People are programmed, whether consciously or subconsciously, to embrace the familiar. At the same time, when asked to complete a task, we are apt to identify the easiest way, or choose the path of least resistance, to get it done. When these two things—familiarity and ease—merge, a sense of complacency can be created, a feeling that “this is the best way and there’s no reason to consider any others.”
OPTIONS OVER CENTRIFUGAL PUMPS
Which brings us to the oil-and-gas industry. It is a complicated business, one that spans from the discovery of underground reserves to their recovery, gathering, refining, manufacturing, transport, storage, and eventual marketing as consumer goods ranging from motor fuels and asphalt to chemicals and cosmetics. Throughout the various point in this massive production and supply chain, pumps are required to move fluids and gases to and from numerous points.
For many years, the pumping technology of choice in many fluid-transfer applications in oil-and-gas production has been the centrifugal pump. To be fair, centrifugal pumps have performed admirably in these situations. Their method of operation—fluid enters the pump impeller along or near to the rotating axis and is accelerated by the impeller, flowing radially outward into the volute discharge port—makes them well designed for the high-volume, severe-duty transfer applications that are common in the industry. Centrifugal pumps also work especially well with thin, water-like fluids that must be transported through networks of piping with variable flow rates.
So, it’s easy to see why centrifugal pumps have gained a reputation as a go-to technology in oil-and-gas fluid-handling applications. Still, there is an understandable sense of “if it ain’t broke, don’t fix it” thinking when it comes to considering alternatives to centrifugal pumps by operators in the industry. This article, however, will illustrate how a different technology—positive displacement twin- and triple-screw pumps—can oftentimes be a more versatile, reliable, and efficient choice than centrifugal pumps in critical fluid-handling operations in the wide-ranging oil-and-gas industry.
THE CHALLENGE
The most obvious challenge—and perhaps the toughest to overcome—in making the screw pump more prevalent in oil-and-gas applications is convincing the industry’s operators to move away from a technology that has become ingrained in their minds as the best one for numerous jobs. Generally speaking, the bulk of the fluids that are handled during oil-and-gas production in North America have very low viscosities and must be transferred at very high flow rates, which plays to the operational strength of centrifugal pumps.
Because centrifugal pumps have been successful in North America, other oil-producing regions of the world, especially the Middle East, have taken great pains to replicate the North American production infrastructure, which includes significant use of centrifugal pumps. In many cases, oil-and-gas production and processing systems have been designed around the pumping technology, rather than the other way around. This means that engineers are first familiar with centrifugal pumps and attempt to work within their operational limits. They know how centrifugal pumps operate, know their benefits, and are confident that they are the best technology for what they are trying to accomplish.
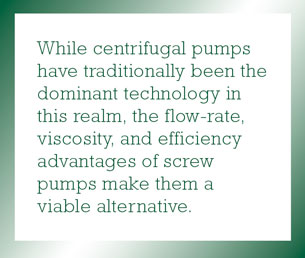
To illustrate this mindset, in some cases a design engineer—instead of considering an alternative pumping technology—will blend or heat raw crude oil as a way to manipulate the process and get the viscosity of the fluid down to less than 300 cSt, which makes it easier for the centrifugal pump to transfer the fluid. What they are doing in this instance is reconditioning the fluid to fit the pumping technology – irrespective of the cost impact.
In other words, when measures like this are taken to satisfy the needs of the pump, the popularity of centrifugal pumps in oil-and-gas fluid-transfer applications becomes something of a self-fulfilling prophecy.
ACHIEVING BEST EFFICIENCY POINT
Despite the ability to recondition the fluid to meet the operational needs of the centrifugal pump, operators must still take care to ensure that the centrifugal pump is operating on what is known as its “Best Efficiency Point,” or BEP. The BEP is the point where the centrifugal pump is working at its highest level of efficiency. Centrifugal pumps rarely operate at their exact BEP because pristine pumping conditions are rarely realized, but a centrifugal pump that is able to function in a window between 80 and 110 percent of its BEP is said to be functioning adequately.
However, when the operation of the pump moves too far off its BEP uneven pressure will be applied to the impeller, which can result in increased radial thrust that will cause the pump’s shaft to “deflect.” When this deflection occurs, higher loads will be placed on the bearings and mechanical seal, which can lead to damage to the pump’s casing, back plate, and impeller. Ensuring operation at the BEP can be a time-intensive task as the pump must be monitored constantly and adjusted, which costs time and money.
Additionally, meeting production rates and quotas has always been job No. 1 in oil-and-gas operations, but as operating costs have continued to rise, there has been a call for increased operational efficiency in terms of the amount of energy that is required and consumed during pumping operations. In this area, centrifugal pumps can also fall short:
- Due to pump-selection complexity, over-sized pumps are often chosen, resulting in increased operating and maintenance costs, inefficient operation, and higher-than-necessary energy consumption.
- As pump differential pressure increases, the flow rate decreases. Therefore, time-sensitive operations that are dependent upon maintaining a constant flow rate will take longer, which may be costly.
- The performance of a centrifugal pump will be adversely affected when pumping a fluid that has a viscosity greater than 100 cSt.
These inefficiencies will lead to higher utility bills and have an undoubted effect on the operation’s bottom line.
A LOOK AHEAD
As mentioned, the solution to the shortcomings of centrifugal pumps can be positive displacement (PD) screw pumps. The problem is not only overcoming the built-in advantages of the centrifugal pump’s vast installed base, but getting design engineers to acknowledge or even become aware that there are alternatives like screw pumps. In next month’s conclusion, we will take a closer look at two of Blackmer’s S Series pump models recommended for these applications.
About the Author
Josh Pepper is the global product manager—screw pumps for Blackmer®, Grand Rapids, MI, USA, and can be reached at 616.248.9235 or josh.pepper@psgdover.com. Michael Moore is Blackmer’s senior director, business development—screw pumps and can be reached at 519.802.2106 or michael.moore@psgdover.com. For more information on Blackmer’s full line of pumps and compressors, visit www.blackmer.com or call 616.241.1611. Blackmer is a product brand of PSG®, a Dover company, Oakbrook Terrace, Illinois. PSG is comprised of several of the world’s leading pump brands, including Abaque®, Almatec®, Blackmer®, Ebsray®, Finder, EnviroGear®, Griswold™, Mouvex®, Neptune™, Quattroflow™, RedScrew™, and Wilden®. For more information, visit www.psgdover.com.
____________________________________________
MODERN PUMPING TODAY, November 2017
Did you enjoy this article?
Subscribe to the FREE Digital Edition of Modern Pumping Today Magazine!
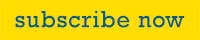