There are two grades of PTFE that can be used in the manufacture of diaphragms: conventional (homopolymer) and modified (copolymer). The lowest performing grade is conventional PTFE. White in color, it exhibits poor flex life and high void content. Modified PTFE is conventional PTFE whose characteristics have been chemically altered; it is translucent and offers improved flex life and lower void content.
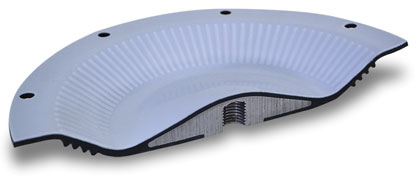
Figure 4: Cross-section of an integral piston diaphragm (IPD) consisting of a PTFE face, fabric reinforced rubber backer and integrated piston to attach directly to the pump shaft.
PRODUCTION METHODS
PTFE sheets are produced by one of three primary methods: skiving, expanding, or calendering. Skiving employs a compression molding process to create billets of PTFE, which are then sliced into thin layers. This process results in lower flex life, uneven tensile strength and high void content, all of which lead to poor diaphragm performance. Skived PTFE can be made from either conventional or modified PTFE.
Expanding and stretching PTFE is done to produce very high, even tensile strength, high flex life, excellent abrasion resistance, and low void content. Expanded PTFE can be made from either conventional or modified PTFE, however conventional PTFE is more often used and results in a white appearance.
Calendering uses large rollers to press the PTFE fibers together which yield even tensile strength, high flex life, and ultra-low void content. Calendered PTFE is typically made using modified PTFE and is clear in appearance.
Figure 3 shows the differences in appearance when the materials are placed on top of white lettering with a black background. The modified calendered PTFE is nearly translucent, the modified skived PTFE is cloudy and both the conventional skived and expanded PTFE are white.
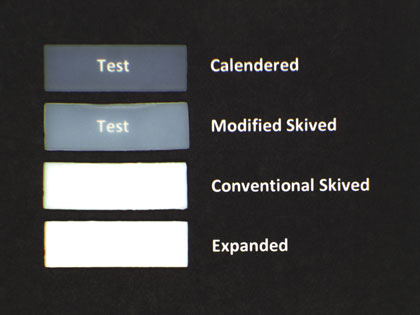
Figure 3: Clarity of PTFE materials produced by different methods.
TEST RESULTS
Table 1 shows actual test results of these four materials. In terms of permeation resistance (SVI) and cycle life, the modified calendered PTFE has superior results. This material is typically recommended for applications involving steam cycling, strong chemicals, ultra-pure media, or for pumps operating in clean environments such as the production of semiconductors, photovoltaic cells for solar energy, chemicals, LEDs, flat panel displays, or pharmaceuticals.
Conventional expanded PTFE is the strongest material and is recommended for pumps operating at high pressure differentials or for abrasive media. Common applications include paints, coatings, mining, ceramics manufacturing, pickling baths, and electroplating. Conventional and modified skived PTFE are considered lower performing materials and are typically used in non-critical applications or applications where the diaphragm is changed at fixed intervals.
Diaphragm performance and ease of installation can be further improved by adding ribs, using one-piece designs and molding the piston into the diaphragm. Flexing a diaphragm can create stress points; incorporating ribs in the PTFE and backing it with rubber allow the material to flex more easily thereby reducing stress and extending service life. Diaphragms with rubber backings are available in one- or two-piece designs. One-piece diaphragms (see figure 4) involve the added step of bonding the PTFE to rubber. This makes the diaphragm easier to install and reduces the potential for improper installation, such as having the wrong side facing the media.
Diaphragms used in mechanically and air-operated pumps use pistons to connect the shaft to the diaphragm. Integrating a piston into the design of a diaphragm eliminates metal contact with the process media, reduces the potential for cross-contamination, and makes it easier to clean and install. This design is commonly used in areas where CIP/SIP is performed, paint or coating operations and for some critical chemical and hazardous gas applications.
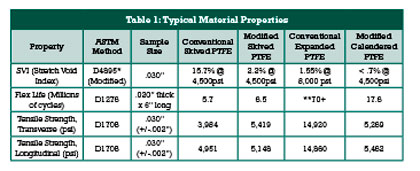
*The SVI test compares the specific gravity of PTFE to PTFE samples stretched at 4,500 psi stress. Due to its very high tensile strength the expanded PTFE was stretched at 8,000 psi.
**Test was stopped over time. Flex life is very high due to the high tensile strength.
CONCLUSIONS
The grade of material and manufacturing method have an enormous effect on the overall performance of PTFE diaphragms. For optimal pump operation it is vital to review the specific application requirements and select the best PTFE diaphragm material. Using the wrong type of material can lead to equipment downtime, loss of product, and potential safety hazards. Pump diaphragms are low cost, high consequence components, where the cost of the actual diaphragm is negligible compared to the cost of failure.
About The Author
Michael Brooks is the applications engineer and Sarah Young is product manager of diaphragms and valves for Garlock Sealing Technologies. They can be reached at michael.brooks@garlock.com and sarah.young@garlock.com. Based in Palmyra, New York, the Garlock family of companies is acknowledged as the global leader in high-performance fluid sealing and pipeline protection products for industry and infrastructure. For more information, visit www.garlock.com.
____________________________________________
MODERN PUMPING TODAY, September 2015
Did you enjoy this article?
Subscribe to the FREE Digital Edition of Modern Pumping Today Magazine!
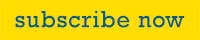