By Johann Fourrat-Besson
It’s a fact of life that industrial manufacturers will need to create or work with liquid components that are sensitive or hazardous. One of the most notable of this class of hard-to-handle liquids is dilatant isocyanates. They possess strict product-handling requirements that must be adhered to, making choosing the proper pumping technology highly critical in ensuring a safe, reliable and efficient dilatant isocyanate-handling operation.
In that vein, eccentric disc pump technology has risen to the fore as a go-to choice for the production and handling of isocyanates and other classes of dilatant fluids.
THE CHALLENGE
First, though, let’s take a closer look at these types of liquids and see how their product-handling characteristics and requirements can create numerous challenges for industrial-manufacturing plant operators:
Dilatants
By definition, dilatants are materials that “increase in viscosity and set to a solid as a result of deformation by expansion, pressure or agitation.” As such, they are also commonly known as “shear thickening fluids,” or STFs. In other words, the viscosity of dilatants increases in proportion to the amount of shear stress/strain that is being put on them during their movement through fluid-transfer applications.
For example, when force (or shear) is applied to a precise 1:1.25 mixture of water and corn starch, the mixture will act as a solid rather than a liquid. Another real-world example can be found that while walking on a patch of wet sand, a dry footprint will appear.
The dilatant characteristics of these materials makes their proper handling paramount in fluid-transfer applications. If the shear rate is too high during their transfer, they can revert to a high-viscosity state that will compromise a pump’s ability to push them through the process piping. In this case, as a dilatant material begins to thicken, the pump’s operation will need to adjust to the changing properties of the liquid. Therefore, dilatants require a pump technology that produces little to no shear when operating, lest the material transform into a high-viscosity liquid and fall outside the pump’s reliable operational range.
Isocyanates
Isocyanates, which are classified as dilatants, are a family of highly reactive, low molecular weight chemicals that have been featured in a wide range of industrial manufacturing and processing applications since the 1950s. The most widely used isocyanate compounds are diisocyanates and polyisocyanates. Within the diisocyanates family, methylenebis (phenyl isocyanate), known as MDI, and toluene diisocyanate (TDI), are the most regularly used.
MDI and TDI are required components in polyurethane, which is used in the manufacture of flexible and rigid foams, fibers, elastomers, and coatings, such as paints and varnishes. Isocyanates are also used in the automobile industry, as well as in auto body repair and building insulation materials. Spray-on polyurethane products containing isocyanates have been developed for a wide range of retail, commercial, and industrial uses to protect cement, wood, fiberglass, steel, and aluminum, and, more specifically, protective coatings for truck beds, trailers, boats, foundations, and decks.
The benefits (and need) of isocyanates as a component in the manufacture of many important products is unquestioned. Also unquestioned is the fact that isocyanates can be extremely dangerous for the user, surrounding populations, and the environment if they are not handled properly and with great care throughout their entire production and supply chain.
Prolonged exposure to, or even simple contact with, isocyanates can result in many adverse health effects. Among them are acute “isocyanate asthma” attacks that can include coughing, tightness of the chest, and shortness of breath; skin irritation that can lead to rash, itching, hives, and swelling; irritation to the mucous membranes, eyes, nose, and throat; gastrointestinal irritation; and pneumonitis, or swelling of the lung walls.
The most common occupational exposure to isocyanates is inhalation of a vapor or aerosol, although exposure may occur through skin contact during the handling of liquid isocyanates. Exposure typically occurs during the production and use of isocyanates, particularly during the manufacturing process in the polyurethane foam industry. Additionally, isocyanates are toxics and pollutants, and can be flammable. While their flammability is low, specific concentrations or the presence of explosive vapors or other flammable liquids in the same facility where isocyanates are being used or manufactured can create an explosive atmosphere for plant personnel and the surrounding community.
As mentioned, to safely, reliably, and efficiently handle dilatants and isocyanates, operators must choose the correct pumping solution for this application, one that handles product gently (low shearing), has strong suction capability and offers a low-maintenance wear-compensation design. Various technologies can be used to transfer dilatants and isocyanates, but the safest, most reliable, and most efficient pumping solution that meets all of the above criteria is the eccentric disc pump.
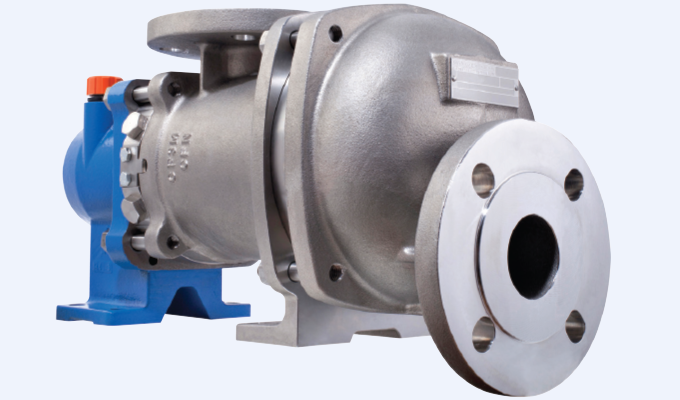
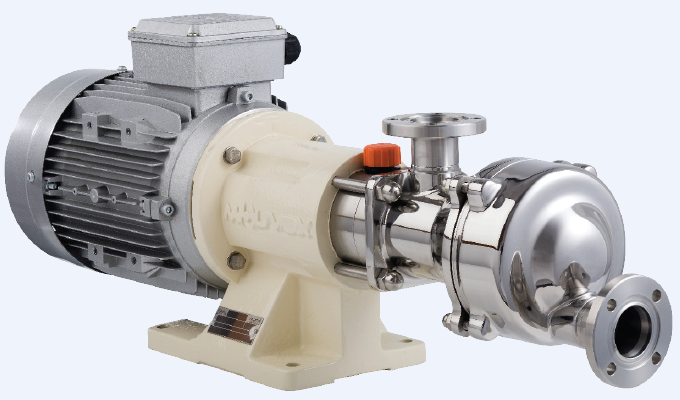
THE SOLUTION
Eccentric disc technology provides less risk and more efficiency than other pumps. The advantages of using eccentric disc pumps are numerous:
Design
Eccentric disc pumps consist of a stationary cylinder and mobile disc, with the disc moved by an eccentric shaft that is housed inside a bellows end, which holds the disc. As the eccentric shaft is rotated, the disc forms chambers within the cylinder, increasing at the suction port and decreasing at the discharge port. During operation, the discharge pressure exerts itself against the eccentric disc, preventing it from slipping.
The low slip between the disc and cylinder gives eccentric disc pumps their ability to strip or clear lines of product. Isocyanates are toxic by nature so they require seal-less pumps to eliminate leaks and provide maximum product containment. Eccentric disc pumps have no magnetic couplings, packing, or mechanical seals, which eliminates a potential leak point that can lead to failure.
Strong Suction
When transferring any hazardous or hard-to-handle liquids, it’s important to have a pump capable of clearing lines. Since isocyanates are a highly toxic pollutant, it makes loading and unloading much safer and cleaner as hoses and pipes are emptied prior to disconnection at the end of the transfer process. Eccentric disc pumps also feature superior suction at low speeds, ensuring that a minimum amount of product is left in the piping at the end of product runs.
Low Shear
When dilatants materials such as isocyanates are subjected to high shear and agitation, their viscosity tends to rise. When this happens, the end result is often pump failure and resulting maintenance, repair, replacement, and downtime. Experiencing excessive shear is a problem that cannot happen with eccentric disc pumps due to their low shear rate.
Wear Compensation
Most positive displacement pumps do not have wear-compensation systems, which means normal pump wear will lead to progressive flow rate degradation. Operators can try to compensate for wear by accelerating the pump, but that will begin a dangerous cycle of running the pump faster, which, in turn, results in the pump components wearing faster, all while consuming more energy. The unique design of eccentric disc pumps allows them to self-compensate for mechanical wear, giving the pumps the ability to maintain consistent flow rates over time. Eccentric disc pumps have a built-in wear-compensation system that keeps them running like new despite wear and without the need for speed increases.
CONCLUSION
French eccentric disc pump manufacturer Mouvex® offers two pumps series that are ideally suited for dilatant and isocyanate transfer: the SLC Series and C Series Eccentric Disc Pumps. Both models require no magnets, mechanical seals, or packing, and are ATEX-rated and TA Luft-certified to handle the most dangerous properties in the most explosive manufacturing environments. Both pumps are self-priming, have line-stripping capabilities, can run dry for up to five minutes, produce low shear rates, and can create high vacuum and compression effects. Both also have a reduced number of components, which leads to reduced maintenance. SLC models are available in stainless steel, while C Series pumps are available in ductile iron. All models are suitable for handling any type of dilatant and isocyanate liquid.
In today’s manufacturing environments, dilatant isocyanates are among the most important compounds within the production process. Many short- and long-term risks are involved with handling them. Therefore, operators need the peace-of-mind that only eccentric disc pumps can deliver. Eccentric disc pumps are low-maintenance and deliver the superior wear compensation, strong suction, and low shear that is mandatory when handling these unique materials. In that realm, Mouvex® is leading the way in safe dilatant isocyanate transfer with its SLC Series and C Series Eccentric Disc Pumps.
FOR MORE INFORMATION
Johann Fourrat-Besson is the industry product manager for Mouvex® and can be reached at johann.fourrat-besson@psgdover.com or 33.386.498.669. Auxerre, France, based Mouvex was incorporated in 1906 and is a leading manufacturer of positive displacement pumps, screw compressors, and hydraulic coolers for use in the refined-fuels, oilfield, energy, food/sanitary, military, transport, and chemical-process industries. For more information on Mouvex or PSG, visit www.mouvex.com or www.psgdover.com.
MODERN PUMPING TODAY, September 2020
Did you enjoy this article?
Subscribe to the FREE Digital Edition of Modern Pumping Today Magazine!
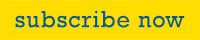