Whether it’s wildfires, hurricanes, or hail, natural disasters devastate solar power infrastructure. Particularly for asset owners of utility PV, extreme weather can cause significant downtime, repair costs, and revenue loss.
Last summer was the worst on record for natural catastrophe claims, with far more damaging unmodeled extreme weather events. Hail losses in Texas alone last year caused about $300 million in solar damage, nearly ten times the estimated losses from Hurricane Hanna in 2020. These weather events are causing some insurance firms to stop underwriting renewable projects, while others are increasing premiums to far higher levels.
When floods recede and winds die down, owners of solar assets need fast mobilization, plant recovery experience, and repowering expertise to get crucial assets back online rapidly.
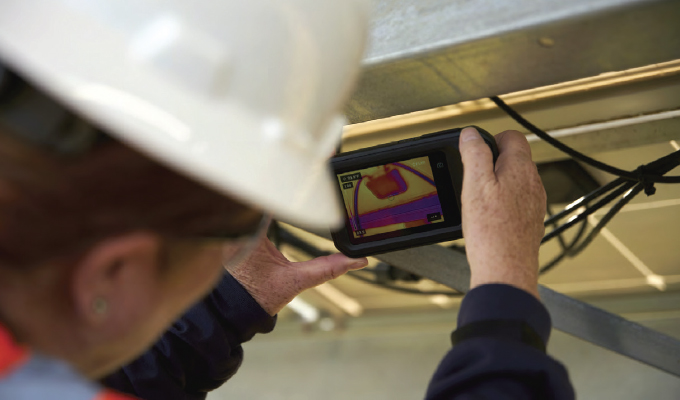
BEST PRACTICES FOR EFFICIENT RESTORATION
Assess and Document Damage
First impressions can be misleading. What appears as minimal damage may conceal more significant issues. Document and take pictures of everything that may require attention. Note components that are obsolete and determine which OEMs will play significant roles moving forward. Consider a high-resolution aerial scan to map the destruction, including infrared views to identify thermal problems. Insurance often covers this because they want to know what they’re dealing with just as much as you do.
Save with Salvage
Before work begins, establish standards for testing damaged equipment and criteria for what warrants repair and what needs replacement. The right restoration partner will have the expertise required to implement these procedures. Salvaging components requires flexibility. Maintain quality, but watch for opportunities to continue using viable parts. For instance, instead of replacing an entire inverter, explore options to re-energize the equipment. Successful salvage can save hundreds of thousands of dollars over replacement
Balance Production with Restoration
It’s critical to get portions of the plant operational to restore revenue streams while restoration continues elsewhere on the site. When possible, stagger the work to prioritize production; if one inverter is down simply because of a ground fault, but the rest of the array is in good shape, prioritize restoration there to get that section of the plant back online.
Repair and Replace Old with New
Ever-improving technology helps move the industry forward, but it also means that new equipment is not always backward compatible. It’s tricky to blend legacy equipment that’s no longer available with modern components. Creative engineering solutions that blend older units with state-of-the-art technologies can keep costs in check. Look for a partner with the expertise required to weave still-functional older parts in with newer PV technology.
Mitigate Equipment Supply Risks
Today’s ‘perfect storm’ of supply chain and inflation challenges exacerbates the complexity of extreme weather claims. A partner with EPC capabilities can streamline the wait for parts, ensuring availability through Tier 1 procurement agreements. Especially with today’s supply constraints, you need experts with a deep supplier network and, ideally, an extensive inventory of spare parts on hand at regional warehouses.
Make Insurance a Recovery Partner
Insurance adjusters often are brought in too late. Instead, establish a relationship with your carrier early to ensure familiarity with PV best practices and align all stakeholders throughout the project. Getting insurance up to speed from the project’s genesis makes it easier to streamline the claims process and support fast, optimal insurance coverage. Select an experienced recovery partner that can help save valuable time by managing insurance claims.
Guaranteeing Profitability After the Crisis
Ensure strong post-recovery performance with in-house engineering teams, designers, construction management, and supply networks all under one umbrella. It’s not enough to meet energy production guarantees after restoration. Partners with O&M capabilities bring additional plant operation solutions for long-term maintenance, repair, and energy optimization. Repowering expertise can weed out unreliable equipment that diminish plant performance, while recertification programs can extend maintenance to salvage usable equipment and source parts faster than OEMs.
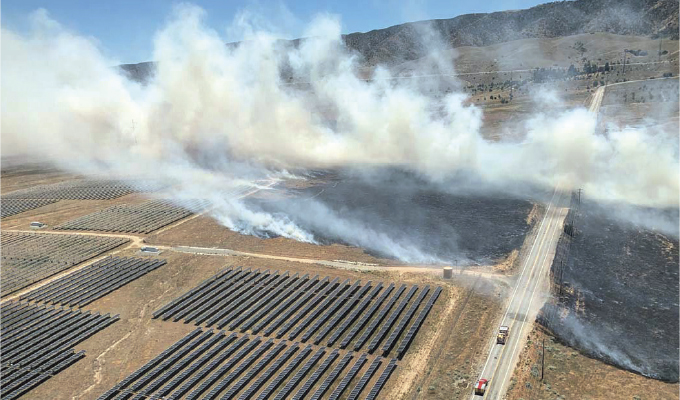
WHAT TO LOOK FOR IN A RECOVERY PARTNER
It pays to bring a restoration expert on board early. Combating force majeure damage requires extensive experience to make swift decisions as well as skilled partner management to secure insurance and warranty support.
Proven Recovery Know-how
Recovery after an extreme weather event is complex, often more so than initial plant construction. Unlike new builds, restoration involves balancing current production needs against deconstruction and replacement demands. Screen partners for expertise in damage assessment, equipment salvage, and insurance claims management.
Solar Construction Experience
Things rarely go exactly to plan. That’s where PV experience is critical. Your partner should be able to troubleshoot and course-correct challenging construction issues before they metastasize. In-house capabilities and a capital equipment fleet can minimize risk and maximize safety, quality, and schedule control.
Advanced PV Engineering
Close collaboration between construction and engineering teams can ensure project success. Demand detailed attention to permitting, civil and structural engineering, plant layout and design, energy modeling and analysis, inverter sizing, and substation size and layout.
Procurement Strength
PV was not spared when the pandemic created supply chain challenges. While that squeeze is easing, the industry is still seeing solar module shortages and logistical constraints that increase supply risk. Look for EPCs with established partnerships with Tier 1 equipment manufacturers.
O&M and Repowering Expertise
Look for cost-effective solutions for short- and long-term maintenance, repair, and energy optimization. A partner with deep repowering expertise can help address diminished plant performance caused by unreliable equipment such as underperforming, damaged, or tough to-source modules and inverters.
CASE STUDY: RAISING PV PLANT FROM ASHES
In 2020, the Western United States experienced one of the most severe wildfire seasons in its history. Fanned by gusty winds and fueled by hot, dry terrain, the fires burned more than ten million acres and caused $19 billion in damage. Solar plants were not spared.
Depcom’s client in Kern County, California, faced catastrophic damage that shut down its 20-MW system. Rampant ground fire destroyed more than 100,000 solar modules, making nearly 200 acres of PV unproductive and unsafe. To tame the flames, helicopters dumped volumes of water on the site, flooding central inverters and other equipment.
Depcom quickly deployed its restoration team to assess the damage on-site, after months offline. With unique plant recovery expertise, Depcom surveyors thoroughly evaluated and documented rows of equipment and swiftly recommended a course of action to salvage, repair, and replace components.
Depcom worked alongside the asset owner and its insurers to prioritize getting a portion of the plant back online quickly. It consolidated salvageable parts to restore segments of the facility while it procured new equipment to replace damaged parts. Unfortunately, the original bill of material and some of the equipment was no longer manufactured. As a result, Depcom had to source, engineer, permit, construct, and commission a hybrid system that wove in older equipment with state-of-the-art PV technologies.
Performing this restoration during the COVID-19 pandemic required extra safety protocols to keep both Depcom and partners safe. Depcom leveraged its deep supply network to overcome pandemic-related supply delays.
Depcom merged in-house EPC capabilities with recovery expertise to balance production demands with deconstruction and replacement plans. This level of collaboration saved the asset owner a total of $2.6 million in restoration and production losses.
Depcom’s extensive restoration experience allowed it to work closely with insurers. The team streamlined the claims process by providing detailed documentation and cost explanations throughout the process, supporting rapid and optimal insurance coverage.
Keeping everyone on the same page was critical. Depcom’s proactive communication between the owner, the insurance providers, and partners wove the team together for an efficient collaboration.
A LOOK AHEAD
This is just the beginning. In next month’s conclusion to this piece, we’ll examine more case studies highlighting not only fire but also flood and storm damage. Plus, we lay out the case that, although no one can control the weather, what operators and facility managers can control is their level of preparedness.
Jamie Alexander is senior vice-president of services at Depcom Power, which serves the solar and energy storage market by providing traditional O&M services, restoration of sites impacted by natural disasters, repowering of sites underperforming or experiencing catastrophic failures, and specialized services focused on inverter commissioning and repair. Alexander’s twenty-five years of industry experience includes OEM equipment design and manufacture, project development, construction, and operations and maintenance. Having worked exclusively in the solar and energy storage sector for the past twelve years, Alexander has been involved in the deployment of almost 3 GWs of assets. For more information, visit www.depcompower.com.
MODERN PUMPING TODAY, July 2023
Did you enjoy this article?
Subscribe to the FREE Digital Edition of Modern Pumping Today Magazine!