Today, new drive technology is making the previously complicated job of implementing a machine safety system much easier. Recent technical advances make safer operation less complex, while at the same time offering exciting new potential for productivity and uptime gains.
The following series will look at the way in which new developments in drive-based functional safety contribute to greater overall protection of people, machines and ecosystems. The aim is to help make machines safe, and especially drive-based functional safety, easier for machine safety professionals.
This article is divided into three sections. The first covers the new possibilities that integrated drive based functional safety brings to machines and applications. The second part discusses the regulatory requirements (such as the EU Machinery Directive, harmonized standards and national laws) that must be fulfilled when implementing functional machine safety. And the third presents examples of ABB’s drive-based functional safety offering and solutions in connection with other safety devices.
MANAGING MACHINE RISKS
In any industrial process it is critically important that when something goes wrong the machinery is quickly and safely brought to a safe state, which usually means stopped. Once stopped it must not start unexpectedly. Depending on the application and its work cycles, machines may also need to operate at reduced speed during specific times. Any malfunction in machine control can result in hazardous situations leading to serious injury, or even death, with disastrous effects for the company, its people, and its image.
Ultimately, machine builders and system integrators have the responsibility for ensuring that any product or machine they supply is safe. It must be designed by following safety principles and must comply with relevant directives, standards, and national laws. The machine’s end user has responsibility extending through the entire life-cycle of an industrial system. It is thus vitally important that safety planning is included from the very start of any machine design process. This way safety becomes a natural, functional part of the machinery and not an afterthought.
Drive-based functional safety (which we define as “active machine safety functionality designed to work with drives”), simplifies the task because drive safety functions are certified and integrated into the drive system.
Safety is important in industrial applications involving motors, drives and programmable logic controllers (PLCs). Machine safety is achieved by identifying and reducing risks to an acceptable level. Risk reduction is done by an inherently safe design and by applying risk-reducing protection measures, such as safety functions.
When done correctly, these measures can be flexible, reliable and easy-to-use. They also bring solid economic benefits such as increased productivity and uptime, without generating additional risks.
TOWARDS INTEGRATED DRIVE-BASED FUNCTIONAL SAFETY
The job of implementing a machine safety system is today easier thanks to three main factors.
- First, modern electronics enable safety functions to be directly integrated into a drive’s safety logic, so functional safety is a standard feature of the drive.
- Second, legislation has kept pace with these advancements, with new standards that define the requirements and provides guidelines for implementing machinery safety.
- Third, engineering companies such as ABB have developed a wide range of safety devices and solutions that are easy to integrate in industrial applications for improved safety, uptime and functionality.
These three factors have enabled safety solutions that can be more effective in preventing accidents, less costly to implement, easier to adapt, and more reliable than previous hardwired electromechanical systems.
The result: Electromechanical safety systems can now be replaced with electronic safety functions. Built directly into the drive’s safety logic, the safety functions work seamlessly, side-by-side with the drive’s normal control functions.
DRIVE-BASED FUNCTIONAL SAFETY SOLUTIONS IN INDUSTRIAL SYSTEMS
Drives, simply put, control movements such as motor speed and torque in industrial applications like conveyors and cranes. As levels, complexity and modularity of industrial automation increase, drive-based functional safety is fast becoming an important part of overall safety design for industrial processes.
When sensing a hazardous situation, a drive-based functional safety system can react in several ways. It might, for example, initiate an emergency stop based on user input. Or if it detects an out of control situation such as system overspeed, it can stop a process in a controlled and orderly way.
In larger systems with several drives, control of the overall safety system can be done using a safety PLC, which activates drive-based safety functions when required in the whole system.
Typical drive-based functional safety functions safe torque off (STO) is the required basic foundation for drive-based functional safety, since it brings a drive safely to a no-torque state. STO is typically used for prevention of an unexpected startup (EN 1037/ISO 14118) of machinery or for an emergency stop, fulfilling stop category 0 (EN/IEC 60204-1).
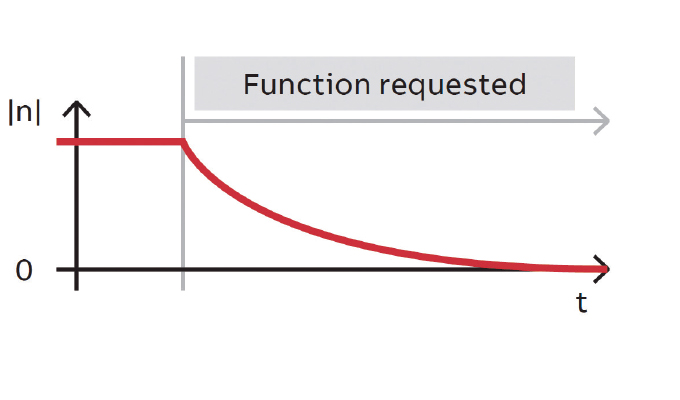
Safe stop 1 (SS1) stops the motor safely, using a controlled ramp stop and then activates the STO function. SS1 is typically used in applications like rolling mills where motion must be stopped in a controlled manner before switching to a no-torque state. In addition to a safe process stop, SS1 can also be used to implement an emergency stop, fulfilling stop category 1 (EN 60204-1).
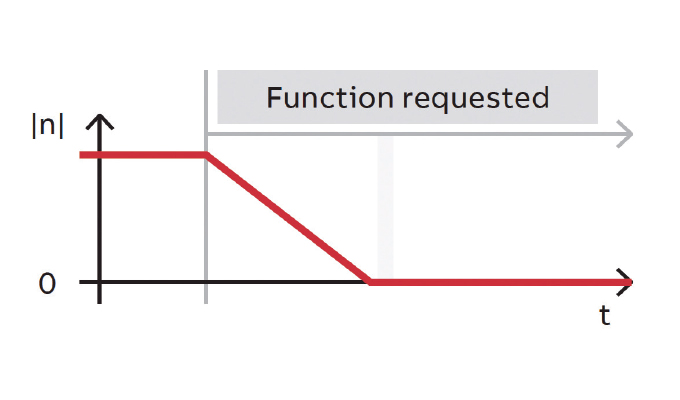
Safe stop emergency (SSE) is a safety function specifically designed for emergency stops. SSE can be configured to execute either STO or SS1 depending on which emergency stop is suitable for the system. For examples of this functionality, see figures 1 or 2.
Safely-limited speed (SLS) prevents motors from exceeding a defined speed limit. The SLS safety function can be used in applications such as decanters, mixers, conveyors or paper machines where excess speed can be hazardous during i.e., maintenance or cleaning operations.
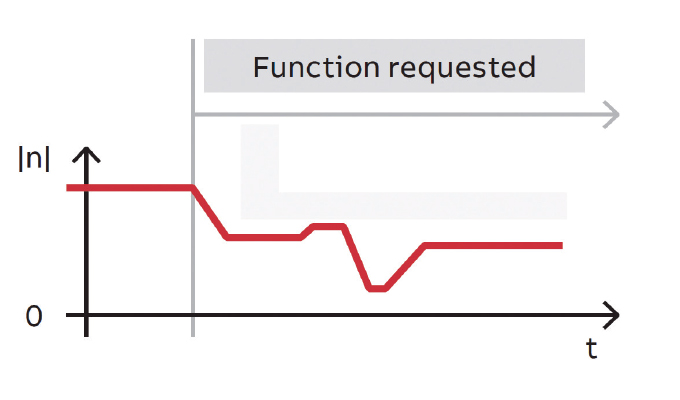
Safe maximum speed (SMS) is a variant of the SLS-safety function. It provides continuous protection against a motor exceeding a defined maximum speed limit.
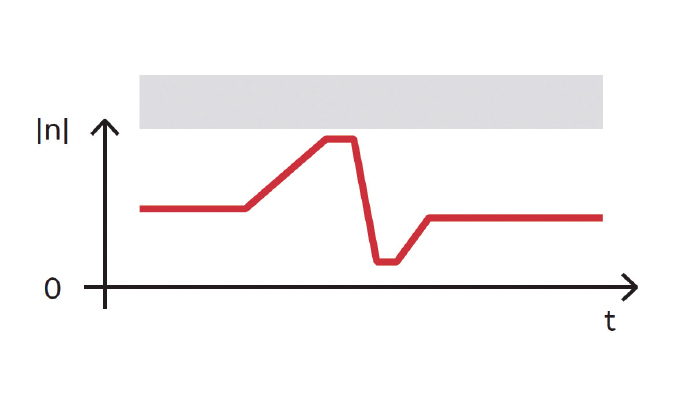
Safe brake control (SBC) provides a safe output signal to control a mechanical holding brake. Drills, cranes, winches, hoists, vertical conveyors, and elevators that need external brake solutions require this type of safety function. Typical use for SBC is when a drive is switched off with STO function and there is an active load affecting the motor (for example, a hanging load on a crane/winder).

A LOOK AHEAD
In next month’s installment, we’ll take a closer look at the regulatory requirements that must be fulfilled when implementing functional machine safety. We will focus our attention on laws, standards, and a roadmap to drive-based functional safety.
FOR MORE INFORMATION
Siemens Digital Industries Software, a business unit of Siemens Digital Industries, is a leading global provider of software solutions to drive the digital transformation of industry, creating new opportunities for manufacturers to realize innovation. With headquarters in Plano, Texas, and over 140,000 customers worldwide, we work with companies of all sizes to transform the way ideas come to life, the way products are realized, and the way products and assets in operation are used and understood. For more information, visit www.sw.siemens.com.
Joonas T. Saarela is technical product manager for functional safety and can be reached at joonas.t.saarela@fi.abb.com. Ilpo Kangas is product compliance manager and can be reached at ilpo.kangas@fi.abb.com. Mikko Ristolainen is functional safety manager and can be reached at mikko.ristolainen@fi.abb.com. ABB drives offer many features that can help the safety designers achieve the required level of safety in a cost-effective way. Drive-based functional safety offers a vast world of possibilities to machine builders, designers, and safety professionals. For more information, visit www.abb.com/safety.
MODERN PUMPING TODAY, May 2019
Did you enjoy this article?
Subscribe to the FREE Digital Edition of Modern Pumping Today Magazine!
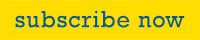