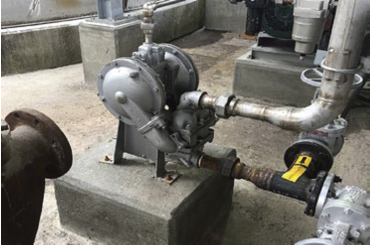
Reliable air-operated double-diaphragm (AODD) pumps make every pulp processing plant safer. When functioning properly, they safely dispose of hazardous wastewater generated during the papermaking process. Recently, a major pulp and paper producer that operates nearly thirty facilities around the country needed an AODD pump for one of its kraft mills that makes paper products for U.S. and international markets.
THE CHALLENGE
The paper producer needed a sump pump to dispose of rainwater in a containment area at one of its plants. But rainwater wasn’t all that needed to be disposed of by the pump. Black liquor soap—a byproduct extracted during the conversion of wood into wood pulp—also entered the containment area. Therefore, the sump pump needed to be able to pump rainwater as well as this hazardous byproduct.
There are many pump options available for sump and rainwater applications, but this particular application was more demanding than normal. Black liquor soap, or tall oil soap, is extracted from black liquor before the liquor is processed for reuse or used to create power. For the black liquor processing to continue at the highest efficiency and at reduced maintenance downtime, the soap needed to be removed.
The soap is essentially a fatty acid that foams and retains air when agitated and creates slippery and hazardous work surfaces when released. The soap is removed from the black liquor by skimming it off the tops of vessels and pumping it away using positive displacement pumps. During upset conditions, the soap can actively dump into the collection area and a pump would have 100 percent black liquor soap in the sump. The pump used to evacuate this sump area would see pumpage with entrained air, suspended solids, large swings in viscosity and unique control challenges, which would quickly fail some pump technologies.
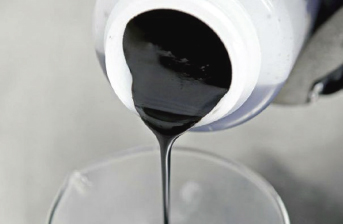
THE SOLUTION
To contain the hazardous black liquor soap and black liquor, the company created a containment area with a sump that could be pumped out to a safe area for processing. The challenge was finding a pump that could handle the liquid, the varying operating conditions and would not leak. They originally installed another style of pump that leaked excessively. Needing to find a versatile and trustworthy solution for its containment area, the company turned to a pump manufacturer known for making durable and dependable products for the harshest applications: Sandpiper.
After assessing the situation, Sandpiper experts recommended installing a 2-inch heavy-duty ball (HDB) valve pump to remove both rainwater and black liquor soap from the plant.
The Sandpiper HDB down-ported pump was the perfect fit for this black liquor soap application. Here’s why:
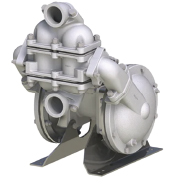
- It’s self-priming and can completely pump out the sump.
- It can be controlled easily by one float connected to one discharge valve. When the discharge valve is closed, the pump simply stops and restarts when the valve is reopened.
- The AODD design has no mechanical seals like a rotating positive displacement or centrifugal pump. Mechanical seals have a tendency to fail in this application and will leak, causing more issues.
- It can run dry without damage. This is a plus when emptying sumps that can have varying liquid levels causing dry running.
- It can pump liquids entrained with air or other gases, such as the foamy black liquor soap.
- The Sandpiper HDB model with a bottom-port configuration is excellent at pumping solids-laden fluids by leveraging gravity to keep the pumping chambers free of blockage.
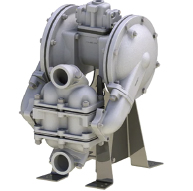
The pump was chosen because its AODD design could easily handle everything from water to highly viscous and abrasive fluids. The unique down-ported design uses gravity to evacuate the abrasive slurry from the diaphragm chambers, eliminating solids buildup. The pump also has weighted check balls to allow the balls to seat properly when pumping high viscosity fluids. The self-priming AODD pump can handle the air-entrained product without interruption or damage to the pump, and its seal-less design prevents leaks. To automatically turn the pump on or off for unattended service, plant management installed a Sandpiper Liquid Level Control.
THE RESULT
As a result of its partnership with Sandpiper, the company was able to find a reliable solution to a challenging pumping application faced by pulp and paper producers and avoid a potential emergency. If you’re in charge of keeping plant employees safe and maintaining systems and machinery, it’s important to partner with manufacturers you can trust. Sandpiper’s wide range of products and deep pumping expertise can deliver the solution clients need for the most complex industrial problems. With Sandpiper’s quick lead times and an after-sale support team that will ensure the equipment is running as efficiently as possible, this client received the reliability, durability, and value they deserved.
FOR MORE INFORMATION
Edward Kupp is director of product management for Warren Rupp. Warren Rupp pumps are offered worldwide through independent authorized distributors in at least seventy-five countries, including Sandpiper. With over fifty-five years of trusted solutions expertise, Sandpiper delivers best-in-class pumping and engineering innovations for customers’ most difficult and demanding pumping challenges. For more information, visit www.sandpiperpump.com.
MODERN PUMPING TODAY, October 2023
Did you enjoy this article?
Subscribe to the FREE Digital Edition of Modern Pumping Today Magazine!