Imagine if you will, wear components that do not rely on low coefficient of friction or lubrication to extend the components’ life, but by reducing the contact area between the rotating and non-rotating surfaces. Basically, you reduce the contact area between the wear component by the diameter minus the apex of the curve. Assume millions of tiny spheres and, thus, the contact area of the part is reduced by the diameter minus the apex of the curve of two round smooth surfaces.
This design is accomplished by using a high temperature / low coefficient of expansion resin that has impressive adhesion to fillers. This allows the resin to be filled with micro spheres that only contact the tip of the round shaft at the apex of two curves. This adhesion to filler is the key to the function of the wear-resistant parts. The parts adhere to the filler so that the tiny spheres do not dislodge. We have now had wear parts in the field for fifteen years without failure or wear on the shaft.
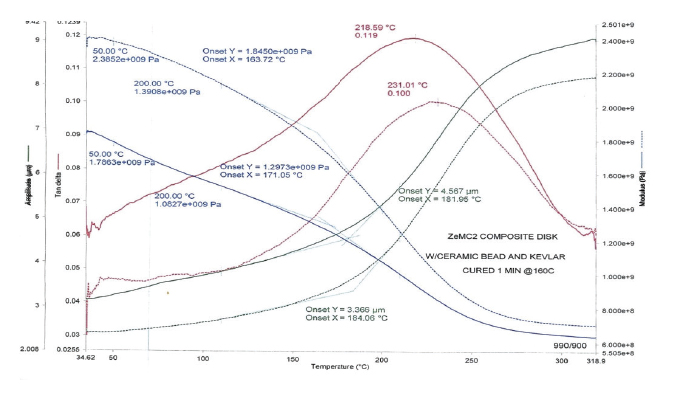
HIGH TEMPERATURE PERFORMANCE
Let’s look at the following example: glass transition temperature (Tg) increases with post baking. Please note in the DMA seen in this graph, the first pass to 572 degrees Fahrenheit (300 degrees Celsius) has a Tg as a of 424 degrees Fahrenheit (218 degrees Celsius), the second has a Tg of 447 degrees Fahrenheit (231 degrees Celsius), and the third has no definable Tg and the temperature capacity extends beyond the limits of the DMA.
ADHESION
Myriad materials have been tried and all save this one released the spheres. Loose ceramic spheres in a pump have been the result of all others. Aaron Rutin, CEO of R3 Composites, had this to say in a report from our first try with our wear components: “Carver Pump has been working with a potential new customer who is an OEM to sell them high-pressure pumps (Carver Ring Section RS pump) for inclusion in their product. Each ring section in one of these pumps contains multiple wear rings and bushings made of PRLC components molded and machined by R3 Composites.”
Rutin continues, “Carver Pump supplied one typical pump to this customer for their evaluation before placing orders. They ran this test pump through performance, endurance and accelerated usage test and returned it to Carver pump for inspection. The customer reported the pump ran beautifully no matter what they through at it. On inspection, it appears they ran everything but the kitchen sink through the pump without problems or loss of performance. Metal parts and hose fittings were found lodged inside the pump along with other discarded floor debris. All of the rings and bushings appear to be in good shape with minimal dimensional change except for scars on the working surfaces where the foreign materials worked their way through the tight clearances on the pump during operation.”
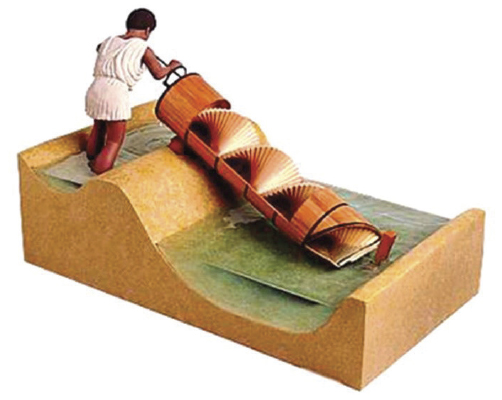
HISTORY
Archimedes invented the first centrifugal pump about 200 BC in Ancient Greece. Since then, pumps, centrifugal and otherwise, have had the same continuous problem—wear. One part must turn while the other remains stationary. Centrifugal pumps have changed little since then—an impeller turns and liquid is pumped in the desired direction. The first wear bushing was probably soft wood to protect the hard wood. Therefore, wear equals downtime to change the soft wood.
New materials, sophisticated impeller angles, and propulsion are the only differences in 2,200 years. Wear between the stationary and rotating components is still the main cause of downtime. It has always occurred at the interface between moving and stationary surfaces and has been an accepted, unavoidable drawback.
The industry practice for pump manufacturers is to design a cheap sacrificial bushing, just like the soft wood of the very first pumps, to abrade away and spare the more expensive shaft. To replace the shaft or the bushings requires downtime, which is the most expensive factor. Pump users need multiple pumps so that one can be taken offline for rebuild of the wear components while another is serviced. Increasing uptime is an advantage of parts molded from the new bulk molding compound.
THERMOSET RESIN
A proprietary thermoset resin is the key to the functionality of this new product because of its high glass transition temperature (Tg), chemical resistance, and unsurpassed adhesion to fillers. Excursion temperatures to 572 degrees Fahrenheit (300 degrees Celsius) are not uncommon. In one application, a pump was returned from the field for rebuild with the epoxy paint on the outside of the housing scorched from friction heat generated internally by abuse. The rebuild manufacturer reported that the new BMC wear bushing and the shaft under the wear bushing looked like new.
The ability of this resin to adhere to fillers is the reason Kevlar and ceramic beads can be used to hold them in place for machining. The fiber reinforcement is similar to rebar in concrete—without it there is little strength. Nothing adheres to Kevlar, according to the manufacturer, but adhesion to Kevlar was achieved with this resin that was equal to epoxy resin to glass. This is why parts manufactured from this composite are the first long-fiber, Kevlar-filled parts that can be machined cleanly and hold tolerance.
Kevlar also makes it free from the possibility of galvanic corrosion. Dimensional creep with temperature is another reason that other resins do not adhere to their fillers. Adhesion and exceptionally-low creep are the reason this resin is vital to the product.
Conductive carbon fiber and combined graphite has been introduced to improve the chemical resistance over the Kevlar. This also provides thermal conductivity. The composite BMC has passed house testing by several customers and have been in the field for fifteen years with no wear on the components or the shaft.
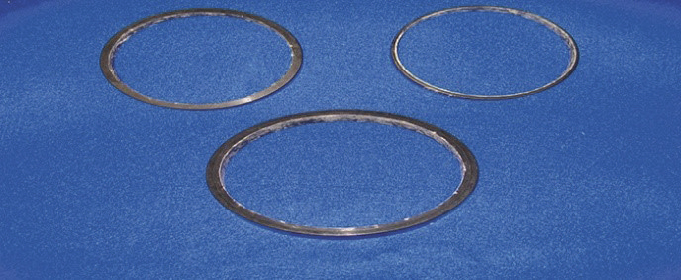
SYNOPSIS
Kevlar is attacked by strong bases while the carbon fiber is affected by galvanic corrosion in seawater. It appears each has challenges, but new fillers are constantly being tested in research and development. The new resin appears impervious to temperatures below 392 degrees Fahrenheit (200 degrees Celsius). The latest effort is to test a special glass fiber combined with the ceramic spheres for seawater applications. It is known that the wear component will not wear, but it is not yet known if the new glass will wear the shaft or if the ceramic beads will maintain the needed separation and prevent wear.
The concept of using ceramic beads to reduce the surface contact area is new. The function of the molded part is totally dependent on the adhesion and dimensional stability found in the new resin. Because this BMC composite is new, addressing any failure mode is the focus. The goal is to define and recommend a product for each application and cover the widest possible temperature and chemical range with zero wear to the bushing or shaft. The resin seems to adhere to everything, so fillers that were never successfully used, such as Kevlar, can now be tested. Adhesion to polytetrafluoroethylene (PTFE) has even been successful.
Randy Lewis has a degree in industrial engineering from Gaston College and over four decades in the business. He has published several papers and set up five plant wide thermoset recycling operations. Plastics Molding Consulting, LLC is a collection of experts in different fields of plastics. They design customer products, make 3D printings for inspection, research and specify molding compounds, modify plastic to specification, and prototype, build, and manufacture myriad plastic parts. For more information, visit www.plasticsmoldingconsulting.com.
MODERN PUMPING TODAY, July 2023
Did you enjoy this article?
Subscribe to the FREE Digital Edition of Modern Pumping Today Magazine!