Read Part 1 here.
In last month’s introduction, we laid out how, in the face of recent record-breaking natural catastrophe claims and damage from extreme weather events, some insurance firms have stopped underwriting renewable projects, while others are increasing premiums to far higher levels. This is a serious problem for the sustainability of both the energy sector and its profitability. This guide offers a roadmap to natural disaster plant restoration, with actionable strategies to keep plant revenue loss under control. To reiterate, although no one can control the weather, what operators and facility managers can control is their level of preparedness and how to plan for recovery.
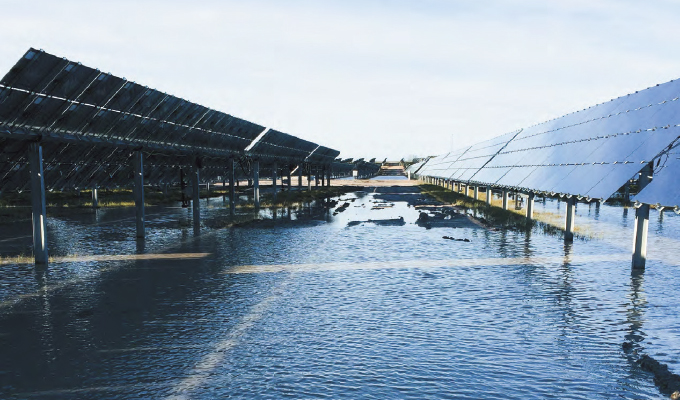
CASE STUDY: SALVAGING SOLAR FROM FLOOD
Whipping winds, torrential downpours, power outages, and floods—hurricane season can be punishing. And with 2020’s Atlantic hurricane season ranking as the most active on record, owners of utility solar plants are bracing themselves for costly damages in the future.
When two hurricanes swept through the Southeast in 2018, one asset owner faced torrential rainfall and massive flooding at its 92-MW PV plant. The damage was severe: Ten of forty power conversion stations were inundated with 12 to 18 inches of water and remained flooded for several days.
The operator took all of the plant’s inverters offline before the hurricanes roared through, generating condensation inside all of them. Consequently, when the inverter manufacturer inspected for damage at the plant, it voided the warranty on all forty inverters—instead of the ten flooded units—abruptly denying responsibility for any of them.
Depcom’s restoration teams looked at all aspects of the project to keep costs and revenue loss to a minimum. From damage assessment and salvage planning to rapid restoration, they quickly assessed the situation: Condensation in the inverters was the long-term result of poor design and not negligent maintenance, as the OEM reported.
Depcom equipment specialists determined that the doors on the damaged units were not sealed properly, allowing humid outside air to seep in, resulting in condensation. With this expert documentation in hand, Depcom provided the critical proof that the units had preexisting design issues, compelling the OEM to restore the warranty on the 30 inverters that had not flooded. Insurance covered the ten flooded inverters.
Facing significant production losses already, the plant owner and its insurance partner were on track to replace the flooded inverters. But Depcom’s specialists offered a different solution: Salvage and refurbish the units and save a whopping four million dollars in equipment replacement costs. The insurer approved the plan, but wanted to be sure the inverters were flood-proof. The most cost-effective solution? Elevate the concrete pads supporting the units by three feet for a fraction of the replacement cost.
One of Depcom’s unique strengths is prioritizing workflow to minimize revenue loss. In this case, it applied a strategic approach to move the restoration worksite to an area that would not hamper power production in other sections of the site.
As one of the country’s leading EPCs with more than 1.5 GWs of operational solar projects, Depcom can mobilize quickly. It deployed its 24/7 operational crews to the site to lift the pads in just six weeks, far faster than the twenty-two-week lead time required to install new inverters. This efficient solution minimized business interruption and got the flooded portion of the plant back online.
Depcom’s ability to rapidly return the plant to production resulted in $400,000 to $700,000 more revenue than waiting for delivery of new inverters. Combined with the $1.8 million savings from salvaging the flooded units, Depcom’s fast restoration plan resulted in total savings of more than $2.5 million for the asset owner.
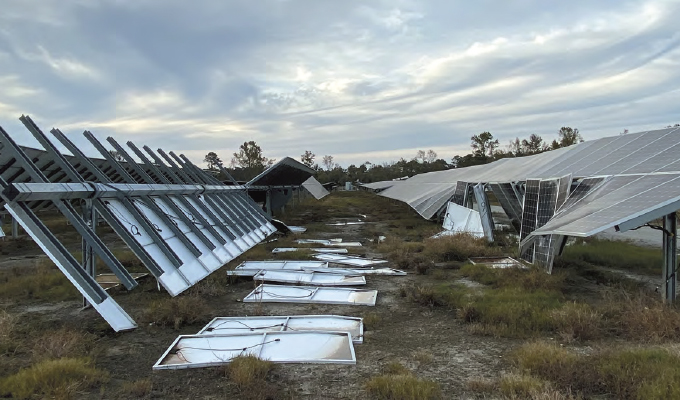
CASE STUDY: SURVIVING THE STORM
When a rogue storm battered a PV power plant with winds up to 80 miles per hour, damaging 233 of the site’s 1,600 trackers, it quickly became clear that consistent and thorough maintenance practices had not been observed prior to the damage. As a result, more than 15 percent of the plant’s trackers weren’t operational before the storm, making it impossible to stow them into a protective position to minimize damage.
Despite that failure, the asset owner initially relied on O&M personnel to assess the damage and file insurance claims. But four months after the storm, with huge swaths of the plant still not operating and finances beginning to sink into the red, restoration work had yet to begin. That’s when Depcom’s Repowering+ team was asked to step in.
As one of the country’s leading EPCs with more than 1.5 GWs of operational solar projects, Depcom can mobilize quickly. Within four weeks, our recovery experts had a plan in place and were powering through the work.
Specialists deconstructed the damaged areas and conducted testing to determine what components could be salvaged and repaired versus what needed to be replaced altogether. Because of its deep supply network, Depcom was able to establish reliable and fast delivery for the required replacement parts. Equipment also was readily available through Depcom’s extensive inventory of spare parts on hand at regional warehouses.
Of equal importance was Depcom’s early work with a key stakeholder too often brought in late in the process—the plant’s insurance carrier. By establishing an ongoing dialogue with insurance adjusters, Depcom was able to keep the many moving parts in alignment while streamlining critical insurance payouts.
Ultimately, Repowering+ experts seamlessly married original, salvaged parts with new, modern equipment to bring the site completely back online without a significant (and costly) redesign. Such a complex accomplishment would not have been possible without our extensive restoration experience, which has allowed Depcom to consistently uphold every energy production guarantee after an extreme weather event. The flexible restoration plan minimized revenue loss while keeping much of the plant operational to maximize production throughout the repair process.
The final upshot: Savings of $3.3 million over the initial forecasted budget. While the plant’s owner had anticipated replacing roughly $1.75 million worth of damaged components, Depcom was able to develop a salvage plan for the bulk of the modules that resulted in $1.3 million in savings, recovering 70 percent more modules than anticipated in the original budget.
Recovery following an extreme weather event is complex, often even more so than initial plant construction. Unlike in new builds, recovery and restoration involve an intricate balancing act between current production needs and restoration demands. Depcom has found that balance time and again. In this case, additional savings came from reduced business interruption claims, a more efficient timeline than was originally forecasted, and a staggered workflow to prioritize production.
Depcom’s restoration efforts resulted in additional savings from reduced business interruption claims, a more efficient timeline, and a staggered workflow to prioritize production.
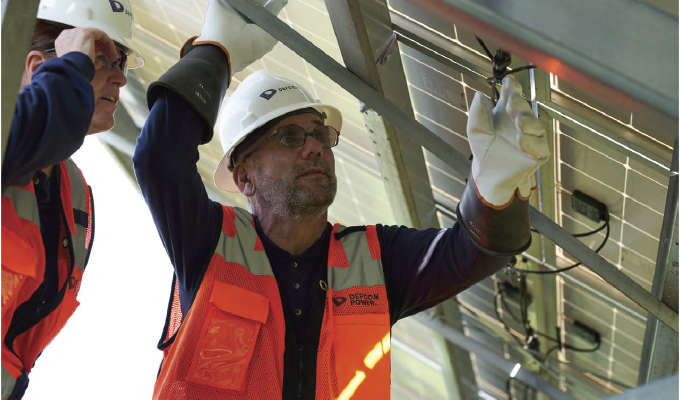
CASE STUDY: REPOWERING INVERTERS AFTER SEVERE FIRE
When a catastrophic inverter fire took down all production at a five-megawatt PV plant in Durham, North Carolina, there was no way to know how or why the fire ignited. Although it was clear that the flames had started inside the inverter cabinets, damage to both power conversion stations was so severe that it was impossible to determine the root cause.
Because the plant was commissioned in 2014, much of the original equipment is no longer made. The site was designed around now-obsolete 1000-volt DC inverters, while today’s plants are developed using 1500-volt DC systems.
Forced to work with a lump-sum payout from their insurers, the asset’s owners needed a plan—and fast. Under the power purchase agreement with the local utility, there was a limited grace period allowed before production had to be restored. If that deadline was missed, the PPA could be voided entirely.
Unlike other contractors that quote a price at the outset and then modify it with change orders as issues stack up, Depcom’s plant repowering expertise allows the EPC leader to cover the full scope of the project for a guaranteed price up front.
As the project started, Depcom’s Repowering+ team determined that the four destroyed one-megawatt central inverters were no longer manufactured. Instead, they devised a plan to reuse the existing skid base and consolidate the four old units into two new inverters with a higher power density—reducing the project’s timeline and avoiding considerable construction costs.
Depcom’s strategy simplified the overall system design, minimizing the balance-of-system materials required and reducing the AC bus work and components needed, to create overall savings in installation costs. These savings offset the higher cost of manufacturing new 1000-volt inverters, which are now much more difficult to source and require components and materials no longer readily available.
Because the plant had to be partially redesigned, both local regulators and the contracting utility required that the facility meet all current standards and codes. This meant registering entirely new permits, updated testing, and a repeat approval process as if the plant were being commissioned for the first time.
Depcom Power brought in its repowering experts to mitigate the damage fast. Leveraging its EPC and O&M capabilities allowed Depcom to complete the permitting process efficiently, engineer and design the restoration rapidly, source new equipment, and remove damaged equipment. Timing was of the essence to complete the installation and fully test the new operation.
Ultimately, Depcom was able to bring the plant back online before the PPA grace period expired, preserving the contract. Because work was completed within the budget set by the insurance company, the asset owner had no out-of-pocket expense beyond paying the deductible.
DON’T WAIT FOR NATURAL DISASTERS TO STRIKE
Site recovery takes more than cobbling pieces back together again after a disaster; it involves complex processes that demand unique skills and expertise beyond simple construction. Planning ahead can make the difference between struggling to get back online and coming back at full strength. To weather whatever storms may come, plant owners should screen potential partners today and enlist their help to develop contingency plans for critical equipment and parts, safeguarding future profitability.
As a market leader in natural disaster management, Depcom’s repowering team helps asset owners restore damaged solar assets for maximum profitability.
FOR MORE INFORMATION
Jamie Alexander is senior vice-president of services at Depcom Power, which serves the solar and energy storage market by providing traditional O&M services, restoration of sites impacted by natural disasters, repowering of sites underperforming or experiencing catastrophic failures, and specialized services focused on inverter commissioning and repair. Alexander’s twenty-five years of industry experience includes OEM equipment design and manufacture, project development, construction, and operations and maintenance. Having worked exclusively in the solar and energy storage sector for the past twelve years, Alexander has been involved in the deployment of almost 3 GWs of assets. For more information, visit www.depcompower.com.
MODERN PUMPING TODAY, August 2023
Did you enjoy this article?
Subscribe to the FREE Digital Edition of Modern Pumping Today Magazine!