Figure 1: Cutaway view of a pneumatic pump fitted with a PTFE diaphragm.
Invented nearly 160 years ago, diaphragm or membrane pumps are used in numerous industrial applications. These reciprocating, positive displacement pumps produce a pulsating flow as a hydraulically, mechanically or pneumatically actuated diaphragm moves to draw fluid into a chamber and expel it through a discharge outlet. Diaphragm pumps generally operate at lower volumes and higher pressures than centrifugal and rotary pumps, and are preferred for dry running, moving abrasives or shear-sensitive media, and when there are larger particulates present.
Diaphragms are held in place along their outer edge, allowing the center to move back and forth. Actuation of the diaphragm will vary depending on the type of pump; pneumatic and hydraulic pumps use fluid or air pressing on the back of the diaphragm and mechanical pumps have two pistons gripping the center of the diaphragm with a motor driven shaft.
Pumps using a fluid to actuate the diaphragm can operate at higher pressures, because the diaphragm is pressure balanced, i.e., the fluid pressure on one side is only slightly higher than the pressure of the media, thereby minimizing stress on the diaphragm. Pumps using a shaft and pistons to actuate the diaphragm operate at lower pressures because the diaphragm is under greater stress with most of the pressure on just one side.
Diaphragms are critical components separating the media from the motor or inner workings of the pump. A diaphragm must withstand high pressures, various media, fluctuating temperatures, abrasive particles and steam cleaning, all while flexing and maintaining a tight seal. Whether the diaphragm is flat or convoluted, the volume a pump transfers depends on it maintaining its shape and not stretching out. If a diaphragm fails, the media could damage a pump, and conversely the pump could contaminate the media. Diaphragm failures can result in equipment downtime, maintenance expenses and ruined process media.
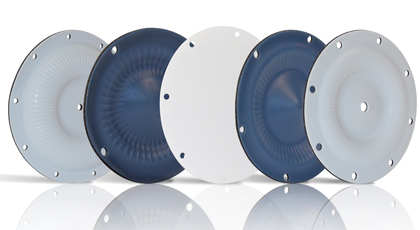
Figure 2: One-piece diaphragms consisting of PTFE bonded to a fabric reinforced rubber backer.
PTFE DIAPHRAGMS
PTFE diaphragms are used in sanitary applications and those involving strong chemicals, abrasives and higher temperatures or pressures. Depending on the type of pump, a PTFE diaphragm can work by itself or with a rubber backing for added strength. It is important to note that not all PTFE diaphragms are the same. Variations in the quality or grade of the PTFE and how it is manufactured can result in significant differences in performance and longevity.
The following tests are typically used on PTFE sheet to indicate its performance: MIT Flex Endurance (ASTM D2176), Tensile Strength (ASTM D1708), and Stretch Void Index (ASTM D4895).
FLEX LIFE
Flex life is an indication of how many cycles a diaphragm can deliver before it ruptures. Traditionally the higher the flex life, the longer a diaphragm will last. However flex life can register artificially high when testing materials with extremely high tensile strength.
TENSILE STRENGTH
Tensile strength helps determine how much pressure a diaphragm can withstand, and whether it will maintain its shape. It is measured along the X and Y axes of the material; if it is not relatively even in both directions, stretching and eventual tearing of the diaphragm can occur over time. Higher pressure applications require high, even tensile strength.
STRETCH VOID INDEX (SVI)
Stretch void index (SVI) measures the voids or air pockets in the material after it has been flexed and indicates the potential for media to permeate into the PTFE. Permeation can sometimes occur with no visible damage to the diaphragm; however it can weaken the PTFE, reduce the diaphragm life and create the potential for cross-contamination. In some cases the media can pass through the PTFE and chemically attack the rubber backing and damage the pump. In pneumatic pumps it can reach the pump exhaust and expose the media to the surrounding environment. Selecting a material with a low SVI is essential when handling critical media, media with a small molecular structure or that can be hazardous to humans or the environment.
A LOOK AHEAD
In next month’s installment, we’ll take a closer look at the two grades of PTFE used in the manufacture of diaphragms—conventional (homopolymer) and modified (copolymer)—as well as a comparison of the performance of sample PTFE sheets produced by skiving, expanding, and calendaring, the three primary methods PTFE production.
About The Author
Michael Brooks is the applications engineer and Sarah Young is the product manager of diaphragms and valves for Garlock Sealing Technologies. They can be reached at michael.brooks@garlock.com and sarah.young@garlock.com. Based in Palmyra, New York, the Garlock family of companies is acknowledged as the global leader in high-performance fluid sealing and pipeline protection products for industry and infrastructure. For more information, visit www.garlock.com.
____________________________________________
MODERN PUMPING TODAY, August 2015
Did you enjoy this article?
Subscribe to the FREE Digital Edition of Modern Pumping Today Magazine!
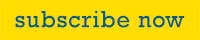