The skills shortage in engineering services is very real and is hitting hard in some sectors of the economy. In particular, the Engineering Construction Industry Training Board (ECITB) has highlighted a number of workforce challenges facing the water treatment and oil and gas sectors due to an aging workforce. For example, an estimated 19.5 percent of engineers currently working in the United Kingdom are expected to retire by 2026.
Ensuring that the industry’s future engineering needs are met is going to call for significant investment in skills among the next generation of engineers. While industry bodies like Engineering UK and others are calling for clear and properly funded STEM skills plans, many commercial organizations are boosting the skills of their own employees through innovative training programs.
ADDRESSING THE KILLS SHORTAGE
SPP Pumps is combatting the skills shortage challenges with its Future Cell initiative. This new training area is aimed at both apprentices and existing employees who want to reskill into an engineering role or simply take the opportunity to learn from experienced colleagues.
Designed, planned, and implemented by SPP’s Machine Shop team, Future Cell’s initial objective was to provide apprentices, as well as employees who wanted to retrain in engineering, an opportunity to extend their knowledge and skills through a series of challenges—working on real life pumping products and projects.
Investing hundreds of thousands of dollars in specific equipment and developing learning programs, the project was designed with a practical focus, ensuring that participants would gain hands-on experience and recognized qualifications through work-based operations in a fully equipped operational machining cell.
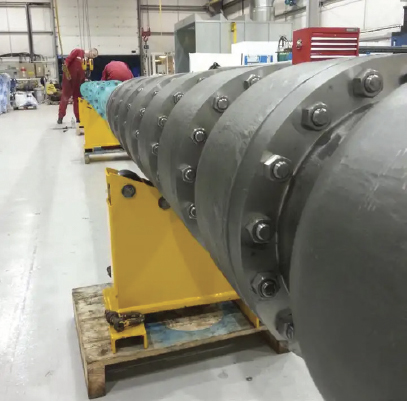
INVESTING IN THE FUTURE GENERATION
Because training is not limited to apprentices only, more experienced employees who want to retrain into engineering roles or expand their machining abilities are also able to benefit.
Two new CNC machines with remote monitoring and wireless probing help enable trainees to develop key programming and machining skills while producing critical pump components. Success of the initial three-month project proved the value of such an approach and secured further investment in equipment, with a state-of-the-art Electric Discharge Machining (EDM) tool recently been added to the program.
Also, with the purchase of three conventional machines, trainees are given the opportunity to become proficient in the underpinning knowledge essential to CNC machining and production engineering. In addition, a bespoke quality area in the machining cell gives apprentices the capability to inspect both their own and others’ work to both SPP’s and broader industry standards—essential for safe, high-quality operations.
Future Cell was launched late 2023, and within its first three months had exceeded its six-month productivity goal.
PEOPLE ARE AT FUTURE CELL’S HEART
A large part of the program’s success was ensuring that the project leader had personal experience of being an apprentice. Having joined SPP Pumps at sixteen as a mechanical engineering apprentice and benefiting from outstanding training to become a multi-skilled machinist, I was humbly selected to lead the Future Cell program.
In 2013, after successfully completing my apprenticeship, I took up a role within SPP Pumps’ machine shop; taking every opportunity to learn new skills, including additional responsibilities and further developing my leadership skills. It was only through this career opportunity that I realized the level of diligence and application needed to progress. Rather than going to my head when named as the Rising Star at the Pump Industry Awards (PIA) by the British Pump Manufacturers Association’s (BPMA), it increased my belief and determination that it was possible to train the next generation of engineers and promote opportunities that a company like SPP can offer young people.
As its name suggests, Future Cell has a clear objective to develop the next generation of skilled machinists. With the help of other experienced members of our team, we aim to offer a versatile training environment covering all key machining disciplines, while producing high quality components and reducing sub-contracting costs.
SPP invested in me at an early age and gave me the opportunity to learn invaluable skills. We’ve created a structured training plan that ensures all apprentices cover the essential skills. We identify individuals’ strengths and weaknesses and tailor their training accordingly, ensuring they gain the necessary knowledge and confidence to make technical decisions to help optimize the process’ capacity and productivity.
We are keen to raise the aspirations, employability and opportunities among local young people, as well as the wider community. Future Cell provides a golden opportunity for young men and women interested in engineering—and specifically the pumping sector.
REWARDING OUTCOMES
The machining team has been engendering excitement and interest in engineering to the local community through primary school visits, secondary school careers events, and scouting engagements. Together with STEM, the highly successful Future Cell initiative is the most recent investment in SPP’s wider project to address and hopefully head off the future skills shortage.
With provisions for all ages often featuring discussions around imagining a world without pumps, the team has sought to increase understanding that a career in the engineering, and more specifically the pumping industry is available and rewarding.
For more than 140 years SPP Pumps has been a leading manufacturer of centrifugal pumps and associated systems, a global principal in design, supply, and servicing of pumps, renowned fire pump packages, and high-quality equipment for a wide range of applications and industry sectors. SPP’s precision-engineered pumps and associated systems are installed around the globe, in all continents providing valuable high integrity services for diverse industries, such as oil and gas onshore and offshore applications, industrial water and wastewater treatment, power generation, construction, mines, and large industrial plants. For more information, visit www.spppumps.com.