test data, and sample spill containment materials to help you make an informed decision. Basic Concepts is part of the Justrite Safety Group. For more information, visit www.basicconcepts.com.
MODERN PUMPING TODAY, November 2020
Did you enjoy this article?
Subscribe to the FREE Digital Edition of Modern Pumping Today Magazine!
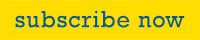