The growing trend towards above ground pump stations is transforming wastewater collection systems, empowering operators to rise above the challenges of conventional submersible pumps. It’s common sense that relocating pumps above ground, away from constant exposure to corrosive and hazardous sewage, safeguards the mechanical and electrical components of the pumps, as well as the workers who handle them. This strategic move simplifies maintenance by making the equipment more accessible and eliminates the need for workers to enter dangerous, confined spaces, thus improving safety.
Additionally, it reduces wear and tear on equipment and minimizes breakdowns. By dramatically improving reliability, pump efficiency and longevity, the increasing adoption of above ground systems aligns with sustainability goals by eliminating the costly problems of frequent stocking, replacement and disposal of submersible pumps.
The longevity of above ground pump stations is evident in their decades-long lifespan, markedly outperforming the brief lifespan of a few years typical of submersible pumps. The longer service life and easier maintenance add up to a significantly lower total cost of ownership.
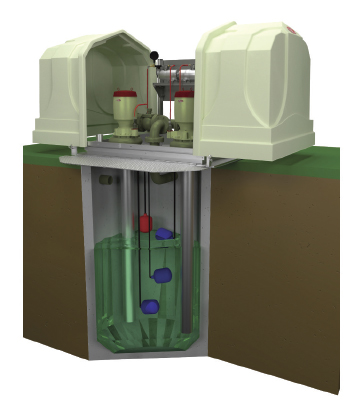
RELIABILITY, ENERGY EFFICIENCY, AND OPERATOR SAFETY
Let’s explore the vital role of pump stations and their key requirements. Wastewater pump stations are crucial in residential, commercial, and industrial settings for effective wastewater management and to prevent sewage backups and overflows. Throughout the United States, countless pump stations perform an essential role: they pump wastewater from lower to higher elevations in situations where gravity flow is impractical.
Pump station facilities comprise a receiving well (wet-well) that is equipped with pumps, pipes, valves, power supply, and control systems and may include a screen or other specialized components designed to mitigate against heavy clogging materials along with systems for odor control and ventilation. Typically, pump stations employ at least two pumps for redundancy, alternating between the lead and lag roles to ensure both efficiency and reliability.
Reliability
The reliability of wastewater lift stations is vital for public health and environmental protection. A failure can result in sewage backups, untreated wastewater overflow, and severe flooding, leading to odor issues, health risks, environmental harm, and property damage. Considering the potentially severe consequences that can arise from pump station failures, it is imperative that these systems be designed with a focus on robustness to guarantee their long-term reliability and efficiency. Pump stations must also be designed for easy access, facilitating regular inspection and maintenance to prevent failures and performance degradation and to prolong system life.
Energy Efficiency
Maintaining operational efficiency is crucial because pump stations consume a significant amount of electricity. Ensuring they continually operate at peak performance is therefore not only an environmental necessity but also a financial one.
Prior to installation, optimizing pump performance begins with pump selection based on the pump station’s flow and head conditions. Pump manufacturers publish pump curves demonstrating the range of pump efficiencies that a particular pump model will achieve, assuming proper care. Selecting a pump that optimizes the pump’s efficiency—and ultimately the pump station’s wire-to-water efficiency—translates into lower power consumption and lower utility costs.
Of course, it follows that pumps with more robust internal construction generally feature higher pumping efficiencies. Yet, dry-pit solids-handling wastewater pumps tend to be more efficient than typical wet-pit or submersible pumps. The latter’s design must account for full submergence in the sewage to prevent seepage into the motor, which can lead to pump failure. As a result, submersibles tend to be less efficient compared to dry-pit pumps.
Operator Safety
Ensuring the reliability and performance of pump station operations necessitates regular maintenance, underscoring the critical need for pump operators to conduct these tasks in a safe and efficient manner. Conventional submersible lift station designs present significant safety hazards, complicating maintenance procedures.
Confined Spaces
Lift stations that require access to the wet wells and any associated valve vaults will often be classified as confined spaces by municipal utilities and industrial end-users per OSHA guidelines. These sub-surface spaces pose significant safety challenges because operators must enter these spaces to perform routine maintenance or emergency repairs. Operators are exposed to risks like toxic gasses and contact with sewage. Ensuring safety requires strict and costly protocols such as permitting, multiple personnel, proper ventilation, gas monitoring, harnesses, and protective gear, along with thorough training for adherence to OSHA standards and other Class 1 Div. 1 requirements.
Hazardous Materials
Exposure to raw sewage, commonly referred to as “black water,” is hazardous. This term encompasses any waste contaminated with human feces and other liquid waste, including discharges from urinals and toilets. Additionally, sewage presents chemical dangers, including the presence of ammonium compounds, formaldehyde, chlorine-based products, sodium hydroxide, and enzymes used in odor control and sewage decomposition. It also contains sanitizers, biocides, agents for cleaning or bleaching, pharmaceuticals, hormones, and heavy metals. The pandemic has heightened awareness of the risks that operators face, especially the increased risk of waterborne diseases.
Enhancing job safety and reducing unpleasant aspects are crucial for minimizing accidents and health risks, as well as boosting worker morale and satisfaction. This is becoming increasingly vital in the wastewater sector as it seeks to recruit and retain its workforce. With a significant number of employees nearing retirement—statistics indicate that up to 30 percent of the current wastewater operations workforce in some areas may retire within the next five to ten years—addressing these issues is essential for ensuring a skilled and motivated workforce.
A LOOK AHEAD
In the conclusion to this series, we’ll take a closer look at the history of above ground systems as well as explore the technical reasons these advancements in lift station design have led to a track record of more economical costs, safer performance, and efficient operations for a variety of applications.
As a pioneer of pumping systems for seventy-five years, Smith & Loveless has spearheaded the innovation for above ground pump systems, with continuing advancements in the design and production of these stations. Designed with a focus on robustness and a keen awareness of the most pressing industry challenges, above ground lift stations protect both operators and employers, and offer lifespans that are significantly longer than submersible pumps. It is, therefore, no surprise that operators facing workforce challenges, flushables, and economic pressures are increasingly turning to above ground pump stations over conventional submersible pumps to meet current and future demands. For more information, visit www.smithandloveless.com.