The following study consisted of three phases that started in the autumn of 2016 at a site located in Egypt by the Red Sea. The primary objective of pretreatment to any membrane system is to ensure the feed water is compatible with the membrane. Inadequate membrane pretreatment results in high chemical cleaning costs, increased downtime, permanent loss of performance and reduced membrane life. This is particularly true in seawater reverse osmosis (SWRO) desalination plants where water quality parameters fluctuate. High salinity can also significantly reduce the efficiency of coagulation, flocculation and dual-media filtration.
Cross-flow microsand filters (CMF) consist of pressurized vessels with the use of fine silica sand and crossflow hydraulics to achieve high efficiency filtration. Fortex Experts put the Vortisand filtration technology to the test!
The study demonstrated that the technology of the Vortisand crossflow microsand filtration system made it a much more effective solution at reducing suspended solids and SDI than conventional multi-media filters. With filtration rates of 3 to 4 times those of MMF systems, the Vortisand system produced water with an SDI less than or equal to 2.4.
It appears that cross-flow microsand filtration is a better alternative to conventional filtration methods and has the potential to significantly reduce the life cycle costs of SWRO desalination projects. Further studies will confirm long term technical performance and related impact on SWRO Capital and Operating cost. The Fortex Experts and Evoqua teams are excited to start working on the third stage of the three-phase study; determining the impact and ROI of the high efficiency cross-flow technology.
The primary objective of pretreatment to any membrane system is to make the feed water compatible with the membrane. Inadequate membrane pretreatment results in high chemical cleaning costs, increased downtime, and permanent loss of performance and reduced membrane life. This is particularly true in seawater reverse osmosis (SWRO) desalination plants with open intakes where water quality parameters fluctuate. High salinity can also significantly reduce the efficiency of coagulation, flocculation, and dual-media filters.
Cross-flow microsand filters (CMF) consist of pressurized vessels and use fine silica sand and cross-flow hydraulics. CMF typically operate at rates ranging from 30 to 60 m/h and yet are able to achieve submicronic particle removal. They are pressurized shallow-bed mono-media filters operating as dead-end filters (100 percent of the inlet water is filtered without loss).
Vortisand filters rely on diffusers inducing crossflow patterns to sweep the surface of media and prevent surface blinding. Larger particles are maintained in suspension (above the media), preventing surface blinding and channeling, allowing for high filtration rates, improved removal efficiency of fine particles, and extended duration of filtration cycles.
The program consisting of three phases started in the autumn of 2016. The first phase was completed to determine the optimal filtration rate and performance of microsand filtration. The second phase was conducted to determine the impact of microsand filtration on the membrane flux rate, trans-membrane pressure, operating pressure, and cleaning frequency. The third phase helped determine the long-term effects of CMF on SWRO membranes life and performance. Economic parameters were also evaluated and compared to other SWRO systems.
The study was conducted with two side-by-side SWRO trains sharing a common open sea intake. Based on a well-documented methodology the Fortex Experts and Vortisand team had three objectives in mind;
- Measure the field performance of CMF in comparison to existing multi-media filtration (MMF) pretreatment systems.
- Observe and measure the impact of two different pretreated water qualities via silt density index (SDI) and levels of turbidity.
- Determine the impact and ROI in relation to operating costs, water recovery, cleaning frequency, chemical consumption, power cost, feed pressure, and backwash volume.
PRETREATMENT COMPARISON
Two side-by-side SWRO trains sharing a common open sea intake were used for this study. This program had three objectives, based on a well-documented methodology.
The first objective measured the field performance of CMF in comparison with existing MMF as pretreatment to a SWRO system. The optimal operating conditions were determined during the first weeks for each pretreatment system. The existing SWRO plant was very simple and facilitated the comparison between the two different media filtration systems.
The second objective was to observe and measure the impact of the two different pretreated water qualities on the performance of the downstream SWRO trains. Cleaning frequency and water quality are the most important parameters to determine the best pretreatment.
The third objective was to determine the impact of CMF optimal operating conditions on the global operating cost related to filtration run time, water recovery, cleaning frequency, chemical consumption, power cost, feed pressure, and backwash volume.
The site is located in Soma Bay, 45 kilometers south of Hurghada International Airport. Hurghada is one of the leading coastal resorts on the Red Sea.
The average surface water temperature of the Red Sea during the summer months is approximately 79 degrees Fahrenheit (26 degrees Celsius) in the north and 86 degrees Fahrenheit (30 degrees Celsius) in the south, with only about 3.6 degrees Fahrenheit (2 degrees Celsius) variation during the winter months. The overall average water temperature is 72 degrees Fahrenheit (22 degrees Celsius).
SWRO TRAIN USING MULTI-MEDIA FILTERS
Both SWRO systems used the same raw water coming from a common open seawater intake. The SWRO plant using conventional filters produced 1850 m3/d of desalinated water at a recovery of 35 percent. The existing plant comprised of three separate trains:
Train 1
- Description: 1 skid production capacity 600 m3/d at 35 percent of recovery
- Array: 8 PV: 6 el/PV, Filmtec SW30HRLE-400 with permeate flux of 14 lmh
- Three multi-media filters of 1500 mm of diameter with a flux of 15.8 m/h
- Anti-scaling and acid dosing system
Train 2
- Description: 1 skid production capacity 500 m3/d at 35 percent of recovery
- Array: 7 PV: 6 el/PV, Filmtec SW30HRLE-400 with permeate flux of 13.4 lmh
- Two multi-media filters of 1,800 mm of diameter with a flux of 13.8 m/h
- Anti-scaling and acid system
Train 3
- Description: 1 skid production capacity 750 m3/d at 35 percent of recovery
- Array: 10 PV: 6 el/PV, Filmtec SW30HRLE-400 with permeate flux of 14 lmh
- Two multi-media filters of 2,100 mm of diameter with a flux of 15.3 m/h
- Anti-scaling and acid dosing system
SWRO TRAIN USING CROSS-FLOW MICROSAND FILTERS
Train 1 of the existing SWRO system was used to test the CMF. The modified train comprised of the following components:
Train 1
- 1 skid production capacity 600 m3/d at 35 percent of recovery
- Array: 8 PV: 6 el/PV, Filmtec SW30HRLE-400 with permeate flux of 14 lmh
- One CMF with a surface of 1.32 m2 (see figure 3) with a flux between 30 and 60 m/h
- Anti-scaling and acid dosing system
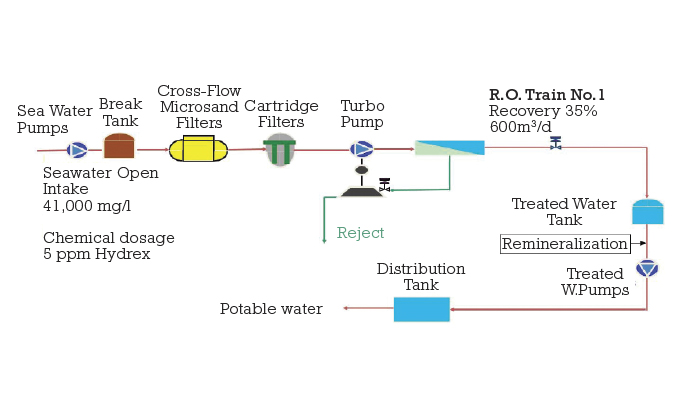
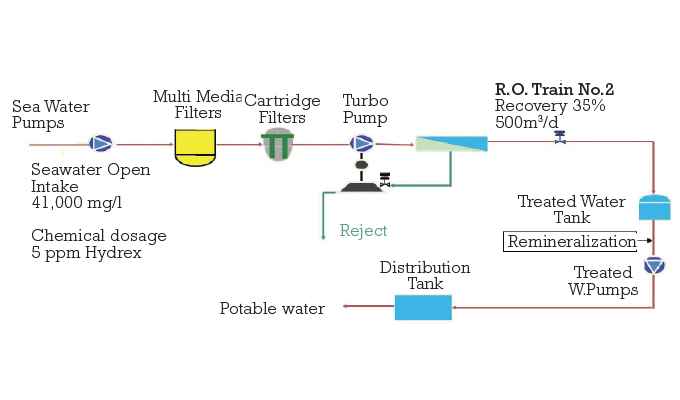
Train 2 of the existing SWRO system was used to compare the results coming from CMF.
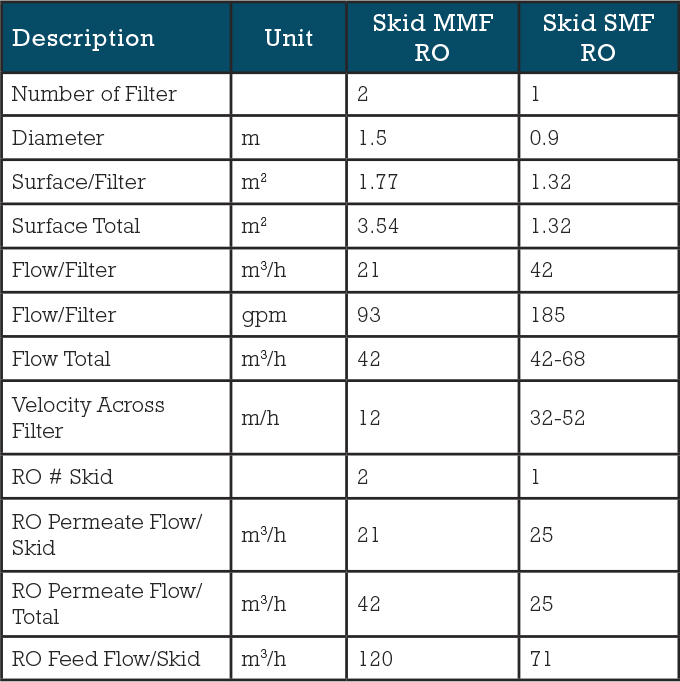
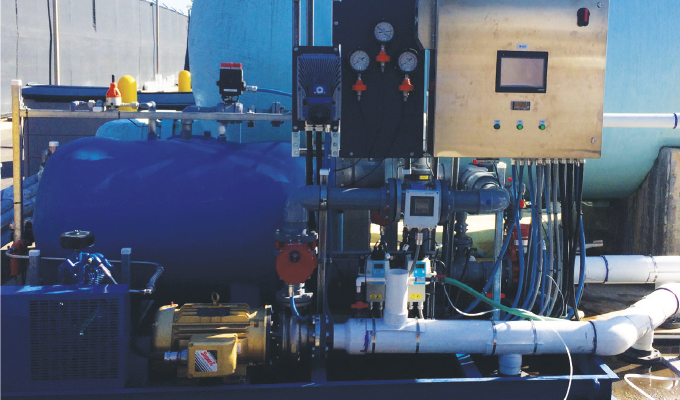
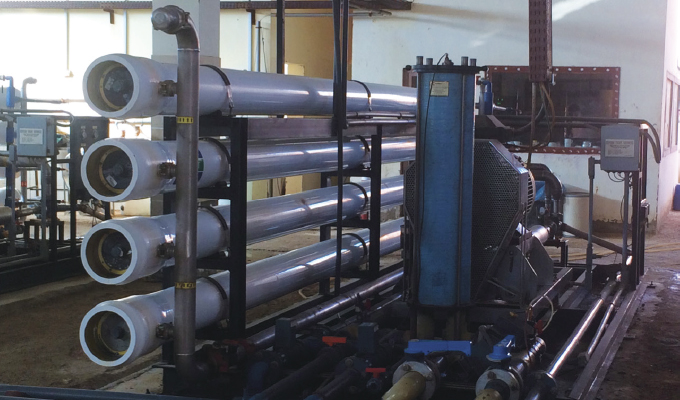
RAW SEAWATER CHARACTERISTICS
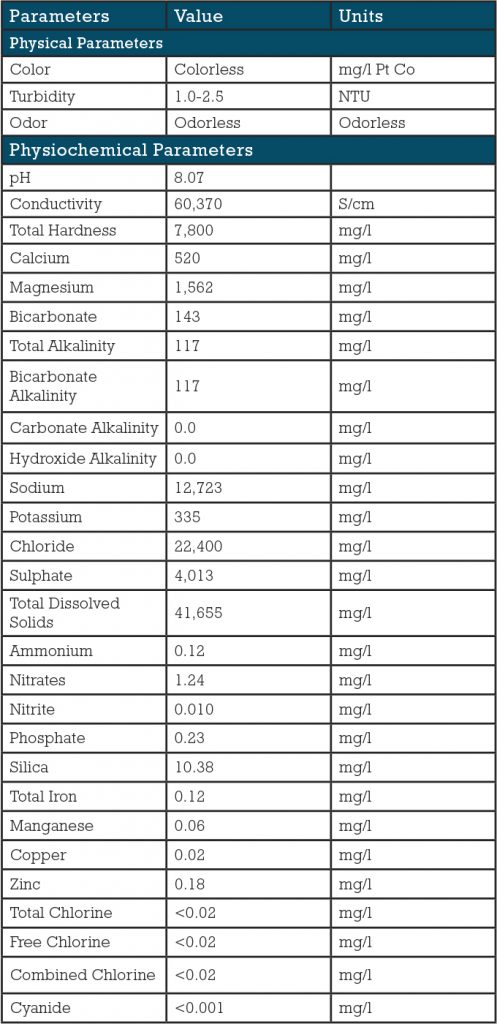
SAMPLING AND MONITORING
Data logging is essential when comparing the field performance of cross-flow microsand filters (CMF) versus multi-media filters (MMF) and observing the impact of the two different pretreated water qualities on the performance of the corresponding downstream SWRO process. Analytical procedures used for monitoring each of the process trains complied with Standard Methods or ASTM methods.
The following table indicates the parameters and sampling frequency used to compare the performance of each pretreatment system:
The following parameters were used to compare the performance of each SWRO train:
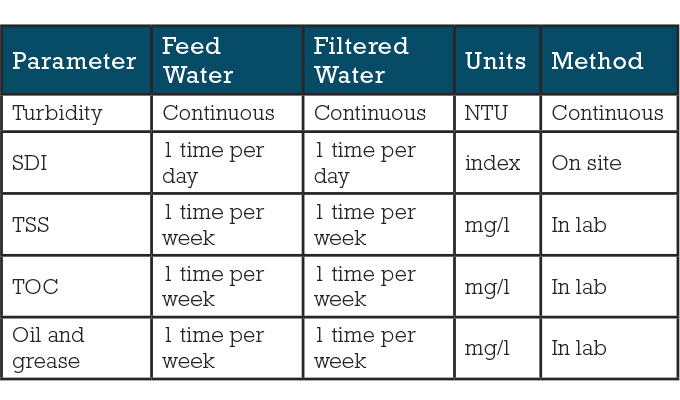
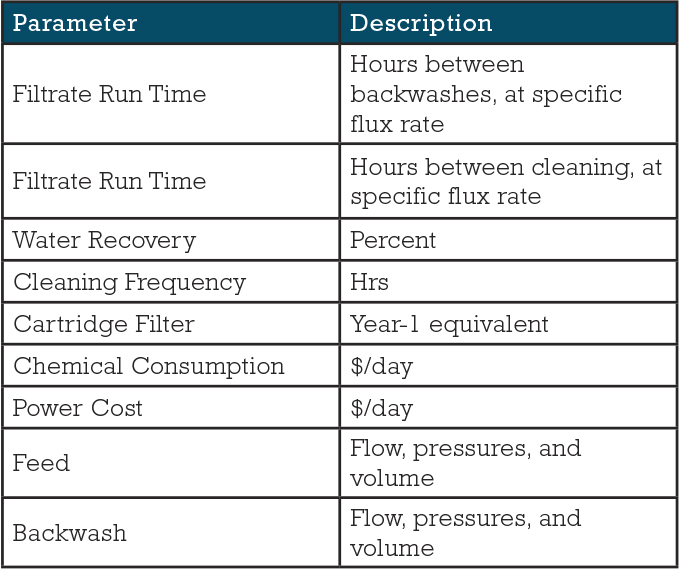
A LOOK AHEAD
Results from this study are presented in three phases, as they were performed and analyzed. Preliminary tests were conducted on the U.S. West Coast to observe and compare the behavior of CMF versus MMF in seawater filtration. Three sampling points were studied: common inlet (raw seawater), CMF outlet, and MMF outlet.
FOR MORE INFORMATION
Siemens Digital Industries Software, a business unit of Siemens Digital Industries, is a leading global provider of software solutions to drive the digital transformation of industry, creating new opportunities for manufacturers to realize innovation. With headquarters in Plano, Texas, and over 140,000 customers worldwide, we work with companies of all sizes to transform the way ideas come to life, the way products are realized, and the way products and assets in operation are used and understood. For more information, visit www.sw.siemens.com.
With more than a 100-year heritage of industry-leading brands and products, technical expertise, and unmatched customer service, Evoqua is the partner of choice for millions of water users across the globe. For more information, visit www.evoqua.com.
MODERN PUMPING TODAY, May 2019
Did you enjoy this article?
Subscribe to the FREE Digital Edition of Modern Pumping Today Magazine!
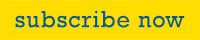