In many applications in the oil and gas industry, the chemical industry, or even the food industry, pumps that work reliably and provide high performance are needed. At the same time, they must have convincingly low investment costs. With the Ecosmart diaphragm metering pump, the German Lewa GmbH has provided a cost-attractive and safe model that can handle flow rates of up to 300 l/h for many years. For use in applications with higher flow rates, the pump expert from Leonberg, Germany, is now expanding its product range with two new sizes. In addition to the LCA version, the Ecosmart will also be available in the more powerful LCC and LCD versions in the future. While the LCC model can meter in excess of 264 gallons per hour, Lewa designed the LCD for a flow rate of up to 528 gallons per hour. The maximum permissible operating pressure for both models is 50 bar and 600 pounds respectively. The stringent use of similar components within the Ecosmart product family keeps production costs and therefore the final price low. At the same time, a high level of safety can be guaranteed by focusing on all essential design features such as the pressure relief valve or the proven sandwich diaphragm with continuous monitoring. The LCC variant was made available at the end of 2021 and the LCD model will be available by mid-2022.
In addition to the proven diaphragm metering pumps of the Ecoflow series, Lewa has offered the less expensive Ecosmart pump for several years. This is mainly due to the fact that although a reliable pump unit is required in numerous processes, at the same time relatively low discharge pressures in the lower two-digit range require less complex pump technology. With the Ecosmart LCA in the single pump version, however, only a flow rate of below 80 gallons per hour was previously possible. In order to be able to offer the Ecosmart for applications with higher flow rates, the engineers at Lewa began developing two additional, larger pump variants in 2019. The aim was to scale up the Ecosmart to larger applications with the proven safety level and high quality Lewa components without significantly increasing the low investment cost typical for this pump series. This was to be achieved by a consistent modular principle within the pump series, as well as a strict focus on the essential functions and features. The specifications also demanded the usual Lewa suitability for unrestricted continuous operation over many years. Options for integrating the pumps into automated systems via analog control signals or bus systems are also a matter of course.
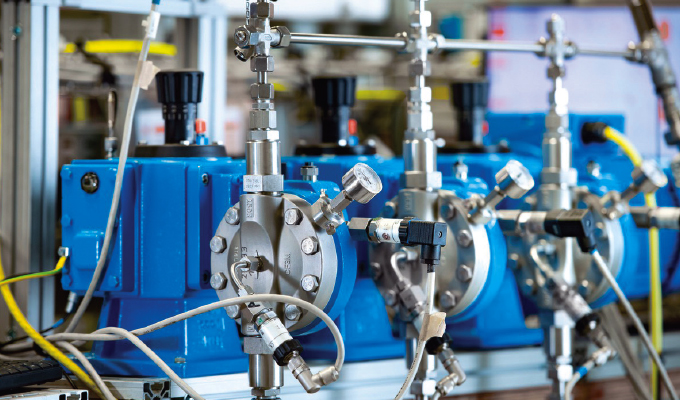
ADJUSTMENT OF PLUNGER DIAMETER AND STROKE ENABLE MORE FLOW
First of all, the requirements for the conveying capacity had to be implemented constructively. Larger plunger diameters were selected for the smaller LCC variant, so that more than 264 gallons per hour can be conveyed instead of less than 80 gallons. In the case of the more powerful LCD version, the engineers also decided to extend the stroke length so that a maximum flow rate of 528 gallons per hour could be achieved. Both pump types can work against a maximum operating pressure of 50 bar. As with all hydraulically actuated diaphragm metering pumps, maximum pressures are achieved with smaller plunger diameters.
Just as important as the performance of the pump was the operational reliability typical of Lewa familiar from other pump series. For this purpose, individual, essential features such as the integrated pressure safety valve or the sandwich diaphragm were taken over from the Ecoflow models. The individually adjustable pressure safety valve ensures that sudden overpressure in the pump does not damage the diaphragm or pump drive. The diaphragm protection system DPS, whose essential component is a return spring for the diaphragm, also ensures that the PTFE sandwich diaphragm always works in the right place. It cannot be overstretched or damaged during start-up. Thus, the pump is protected against operating errors or upset operating conditions. Finally, the standard diaphragm monitoring system checks the condition of the diaphragm and warns plant operators immediately if there is any damage. This reliably prevents cross-contamination between the pump and the piping system and ensures operational safety at all times, especially in sensitive areas with toxic fluids. However, diaphragm monitoring is rarely used because Lewa diaphragms of this series usually achieve service lives of several years – even under full load and continuous operation.
A key point was to keep production costs within a similar range to the small LCA variant, thereby creating attractive market prices for applications with less demanding requirements and lower operating pressure. To do so, the design of the two new pump sizes needed to integrate components that are as identical or at least similar as possible in order to avoid high manufacturing costs. In this way, the Lewa engineers were able to successfully implement the common parts strategy that had already been practiced many times.
Pump users also benefit from this intelligent modular principle, as many wear parts can be used across pump types. This considerably simplifies the spare parts inventory. At the same time, the modular principle also allows individual adjustments to the respective application. For example, stroke frequencies or plunger diameters can be selected individually. The basis for this is the M900 pump head, which is already used in the LCA variant and in the Ecoflow program.
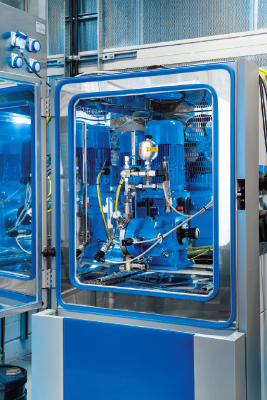
GOOD INTEGRABILITY FOR PLANT CONSTRUCTION COMPANIES
The pump’s flexibility also offers advantages for plant construction: It allows the Ecosmart pump to be oriented either vertically or horizontally, making it easier to integrate the unit into systems with limited or confined spaces. In addition, the pump head of the new LCC and LCD models is aligned at right angles to the plunger axis, resulting in a particularly compact format. In many pumps, the pump head is on the same axis as the plunger, which often results in bulky pump dimensions. The 90-degree orientation avoids this with the new models. This advantage is achieved by the extremely compact and completely newly developed, cost-effective diaphragm drive.
In order to ensure the long service life typical of Lewa pumps, only high-quality, robust materials are used in the LCC and LCD versions. Toxic and abrasive substances can stress the pump significantly and so a variety of materials can be used on the wet end, which are also successfully used in the high-pressure variants of the Ecoflow series. Many high-quality parts from the Ecoflow series are also used for the drive units, employing the common parts strategy. The result is robustness and durability that is unusual in this pump class. In addition, all Ecosmart pumps have been designed with a single oil bath, which is used for both the lubrication of the drive unit and the hydraulics of the pump head. This eliminates the more complex lubrication via two separate oil systems and results in a simpler design, which not only facilitates operation but also reduces maintenance work.
Last but not least, the new LCC and LCD versions—like the LCA—comply with the U.S. industry standard for metering pumps API 675, ensuring nearly unlimited usage for numerous demanding processes in a wide range of industries.
USE IN THE CHEMICAL INDUSTRY
For example, when metering solvents in the chemical industry, pumps are needed that on the one hand meet the highest specification requirements and on the other hand are still cost-effective. Here, the Ecosmart pump with its higher performance is able to meet exactly these requirements, as it has been precisely engineered for applications in the lower pressure range up to 50 bar (600 pounds). The larger versions of the Ecosmart pump are also suitable for industrial water treatment, such as in seawater desalination or industrial cooling circuits. What counts here above all is compactness and cost-effective design, which the entire Lewa Ecosmart series fulfills thanks to its innovative design principle.
Before the new pump variants are available to customers, a number of extensive tests will be carried out. They will ensure that the units also meet the high internal company requirements for reliability and performance in operational practice. They include, on the one hand, continuous load tests of up to several tens of thousands of hours and, on the other hand, overload tests. In the latter, the pump is run continuously at up to 20 percent above maximum pressure to further validate its robustness. Special tests are carried out in heated cabinets to proof that the pumps also perform perfectly under extreme ambient conditions. After successful completion of all tests and final adjustments, the Ecosmart version LCC is now on the market, the LCD model will follow in mid-2022.
FOR MORE INFORMATION
Thomas Bökenbrink is lead product manager for pumps for Lewa GmbH. Lewa develops technologies and provides solutions for the vast array of applications among its customers. Its products are used mainly in the oil and gas industry, in gas odorization, in refineries and petrochemicals, as well as in the production of plastics, detergents, and cleaners. Additional application areas include the chemical industry, cosmetics industry, pharmaceuticals and biotechnology, food and beverage industry, and energy utilities. For more information, visit www.lewa.com/en/pumps/metering-pumps/lewa-ecosmart-diaphragm-metering-pump.
MODERN PUMPING TODAY, May 2022
Did you enjoy this article?
Subscribe to the FREE Digital Edition of Modern Pumping Today Magazine!