We naturally adjust our expectations within the constraints of what is practical. When we lived in an analog world, we didn’t expect or even easily imagine what would become possible in the digital era. But as technology evolves, we expand our expectations, raise our standards, and eventually become dependent on new levels of performance. That’s what’s happening with grit removal efficiency for wastewater treatment plants and sand removal in potable water plants.
Traditionally, achieving a removal efficiency of 105 microns (140 mesh), classified as “fine” grit, has been regarded as a significant accomplishment. However, the introduction of an innovative new system, the Smith & Loveless Pista® Invorsor®, now enables the reliable and cost-effective capture of “ultra-fine” grit, which includes particles as small as 75 microns.
This advanced system integrates three well-established and validated technologies to consistently achieve a 95 percent removal efficiency for ultra-fine grit down to 75 microns across all flow rates. It ensures consistent performance without derating, across low, average, or peak flow conditions, with a single-unit capacity of up to 50 million gallons per day.
THE RISE OF HIGH-EFFICIENCY GRIT REMOVAL SYSTEMS
The rising demand for high-efficiency grit removal systems is driven by the need to protect plant infrastructure. This trend is particularly noticeable with the increasing adoption of technologies such as membrane bioreactors (MBRs), specialized pumping equipment, and fine bubble diffusers. Effectively removing ultra-fine grit can yield a substantial return on investment by preventing line blockages, deposition in downstream channels, process basins and reducing the fouling of diffusers and membranes. This, in turn, extends the lifespan of downstream equipment, significantly lowers maintenance costs, and enhances overall operational efficiency.
Ultra-fine grit can also present significant challenges to aeration systems. The accumulated grit disrupts oxygen circulation, decreases the efficiency of biological treatment, and increases compliance costs associated with effluent regulations. This buildup limits the volume necessary for optimal retention times in biological treatment and sludge digestion. Manually removing grit from the bottom of basins can cost between $150,000 and $1,500,000 per cleaning, and the cleaning process risks damaging the aeration infrastructure.
The necessity to tackle ultra-fine grit differs by region and season. Geographic location and environmental factors significantly affect the grit size distribution encountered by wastewater treatment facilities. Coastal regions and agricultural areas face elevated levels of ultra-fine particulate matter, and seasonal factors such as winter road treatments also influence particle size distribution. As the diameter of grit decreases, the challenge of removal increases.
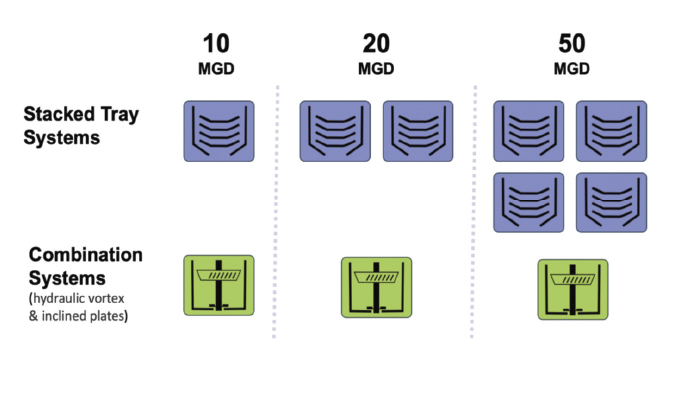
STACKED TRAY SYSTEMS
Around fifteen years ago, the stacked tray system was developed, raising expectations for the removal of ultra-fine grit through gravity-based separation. This method utilizes a series of vertically-mounted trays to expand the surface area in a square settling tank, allowing grit particles to settle gradually from wastewater.
The design features a notable head loss throughout the system, primarily due to the inlet distributor, which evenly disperses the incoming flow across the multiple trays (up to 12 inches / 300 mm). Typically, a continuously operating remote pump is used to remove the grit that accumulates at the bottom of the tank.
While high removal efficiencies are touted for particles as small as 75 microns, efficiencies are typically derated down to 85 percent during peak flow conditions in many of the installations. At such peak flow rates, manufacturers of stacked-tray systems will often only guarantee performance specifications for the removal of particles as small as 212 microns.
Stacked-tray systems are sized and designed based on surface area and particle settling rates, which determine the number of trays and tank depth required. Increased flow demands more surface area to sustain a Surface Overflow Rate (SOR) that effectively removes fine and ultra-fine grit.
Practical limitations on available surface area restrict system capacity. The largest stacked tray systems can accommodate a maximum of approximately 13 million gallons per day for 75-micron removal. To manage larger flows, multiple systems are necessary: 20 million gallons per day requires two systems, while 50 million gallons per day demands four systems. This not only increases the footprint significantly but also necessitates the duplication of ancillary equipment, such as pumps and grit washing and dewatering systems. The additional equipment increases the owners’ O&M expenses.
A LOOK AHEAD
Next month, we’ll take a closer look at how integrating forced vortex technology with inclined plates for both flow and level control lead to a complete solution for downstream treatment needs and demonstrate how the Invorsor works seamlessly with Smith & Loveless grit washing and dewatering systems to ensure true ultra-fine grit removal efficiency throughout the entire process.
As a pioneer of pumping systems for seventy-five years, Smith & Loveless has spearheaded the innovation for above ground pump systems, with continuing advancements in the design and production of these stations. Designed with a focus on robustness and a keen awareness of the most pressing industry challenges, above ground lift stations protect both operators and employers, and offer lifespans that are significantly longer than submersible pumps. It is, therefore, no surprise that operators facing workforce challenges, flushables, and economic pressures are increasingly turning to above ground pump stations over conventional submersible pumps to meet current and future demands. For more information, visit www.smithandloveless.com.