By Ericka Richardson, Greene, Tweed
AccessESP, a Houston-based provider of rigless electrical submersible pump (ESP) conveyance solutions for the global oil industry, developed a retrieval technology that reduces costs by enabling quick and easy ESP installation and retrieval using slickline, wireline, or coiled tubing. The system eliminates the need for a workover rig to pull and reinstall an ESP, lowering intervention costs and minimizing lost production.
AccessESP’s unique solution is based on technologies with long-standing use in oilfields and other industries. The company’s key innovation has been to integrate these proven technologies into a radically simplified, rigless conveyance solution, differentiated by using a proprietary, high power density, high efficiency, permanent magnet motor.
THE CHALLENGE
AccessESP’s Reliability Management initiative demanded the development of a new advanced “power delivery” system to eliminate conventional ESP electrical connectors and cable performance weaknesses.
As the provider of the most effective solution in the market, AccessESP permanent magnet motors are capable of operating from low horsepower up to 1,300 horsepower, necessitating the engineering of a robust, customized, bulkhead connector system rated up to 8.6 kV phase-phase, and a continuous operating temperature of up to 400 degrees Fahrenheit (204 degrees Celsius).
Addressing AccessESP’s demanding voltage creep requirements, as well as their high-temperature and high-pressure requirements, meant forsaking a typical connector design that used metal load washers. As a conductive material, metal could introduce a pathway to voltage breakdown. To improve reliability, AccessESP required a thermoplastic load washer that could provide the mechanical support traditionally expected from a metal washer.
Given the customer’s highly specific material and technology needs and their desire for a global company with a local presence to foster a collaborative and responsive relationship, AccessESP contacted Greene, Tweed.
THE SOLUTION
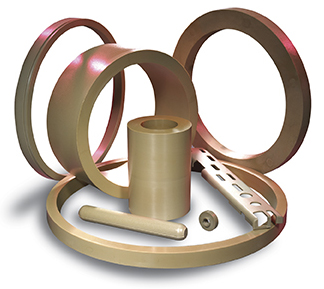
After reviewing the application requirements and understanding AccessESP’s concerns regarding voltage and creep distance, Greene, Tweed proposed a Seal-Connect® solution for the connector assembly, using a combination of its high-performance materials, including Arlon® 1000, Arlon® 3000 XT, and Chemraz® 629.
Arlon® 1000, Greene, Tweed’s non-filled PEEK material, a market leader for its combination of mechanical, thermal, chemical, and electrical properties, was chosen for the body of the electrical connector. Chemraz® 629, a perfluoroelastomer, was recommended for its high-temperature and electrical insulative properties for the seal between the bulkhead and contact block interface.
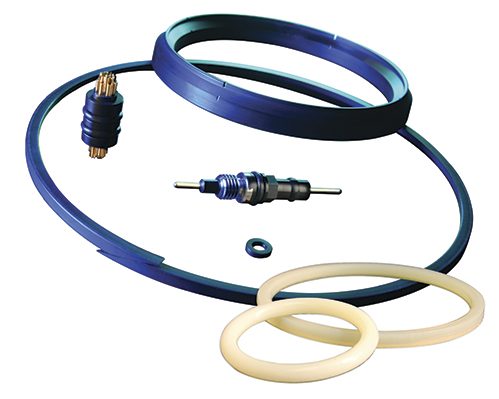
The company recommended Arlon® 3000 XT, Greene, Tweed’s exclusive, non-filled, cross-linked PEEK, as a solution to address AccessESP’s concerns regarding voltage creep and tracking distance. Arlon® 3000 XT, patented by Greene, Tweed, provides improved volume resistivity 30 times that of PEK at 400 degrees Fahrenheit (204 degrees Celsius) and dielectric strength, measured at 730 V/mil in an ASTM D149 testing.
In addition, Arlon® 3000 XT has 1.5 to 6 times higher mechanical properties compared to PEEK in tensile, compressive, flexural, and shear tests at a test range of 392 to 500 degrees Fahrenheit (200 to 260 degrees Celsius), which enabled the company to design a load washer offering the support typically provided by a metal element. Arlon® 3000 XT was also used for insulator sleeves on the bulkhead connector.
THE RESULTS
Arlon® 3000 XT’s best-in-class combination of electrical and mechanical properties provided AccessESP with a connector that demonstrated significantly improved performance over existing PEEK and PEK materials in an over-molded solution.
Greene, Tweed partnering with AccessESP engineering enabled us to share critical information that helped expedite the successful development of this innovative, next-generation product. Greene, Tweed’s Seal-Connect® solution passed all acceptance tests under IEC 60502-1 and API 11S6 standards for a 5-kV rated connector. Furthermore, the use of Arlon® 3000 XT lengthened the creepage distance between the pins, enabling the connector to pass the five-minute, 13-kV AC test at 300 degrees Fahrenheit (149 degrees Celsius).
“We continue to be pleased with Greene, Tweed’s proposed Seal-Connect® solution for the connector assembly,” says David Malone, AccessESP CEO. “This connector provided us with the required performance in order to guarantee a long and safe life with extremely high levels of reliability.”
This agile client/customer collaboration, along with Greene, Tweed’s proprietary materials portfolio and engineering and design expertise, provided AccessESP a customized connector solution that improved the performance of their innovative ESP system.
FOR MORE INFORMATION
For more than 150 years, Greene, Tweed has developed materials and engineered high-performance solutions that have enhanced the safety and performance of critical applications in the aerospace, energy, semiconductor, oil and gas, life sciences, defense, and other industries. For more information, visit www.gtweed.com.
MODERN PUMPING TODAY, August 2020
Did you enjoy this article?
Subscribe to the FREE Digital Edition of Modern Pumping Today Magazine!
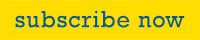