In part 1 of this series, we saw that uses of grinders in petroleum-related pump situations can vary widely, from complex crude oil tank-bottom cleaning to simple portable grinders used on location. In this month’s conclusion, we’ll take a closer look at reclamation of drilling mud from drill cuttings as well as the use of grinders for protecting pumps in petroleum applications.
RECLAIMING OF DRILLING MUD FROM DRILL CUTTINGS
Drilling fluids (drilling mud) are integral to the drilling process, serving to lubricate and cool the drill bit, as well as convey the drilled cuttings away from the bore hole. These fluids are a mixture of various chemicals in a water-based, oil-based or synthetic-based solution. Drill cuttings are broken bits of solid material that are produced as the drill bit breaks the rock. Drill cuttings vary in size and texture, ranging from fine silt to gravel.
For both environmental reasons and to reduce the cost of drilling operations, drilling fluid losses are minimized by stripping them away from the drill cuttings before the cuttings are disposed of. On drill sites, the systems used to reclaim mud are considered to be of critical importance to the process throughput and efficiency of the operation. Mud reclamation is primarily accomplished using shale shakers with vibrating screens to separate the mud from the shale, with subsequent processing of larger cuttings with centrifuges.
The mud passes through the screens and is collected into mud tanks. The drill cuttings remain on top of the shale shaker screens. The vibratory action of the shakers moves the cuttings down the screen and off, where they can be collected and stored in a tank or pit for further treatment or disposal.
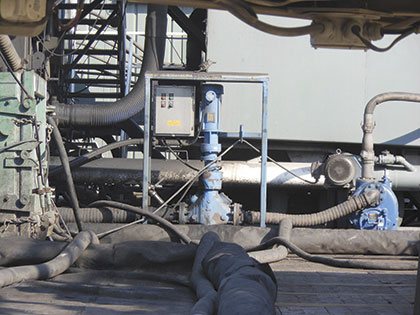
The separated drill cuttings, which were not sifted through the screens, but still coated with a large quantity of drilling mud, are slurried to centrifuges for separation. Since centrifuges perform better when particle size is consistent, solids control companies grind the cuttings to a specific size to achieve maximum throughput rates.
“Centrifuges spin at a very high G-force, and particles that are too large will wear the throat of the centrifuge more rapidly,” says Gary Smith, industrial distribution sales manager with JWC Environmental (www.jwce.com), based in Santa Ana, California, a leading manufacturer of grinders for municipal and industrial applications, including for the oil and gas industry.
“The solids control people found that when they ground up the big cuttings into small pieces there was more surface exposure, and they reclaimed more mud,” adds Smith. “An important point, because it increased their mud return by about 100 percent. This helped them drill faster, and get on and off the rig sites in less time. It has really pushed the efficiency of these drill operations.”
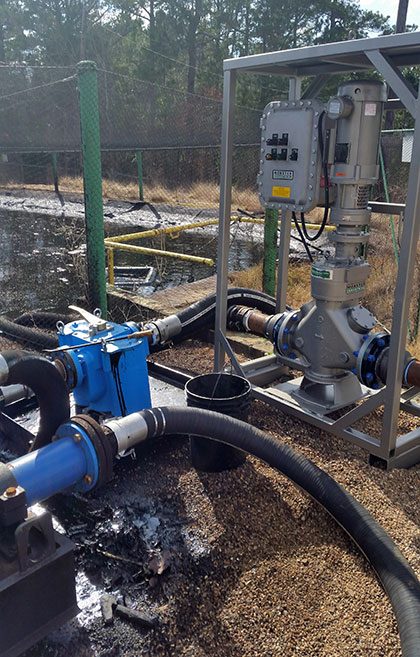
“For grinding drill cuttings, which are essentially rock, dual-shafted, slow-speed, high-torque grinders, using two stacks of hardened steel cutters, are the preferred equipment choice,” continues Smith. “These grinders will get from three months to a year grinding solid rock before the cutters need to be replaced. That outperforms any other equipment for this purpose. Plus, they provide complete protection for downstream equipment, like pumps and centrifuges.”
GRINDERS PROTECT PUMPS IN PETROLEUM APPLICATIONS
Powerful, high-torque grinders are being employed in a number of different petroleum-related applications where pumps need to be protected. One of these is in the extraction of oil sands.
Oil sands (tar sands) are a mixture of sand, water, clay, and bitumen found in several locations around the globe, with the largest reserve located in Alberta, Canada, which can be upgraded into synthetic crude oil and other petroleum products. They are scooped up from open pit mines and transported to extraction facilities for finer processing. The tar sands are mixed with very hot water, allowing oil to separate out at the top of huge separation tanks.
In the separation process, roots, plant life, and sometimes petrified wood is present that would cause pumps to plug in the extraction facility, thereby creating problems throughout the production line. In-line grinders are a necessity here to grind materials to a size that will not plug the pumps.
“Pumps are designed for different applications, so you are going to be more efficient at pumping clean water than you will be at pumping a slurry,” says Daniel Namie, with Superior Pumps of Sycamore, Illinois, a distributor of pumps for municipal and industrial applications, including for petroleum applications.
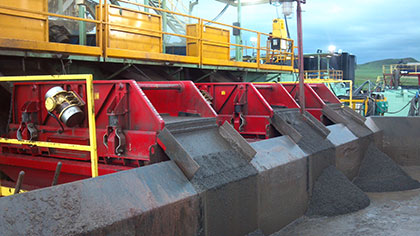
“When a pump impeller is cruising along at 3,600 rpm the velocities at the tip are extremely fast, and can easily destroy all the metal on the impeller passing too large of a solid. So, in many applications we specify high-torque grinders, preferably dual-shaft, to grind up sludge or debris that could harm the pump.”
The uses of grinders in petroleum-related pump situations can vary widely, from complex crude oil tank-bottom cleaning to simple portable grinders used on location.
“One of our customers had a large settling pond that was laced with petroleum, and needed to use polymers to bind with the petroleum for extraction,” adds Namie. “The polymer coagulated the petroleum, and those big solids could not be run through their pump without clogging it. So, we supplied a portable high-torque, dual-shafted grinder which protected his pump from potential damage. A simple solution that may have saved them thousands of dollars in pump damage.”
For More Information
JWC Environmental designs, builds, and services the world’s most dependable waste shredders and screening systems to help municipal facilities and industrial companies solve challenging waste reduction and recycling applications. Founded in 1973, the company has built and shipped over 35,000 Monster shredders and screens to its customers around the world, in diverse industries like energy, wastewater, recycling, oil, chemicals, marine, and facility management. For more information, contact Kevin Bates, director of global marketing, JWC Environmental; at 949.833.3888 or kevinb@jwce.com; or visit www.jwce.com.
____________________________________________
MODERN PUMPING TODAY, February 2018
Did you enjoy this article?
Subscribe to the FREE Digital Edition of Modern Pumping Today Magazine!
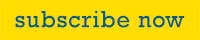