The following report will study the effects of loss of liquid in the wet well during operation of the KPCG-21 progressive cavity grinder pump mechanical seals. The test will also determine the operating capability of the KPCG-21 progressive cavity pump under these conditions, and compare it to that of similar pumps. We will attempt to simulate the conditions created when a float or other level sensing device has become stuck in the “on or run” condition. The pump will drain the wet well and then continue to operate. This can cause a pump to run in a dry condition.
WHAT IS DRY CONDITION RUNNING?
A dry condition occurs when the pump is left in the “on or run” mode after the liquid in the well is removed. This will cause friction on the mechanical seals and between the parts that make up the progressive cavity. It will also cause extremely high temperatures in the pump itself which could damage the pump motor. This condition could go on for days until it becomes apparent that the pump is stuck in the “on or run” position.
Some of these pumps have been run like this for days without any moisture visible on the pumps mechanical seals or wet end parts. This test will show that the KPCG-21 progressive cavity pump is almost completely unaffected by this dry run condition. The superior materials used to build the KPCG-21 can stand up to seven or eight days of this type of abuse and still operate on the published curve.
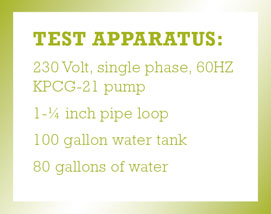
TESTING CONDITIONS
Prior to testing the selected pump will be placed in a test loop and tested for pressure flow and amperage. Please see chart below for results of testing.
First, the EPDM pump stator will be removed. The pump will be placed on a stand, powered up and allowed to run continuously dry without pumping any water.
The pump will be run continuously for an exact amount of time. After the pump has been run for the specified amount of time the EPDM stator will be reinstalled and the pump will be placed in a tank and allowed to cycle water to ensure there are no seal failures and that it still pumps fluids.
Next, the pump will again be allowed to run dry for an additional period of time with the EPDM stator installed. Once the specified amount of time has been reached the pump will be retested for pressure, flow, and amperage to determine if the pump has received any internal damage.
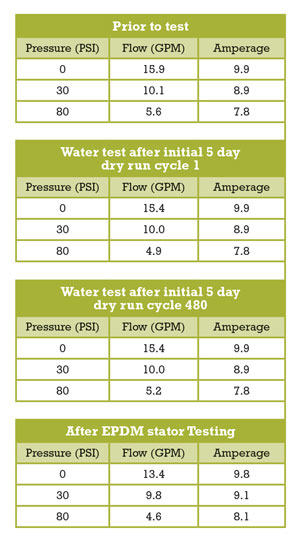
TESTING PROCEDURE
First, the EPDM stator was removed from the pump. 230 volt, 60 HZ single phase power was applied to the pump. The KPCG-21 progressive cavity pump was set up and started. It was allowed to run dry in the atmosphere for a continuous five days. At the end of the fifth day the EDPM stator was reinstalled and the pump was placed into the tank. The tank was filled with water and the pump was started and allowed to run for an entire day on one minute cycles totaling four hundred and eighty cycles. Flow, pressure, and amperage were noted at cycle one and cycle four hundred and eighty, please see chart below for results.
The pump was allowed to drain the tank. A valve was closed to keep water from returning to the tank and the pump was again allowed to run dry. This time the pump ran dry for a period of four hours with the EPDM stator installed. The pump was allowed to run continuously for exactly four hours. At the end of 4 hours the pump was removed from the tank, cleaned, and then retested for pressure, flow and amperage. See the chart below for results of the tests.
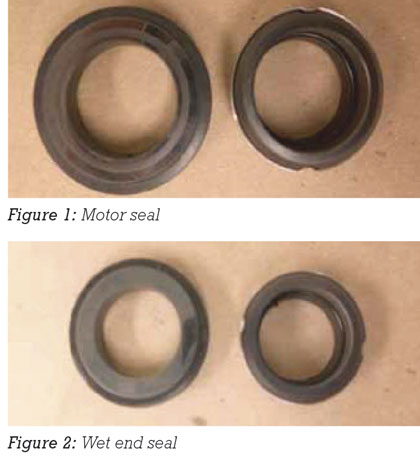
OVERVIEW OF RESULTS
From the results, we see that the KPCG-21 progressive cavity pump suffered only a slight decrease in flow, but was unharmed in pressure or amperage. Upon inspection of the internal parts we found that the EPDM stator suffered only slight deformity but was still functioning with over three quarters of the pump cavity completely unharmed. Both of the seals were completely unharmed and sound. There was no water allowed into either the bearing or the motor housing. As can be seen in figures 1 and 2, the seals received no damage from any phase of the testing.
For More Information
Serving the wastewater industry since 2004, Keen Pump Company, Inc. is a manufacturer of submersible sewage pumps for the residential, commercial, industrial, and municipal markets. Keen Pump provides complete residential and commercial fiberglass basin packages. These systems are complete with the pumps, lift-out slide rail system, discharge piping, junction box, level controls and brackets, and control panels. For more information, visit www.keenpump.com.
____________________________________________
MODERN PUMPING TODAY, July 2017
Did you enjoy this article?
Subscribe to the FREE Digital Edition of Modern Pumping Today Magazine!
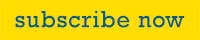