We live in an age of energy optimization. It seems the world has finally rallied around the idea that addressing wasted energy in pumping applications represents a huge financial gain to owners and a substantial efficiency gain to energy providers.
All you have to do is ask a motor manufacturer and I am sure you will get an impassioned response related to governmental energy standards. In just the past several years, we have gone from EPACT to EISA Motor Efficiency Standards and it now appears that this is going to be “refined” yet again.
It’s great that these regulations have continued to push the envelope on motor efficiency, but they never seem to consider the application. Motors do the work applied to them, but the intelligence is in the control. It is the sum of the parts acting as a system that contributes to the overall savings and energy efficiency of a piece of equipment, not just the motors.
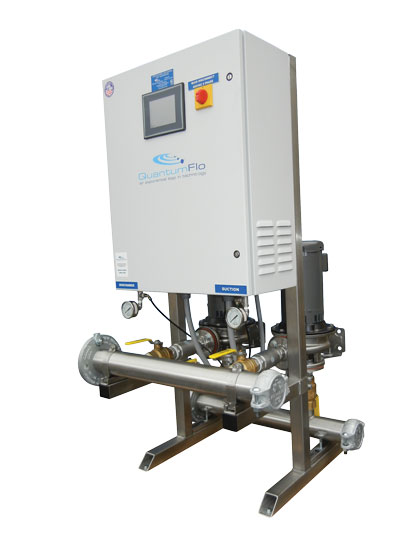
THE LAWS THAT DRIVE ENERGY OPTIMIZATION
Our company builds many pressure booster pump stations that regulate constant output pressure control. Output pressure is our process variable (PV), the primary element we use to maintain a constant feedback loop to maintain pressure regardless of the flow through the pump. We have chosen to do this using electronic rather than hydraulic control. Incredibly, electronic (variable speed) pressure control has only become the preferred means of control within the past ten to twelve years. Prior to this, hydraulic control (pressure regulating valves) was the chief control standard.
As you look around at the current industry, you will likely notice the proliferation of variable speed motor control from large process applications to small fractional horsepower circulators. It makes sense to vary pump speed when you are trying to control a multitude of potential process variables from flow to temperature, to differential pressure and discharge pressure.
So why has variable speed control become so ubiquitous? The simple answer to this lies in the pump and fan affinity laws.
These physical laws state the following:
- A pump or fan increases or decreases flow in proportion to the speed of the motor.
- A pump or fan increases or decreases in pressure as the square of the speed change.
- A pump or fan increases or decreases in energy as the cube of the change in speed.
It is easy to see that, based on these three laws, pumps and fans can have the greatest potential differential of energy based on a change in the motor speed. The best part of this is, only a small change in speed yields a fortune in energy reduction due to the cubic relationship to pump speed. If you perform this basic math, a 20 percent motor speed reduction (.80 x .80 x .80 = .512 or 51.2 percent total energy) nearly cuts your power in half.
Adding the VFD to this application saves far more energy than simply specifying an EISA compliant motor. This requires the engineer to apply the proper components to get to the next level of energy efficiency made possible by the affinity laws.
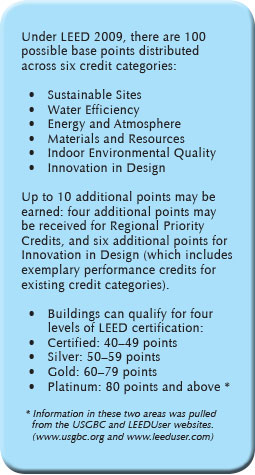
THE IMPACT OF LEED CERTIFICATION
We apply many of our products to the world of commercial building trades. Since the advent of sustainable design, many standards have adopted these green efforts. One effort to improve sustainable design and provide resources to these efforts is the U.S. Green Building Council (USGBC). USGBC has established a roadmap toward sustainable design known as Leadership in Energy and Environmental Design (LEED).
LEED goes beyond the general standards that apply to specific trades within the building such as structural, HVAC, civil, etc. and is an attempt at looking at the total environmental impact of the building. The USGBC committee evaluates the total impact of the structure, including its carbon footprint, or greenhouse gas emissions. When LEED accreditations are followed, existing building emissions can be offset by following the rules of sustainable design such as a “green roof,” which would provide plant life to offset CO2.
The overarching goal of these new efforts is simple: save energy. Since most energy is saved by speed reduction, as in the affinity laws, the primary purpose of these standards is to search for every opportunity to save energy, and thereby, the environmental impact of that energy consumption.
Consider the case of LEED credit for new Construction and Energy Optimization (NC-2009 EAc1). This LEED credit deals with optimization of energy loads within a building. Since the booster system is one of many VFD pump and fan loads within the structure, you can see how substantial an impact this could represent. In fact, EAc1 is by far, the most important credit within the LEED accreditation system as it relates to total points available. This area alone represents up to 19 total points, comprising nearly half of your minimum qualification. You cannot shoot for LEED Platinum without considering the requirements of EAc1.
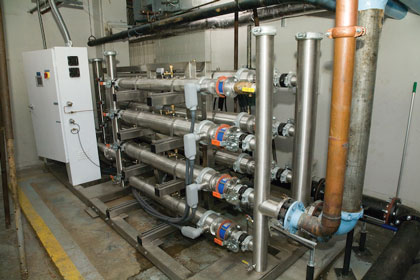
THE ADOPTION OF ANSI/ASHRAE/IES STANDARD 90.1
ANSI/ASHRAE/IES Standard 90.1 is the world’s most adopted building energy code, and yet many plumbing consultants do not realize that it affects booster pumps systems in a major way. Constant speed pumps have been some of the greatest energy vampires in the commercial building space, sucking energy from the source to do nothing more than charge a water riser so someone can walk up to a toilet and flush it.
In the past, this flushing sound signified the owners’ cash being sucked from his wallet, as a pump that does not change in speed uses 100 percent of its full power all the time to make certain that water is available at each fixture. From an energy perspective, the booster was the low hanging fruit of the energy optimization movement, but 90.1 did not stop at just the standard operational savings. The committee wanted more.
The Standard also requires the consultant to either move the variable speed pressure control sensor to the farthest point in the building, or employ software logic to simulate the operation of this remote control. What this does is dial-out the piping friction between the booster and the farthest point in the system. By eliminating piping friction from the control, the pump is allowed to slow even more when the flow rate doesn’t always require this additional friction loss. This is a concept that comes from the HVAC industry, as most of the pressure required by a closed loop HVAC system is due to piping friction loss. However, the friction contribution of an open-loop plumbing system is not as substantial. Nevertheless, Standard 90.1 wants this energy back.
VIRTUAL SIGNALING
There is a secondary option in lieu of the remote set point whereby the system could be controlled via virtual signaling—or logic in the programming that simulates the effect of a remote sensor. This is probably the simpler way to accomplish the reduction in speed without having to involve another contractor besides the plumber; namely an electrician to run the signal wires.
As a result, pump system companies have recommended the use of virtual signaling in lieu of the extra labor and contractor disciplines. (For our company, QuantumFlo, this algorithm is called GreenFlo™). This process measures the flow across the pump and changes the set point when the flow rate is low and the additional pressure is no longer required. The setting then resets when flow is increased back to the range requiring the extra boost. The best part of using logic control versus physically moving the sensor is that the system can maintain its factory-tested and pre-engineered status, which is the primary reason the consultant specified this pre-engineered device in the first place.
INCREASED OPPORTUNITY FOR BOOSTER SYSTEMS
Standard 90.1 (as written) was adopted in October of 2011 and provided a two-year window for states to comply, so most U.S. consultants are already required to design to it. However, many plumbing and mechanical engineers do not even realize that the section regarding the use of VFD-based plumbing pumps even exists. It was then adopted by the International Energy Conservation Code (IECC) in 2012 making it the most prominently implemented.
It does not seem typical to consider that a booster system pressure would actually change according to the flow conditions, but as technology advances, so does the opportunity to use it for the betterment of our world. ANSI/ASHRAE/IES Standard 90.1 is being used in these new designs to assist the engineer in this endeavor and the manufacturer is also there to answer the call to continually innovate and implement these useful energy optimizers.
It is imperative that the engineering community continue to learn and engage with the community of technology and manufacturing in order to find these energy optimizers which, when taken in total, can contribute greatly to the energy consumption footprint of these buildings.
About the Author
Dave Carrier is president and CEO of QuantumFlo, Inc. With nearly 100 years combined industry experience, QuantumFlo has promoted and expanded the new packaged system technologies to the pump systems market. For more information, visit www.quantumflo.com.
MODERN PUMPING TODAY, December 2014
Did you enjoy this article?
Subscribe to the FREE Digital Edition of Modern Pumping Today Magazine!
