Pump selection for variable flow applications is a little different than choosing a pump for a single duty point. Variable flow applications are just as the name describes–variable flow. Selecting a pump for a single duty point is more defined, in that the pump selected should meet the duty point at, or very near, the best efficiency point (BEP). Pumps are “happiest” when they run near their BEP. They are the most efficient and have their highest life expectancy when they can run near their BEP. But what about variable flow applications?
CHOOSING THE RIGHT PUMP(S)
There is no single duty point for the pump(s), but rather, a range of duty points. Selecting pump(s) for variable flow service is more of an art, in that some considerations must be taken into account:
- NPSH available
- Possibility of the pump system to be oversized or undersized
- What type of pump—single impeller or multiple impeller
When selecting a pump for variable flow service, the duty point used to select the pump value should be to the right of the BEP. The BEP is typically near the center of the pump curve with efficiency dropping as you look to the left and right of the BEP along the pump curve. Selecting a pump to the right of the BEP will allow the pump(s) to operate longer in the best efficiency range with the variable flow demand.
Selecting a pump to the right of the BEP is generally in an area of the pump curve where the pump has an increased NPSH requirement. For this reason not every pump selection for variable flow should be selected to the right of the BEP.
The type of pump is another consideration. Single impeller pumps typically have a flatter curve compared to multiple impeller pumps, and single impeller pumps are less forgiving in situations where conditions change and the pumps are undersized. An oversized pump with VFD control can be electronically “trimmed,” where the maximum speed is reduced to eliminate the possibility of the pump running off its curve. The steeper curve of a multiple impeller pump will allow for a greater opportunity for speed reduction at lower flows and help increase the pump(s) flexibility to meet a changing design pressure requirement. Multistage pumps are more service-friendly than single impeller, end suction pumps. A multistage pump paired together with VFD control, is an ideal choice for variable flow pressure boosting.
PROPORTIONAL PRESSURE CONTROL
Municipal domestic water pump systems tend to have a substantial amount of head requirement dedicated to pipe friction loss. Combine VFD pump control and proportional pressure control (pipe friction loss compensation) and large savings can be realized. Proportional pressure control provides better efficiency throughout the flow range, and can help reduce problems associated with high pressure, which can happen when flow rates are low relative to the design conditions.
Pump systems are typically oversized from the start, and when safety margins are included, most pump systems are larger than what is required. Municipal pump systems with large pipe networks are often purposely oversized to be prepared for future growth. The head requirement for the pump system is calculated by the future high flow design conditions (i.e., future flow capacity and head at the furthest user or highest pressure drop scenario). Then a pipe friction loss calculation is made using the future growth requirement and the pipe friction head is added to the design condition. This conventional process can result in a large pump system using more energy than necessary.
Figure 5 shows a four-pump system with a maximum design condition of 2,200 gallons per minute at 115 psi boost or 266 feet. If the design pipe friction loss of the system is 20 percent of the total required boost pressure (266 feet), using proportional control, the pressure boost at 400 gallons per minute is 212 feet.
Proportional pressure control can decrease the pressure at lower flows and increase it at higher flows where it is needed to compensate for pipe friction loss as shown above.
If the pump system had the lower flow rate duty of 400 gallons per minute for 50 percent of the time and operated seven days a week; using the cost of energy of $0.10 KWh, it results in a savings of $2,592 a year based on an overall motor/VFD efficiency of 88 percent. In addition to energy savings, proportional pressure reduces leaks and saves water at low flow periods by reducing the system pressure.
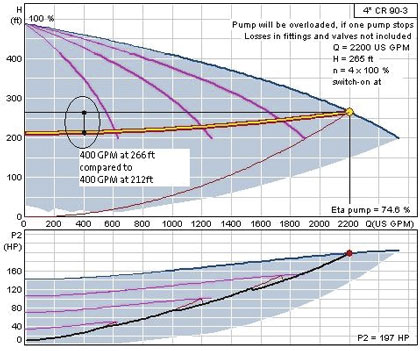
Figure 5
CONCLUSION
VFD-controlled pump systems offer smooth pressure control with energy savings and the ability to match the flow profile to multiple pumps without waste. Systems with multiple pumps deliver variable flow requirements at an increased efficiency over the entire flow range. This is why it is important to understand the specific flow consumption profile of the installation. For example, if the flow rate is constant, then a single-service duty pump operating at its BEP can be used, and VFD-controlled pumps would not be the most efficient control, but may be desirable for other reasons. VFD-controlled pumps and pump systems may not be the best for all applications, but for variable flow applications such as domestic water pressure boosting, they really do have the ability to save energy and decrease maintenance costs.
CASE IN POINT
The city of Cottonwood, Arizona, nearly doubled its population between 1990 and 2010, which put significant strain on the community’s aging water delivery system.
Residents were faced with frequent water outages that would last a day or two, as well as inconsistent pressure and continual water hammer noises in their homes.
The majority of pumps in the city’s existing distribution system were constant speed, across-the-line pumps that were either off, or running at top speed. The resulting pressure surges subjected the pipes to a 25 psi pressure swing, which stressed and prematurely aged the lines (some dating back to 1930), causing significant leakage and capital repair costs.
The city replaced the old, inefficient pumps with the Grundfos Hydro MPC BoosterpaQ. These integrated pumping systems utilize an advanced controller to adjust pump speed and to stage additional pumps to meet fluctuating system demand.
Overall, eliminating pressure surges in the system has slashed the number of pipe breaks and leaks for Cottonwood by 30 percent or roughly $38,000 in capital repairs. Moreover, the proportional pressure setting lowers water pressure/volume during off-peak demand cycles, such as overnight, which translates into less wear-and-tear on the community’s pipe infrastructure, as well as less water lost to leaks.
Moreover, the level of “unaccounted water”—which refers to the difference in the amount of water extracted versus the amount of water billed to customers—has dropped to 11 percent from 40 percent, helping to bridge the water crisis facing the southwest.
ABOUT THE AUTHOR
Brian James, P.E., is business development manager and Roger Weldon is service engineer for Grundfos Pumps Corporation. Grundfos is the world’s largest pump manufacturer. For more information, visit www.grundfos.us.
____________________________________________
MODERN PUMPING TODAY, September 2015
Did you enjoy this article?
Subscribe to the FREE Digital Edition of Modern Pumping Today Magazine!
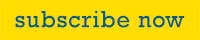