The rendering business is not known for its glamour or its cutting edge technology, but in North America’s first project of its kind, that’s all about to change for an industry that is positioned for growth.
SMART DECISIONS, GREEN TECHNOLOGY
Biogas Energy have built an anaerobic digestion (AD) facility at North State Rendering in Oroville, California that is already paying dividends, with uninterrupted biogas generating electricity, fuelling trucks, and running boilers. The economics seriously stack up—not to mention the massive reduction in carbon footprint.
“For a rendering plant, biogas is a natural fit,” says Brian Gannon of Biogas Energy. “North State Rendering were looking for ways to cut costs, secure new waste supply contracts, and improve wastewater treatment, so creating their own on-site biogas facility was a wise move. Fuel and energy are a significant operational cost for the business, so investing in technology that eliminates electricity bills, slashes diesel costs and reduces natural gas imports all makes sense. Modifying the anaerobic digestion process to integrate with a rendering plant took some fine tuning, including a very positive modification to the digester’s mixing system, but now, we see how we got it right.”
WASTE RECEPTION AND PRE-PROCESSING
Grease trap waste and food waste from kitchens, restaurants, and food manufacturers is expensive to render, so by diverting this material to the digester, North State Rendering reduces costs and frees up rendering capacity for higher-value materials.
The waste reception equipment prepares high-solids feedstocks for the digester, whilst a grease trap reception system separates out contaminants such as plastic and metals.
With this flexible reception facility configuration, the digester can process a wide variety of materials, from food and yard waste to high-liquid grease trap material. Wastewater from the rendering process is also added to the mix. North State Rendering can also add dead stock to the digester during warmer months when rendering can become problematic due to extreme degradation of the material.
ANAEROBIC DIGESTER TANKS
From the reception area, the material is pumped into two tanks (40 feet [12.2 meters] diameter by 24 feet [7.3 meters] high), where the first acid-forming phase of the biogas production process takes place.
These heated tanks contain bacteria that break down the material and prepare it for the main digester tank, which stands 64 feet (19.5 meters) tall. When the material is ready, it is pumped into the main digester where biogas-producing bacteria get to work.
Brian Gannon continues: “We had been using submersible propeller mixers inside our main digester, but with our re-design of the tank, we switched to a new system that meets all of our needs. One of the main issues with submersible digester mixing systems is that the equipment is inside the tank, which from a maintenance point of view is a nightmare. The downtime caused by having to open the digester to lift the mixers out for repairs and maintenance caused serious process interruptions and safety issues.
“We now have a Landia digester mixing system, which is mounted externally, so maintenance is much easier. Even during commissioning when the AD biology was at a delicate stage, we were able to carry out some tweaks without any interruption whatsoever to the biogas production process. With submersible mixers we would have had to start over again, which would have been very expensive and used up a ton of manpower.”
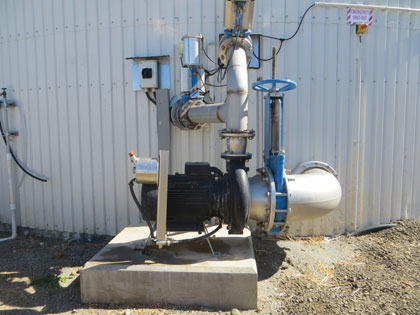
Landia’s externally mounted GasMix at North State Rendering.
POWER IN THE PUMP
In addition to its ease of maintenance, Brian also points to the Landia (patent-pending) GasMix System being able to agitate the entire digester tank (especially one 64-feet high!), whereas other units often cannot prevent a crust from forming on the top level of the tank’s contents.
“The anaerobic digestion facility is designed to process a very wide range of feedstock,” he says, “so its pumps and mixers have to cope. The Landia chopper pumps, which form part of the GasMix system, are absolute troopers. They just keep on working. We wouldn’t be achieving what we are now without them.”
Comprising two 30-horsepower chopper pumps and a self-aspirating system that reduces solids to produce more methane in a much shorter time period, Landia’s GasMix (designed specifically for AD/biogas) is easy to regulate and also offers significant energy savings because it only has to run for a maximum of 30 percent of the installed capacity.
Brian also explained that the anaerobic digester is not only producing biogas, but processing wastewater to improve water quality. The bacteria creating biogas digest is the material that causes elevated COD in wastewater. Hence, the digester also acts as a small wastewater treatment plant, improving the quality of wastewater and enabling reductions in discharge fees.
“We generate enough electricity to power the entire North State Rendering plant,” adds Brian. “Heat from the generator is also used to heat the digesters, so we’re able to optimize energy efficiency.”
ENERGY AND FUEL PRODUCTION
Biogas Energy estimates that North State Rendering will reduce diesel costs by 75 percent by introducing a gas-cleaning skid to create a pipeline-quality biomethane that is then compressed in a CNG fueling station.
As the biogas-to-CNG upgrade system produces pipeline-quality natural gas, producers can inject the gas into the pipeline to sell to other customers. Finally, any surplus biogas is fed to a boiler at the rendering plant to reduce the need to purchase natural gas. With a diverse use for the biogas, North State Rendering will maximize revenue and hedge against price increases in electricity, diesel, and natural gas.

Biogas digester at North State Rendering.
SOURCES OF FACILITY FUNDING
For its new anaerobic digester, North State Rendering was able to take advantage of grants from the California Energy Commission’s Alternative and Renewable Fuel Vehicle Technology Program.
State and federal inducements can also include tax incentives, sales tax exemption, grants for renewable energy project and truck conversion costs, and incentivized electricity production pricing.
Brian Gannon concludes: “Renderers have a big head-start over other companies trying to develop new waste-to-energy facilities. Unlike newcomers, renderers already have the necessary permits in place to process waste material. They also have the trucks to collect waste, and the energy consumption that biogas facilities can help fuel.
“As energy and fuel prices climb and wastewater discharge fees escalate, waste processors can turn waste into an asset. For Biogas Energy, our experience at North State Rendering and the introduction of Landia’s GasMix digester mixing system means that we can help our clients generate renewable energy with a system that maximizes production while facilitating operations and maintenance.”
About The Author
Soren Rasmussen is the director of Landia, Inc. For more information about Landia’s range of applications, call 919.466.0603, email info@landiainc.com, or visit www.landiainc.com. For more information about Biogas Energy, visit www.biogas-energy.com.
MODERN PUMPING TODAY, March 2015
Did you enjoy this article?
Subscribe to the FREE Digital Edition of Modern Pumping Today Magazine!
