Bradleys, a service center that specializes in electric motor repair and testing, is about to mark its 95th anniversary as a family-owned and operated business. What’s more impressive is that the company has successfully navigated five generations of employees, which presents its own unique set of challenges. The ability to persevere through six wars, epidemics, pandemics, and several hurricanes is a testament to strength and adaptability. In addition to striving to survive, it is apparent that the team at Bradleys has a strong foundation to manage any obstacle that comes their way.
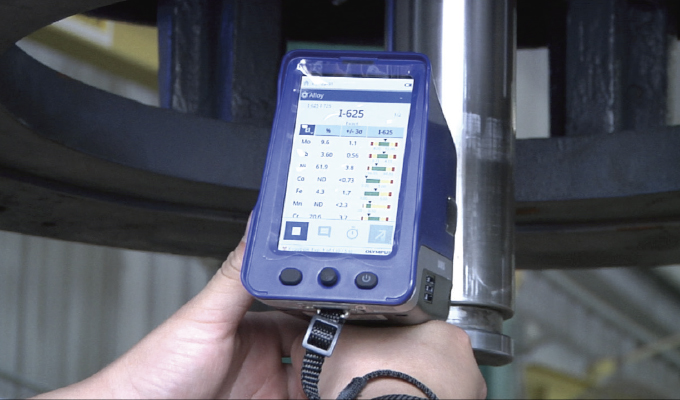
EMBEDDING INDUSTRIALLY RECOGNIZED STANDARDS
Industries, products, and speed of services are constantly evolving and so are the concepts of quality assurance. In response to these challenges, Bradleys has taken significant steps to improve their Quality Assurance approach in response to the constantly evolving industry, products, and speed of service. The company has phased out ‘tribal knowledge’ and implemented institutional knowledge, allowing it to deliver the best value to customers in a timely and reliable manner.
To ensure the highest quality of service, Bradleys’ teams are trained to maximize the usage of proven guidelines, industrial standards, and testing methods, including EASA, IEEE, NEMA, SAE, and customer-specified standards. This has enriched Bradleys’ service quality and eliminated the hindrance of the so-called silo system, thanks to the induction of well-selected craftsmen and professionals with diversified knowledge bases and experience.
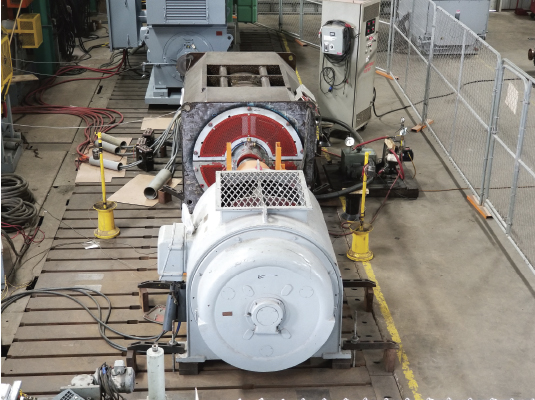
PATH TO RELIABILITY: RISK ANALYSIS AND MITIGATION
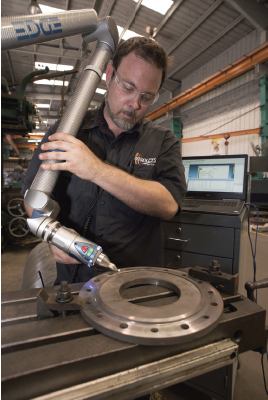
The focus on quality is not just a buzzword, but a fundamental principle that drives their business. By prioritizing processes, standards, and prevention, the company can consistently deliver high-quality results to its clients and partners. Bradleys’ commitment to meeting the evolving needs of its clients is reflected in their ISO 9001:2015 certification, which demonstrates their dedication to excellence. Transparency and honesty are core values that guide the company’s actions, and it is dedicated to building and maintaining strong relationships based on trust and collaboration. These concepts also prioritize the voice of the customer, which is data-driven, and includes continuous improvement in which Bradleys strives to deliver high-quality results to their clients and partners. Additionally, reliability and reproducibility of gauges are employed at Bradleys. When implemented correctly and promptly, quality translates to product and service reliability for all stakeholders.
Bradleys’ team of professionals has undergone a transformation by integrating experienced craftsmen, engineers, as well as seasoned and young professionals to deliver exceptional results. The team is committed to enhancing customers’ experience by not merely replacing faulty components but by analyzing the motor’s diagnosis and operations to identify the root cause of failure. The team establishes a failure-point relationship and works towards resolving every customer motor case, thus delivering greater value for their motor repair and testing costs.
INTERNAL PROCESS IMPROVEMENT
As no company or system is infallible, Bradleys provides its employees with an app to flag any issues that require correction. This tool empowers staff to express their thoughts and ideas, which is the ultimate goal of enhancing efficiency, elevating service levels, and boosting productivity. The app is open to all Bradleys team members who can use it to highlight areas for improvement, gaps, or near-misses. Modern management recognizes that employees are a valuable resource for continuous improvement, and Bradleys’ management team reviews all suggestions put forth via the app. Management and staff employ available tools to respond and take corrective action vis-à-vis recurrence proofing.
To effectively manage and improve processes, Bradleys follows the mantra “if you can’t track it, you can’t control it.” It includes data collection, analysis, algorithm development, and metric creation to measure performance. Through ongoing monitoring and analysis, Bradleys can improve its services by identifying areas for enhancement and taking proactive measures.
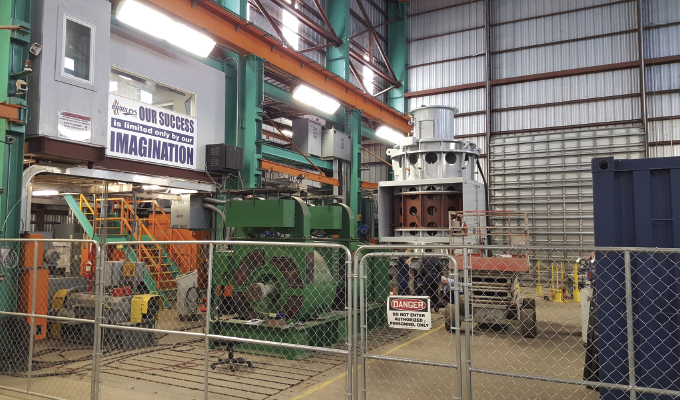
INTERNAL AND EXTERNAL RESOURCES
A service industry such as Bradleys is challenged with numerous issues that need to be addressed. First, it is essential to maintain the service floor hardware and ensure the timely addition of new inspection and processing devices. Second, having a trained and skilled team that receives continuous training and documentation of knowledge is crucial. Third, adhering to service standards, including transparency, time commitment, traceability, and post-service coordination, is imperative for maintaining quality. This also encompasses Bradleys’ internal standards and guidelines.
External resources, or suppliers, are also vital to Bradleys, especially when critical parts and services from suppliers are employed. Ensuring supplier quality assurance is crucial when discussing Total Quality Management (TQM). ISO 9001-2015 acknowledges TQM as one of the backbones of quality and is given Bradleys’ full attention.
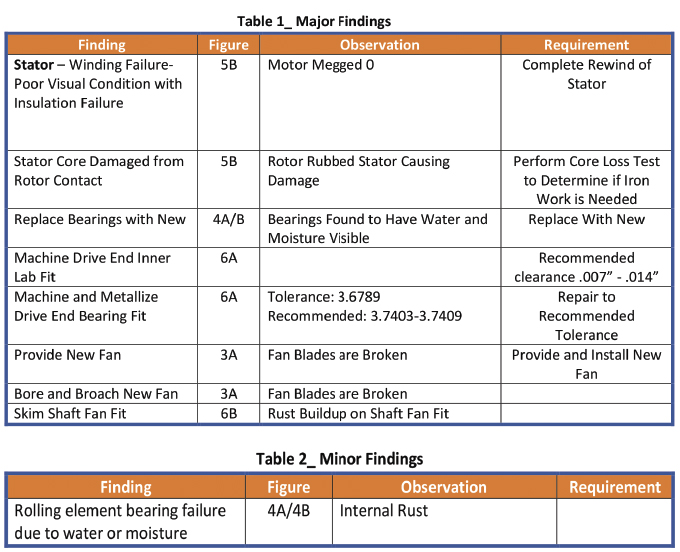
DATA DRIVEN DECISION-MAKING AND TRACEABILITY SYSTEM
In the modern digital era, data is abundant, but organizing and analyzing it intelligently can create significant value. Bradleys recognizes the importance of impartial information on service history for clients, investing in applications that collect, organize, and manipulate data for scientific conclusions. This saves time and effort for both parties, building trust in Bradleys’ services. Comprehensive reports such As-Found reports are shared with clients, offering valuable insights that can reduce liability and improve long-term reliability. The focus on details makes Bradleys’ services dependable and valuable to customers and their motors.
Bradleys is at the forefront of adopting new technologies every day and implementing a new quality model across the organization. Their skilled craftsmen and experienced professionals are driving these initiatives, utilizing the best available standards to enhance service quality. The American Society of Quality (ASQ) recognizes this as the Industry 4.0 era, requiring a new paradigm and innovative concepts to meet and exceed customers’ ever-changing expectations. Traceability, on-time delivery, and zero-defect have always been critical factors for success. Bradleys’ road to continuous improvement is always under construction.
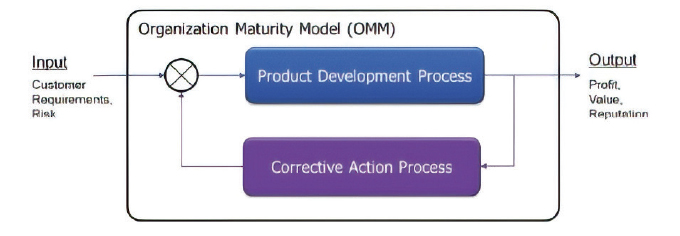
FOR MORE INFORMATION
As an ISO 9001:2015 Certified Company with a Continuous Improvement mindset, Bradleys recognizes that agility and a sense of humor are necessary. No matter how well-thought-out its written procedures may be, there is always room for improvement, whether it’s mitigating risks, providing training, or enhancing communication. Bradleys’ continuous improvement journey started with significant effort, time, and investment. For more information, visit www.bradleysmotors.com.
MODERN PUMPING TODAY, June 2024
Did you enjoy this article?
Subscribe to the FREE Digital Edition of Modern Pumping Today Magazine!