Industrial facilities frequently face challenges with wastewater management, needing solutions that align with EPA and local regulations while keeping costs under control. Automated wastewater treatment systems have emerged as a vital solution, offering significant advantages by streamlining processes and reducing the need for manual oversight. These systems not only help businesses stay compliant but also actively save on labor, treatment costs, and waste disposal, making them a cost-effective and practical choice.
TRADITION VS. INNOVATION
For many facilities, efficiently separating contaminants from wastewater is imperative to legally discharge the treated water into sewer systems or reuse it for other processes. Traditional methods, however, can be cumbersome, requiring multiple stages, various chemical treatments, and consistent manual intervention. Even automated systems often fall short, necessitating in-person monitoring for tasks such as chemical application, mixing, and separation, all while still sometimes producing subpar results that fail to meet regulatory standards.
The alternative option of hauling industrial wastewater offsite for processing is viable but prohibitively expensive. Treating the wastewater onsite is a far more economical approach. Proper treatment produces effluent safe for sewer discharge and a residual sludge that passes toxicity tests, qualifying as non-hazardous waste suitable for landfill disposal. With recent advancements in technology, the integration of fully automated wastewater treatment systems has become a much easier and more cost-efficient solution.
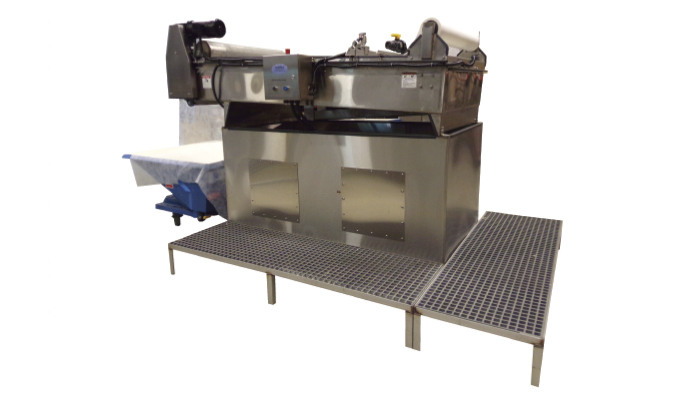
KEEP IT SIMPLE
Modern automated wastewater treatment systems simplify what was once a labor-intensive process into an efficient one-step operation. These systems effectively separate suspended solids, emulsified oils, heavy metals, and other contaminants, transforming the waste into easily manageable sludge in just minutes.
The treated water can then be filtered further—using options like de-watering tables, bag filters, or rotary drum vacuums—before being discharged into sewer systems or reused within the facility. Importantly, the solids generated in this process are non-leachable and classified as non-hazardous, satisfying all testing requirements.
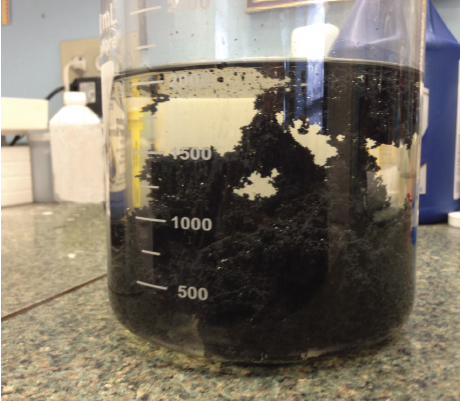
SOLUTIONS FOR EVERY SYSTEM
A broad range of systems is available, from manual and semi-automatic options to fully automated closed-loop systems. For facilities looking to improve efficiency without a complete overhaul, existing setups can often be augmented or modified to achieve better results.
Each facility’s wastewater stream is unique, requiring tailored solutions based on its specific composition and local regulatory demands. Before implementing a new system, businesses must analyze the chemical makeup of their wastewater and consider factors such as volume, local regulations, and available space for installation.
SOLUTIONS AT WORK
One notable success story involves a large, corrugated manufacturer that processes over eight million square feet of packaging daily. Faced with wastewater challenges from the cleanup of its flexographic printing presses, the company opted for an EconoFlow automated wastewater system from Sabo Industrial Corp. The New York-based manufacturer is distributor and integrator of industrial waste treatment equipment and solutions, including batch and fully automated systems, Cleartreat separating agents, bag filters, and accessories.
The solution, combined with separating agents, featured components such as a high-volume mix unit, large capacity feed hopper, bag housing for solids removal, self-indexing dewatering table, and final polishing vessels. Sensors ensure proper material flow and operation, and onscreen audio-visual alerts indicate if anything requires attention.
Remote monitoring capabilities using human machine interface (HMI) technology allowed the system to be adjusted remotely, reducing labor demands and ensuring consistent compliance with water quality standards. Integrated webcams provide real-time feedback, allowing for necessary adjustments without requiring in-person supervision.
While the machinery itself is a critical component of wastewater treatment, the choice of separating agents also plays a crucial role.
Effective separating agents bind with wastewater solids, facilitating their removal. Sabo Industrial uses a special type of bentonite clay in a line of wastewater treatment chemicals called ClearTreat. This line of wastewater treatment chemicals is formulated to break oil and water emulsion, provide heavy metals removal, and promote flocculation, agglomeration and suspended solids removal.
Distinguished by its large surface area and negative charge, bentonite excels at encapsulating contaminants such as heavy metals, oils, and organic pollutants. Unlike polymer-based alternatives, which may fail to fully encapsulate toxins, bentonite-based solutions ensure that contaminants remain securely encapsulated, even under agitation. This not only simplifies the treatment process but also lowers associated costs.
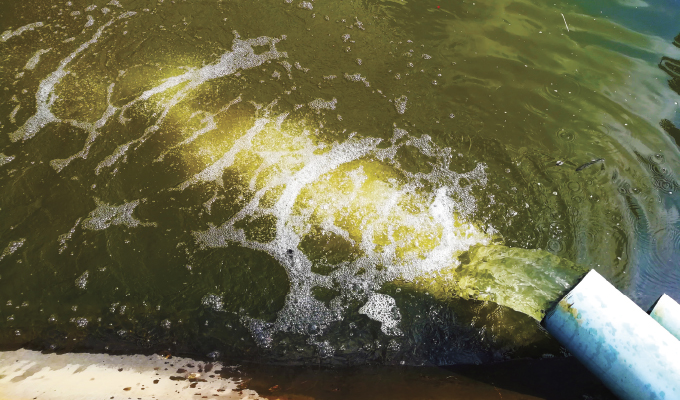
DOING THE DIRTY WORK
Another example comes from a heavy equipment dealer operating several locations across New York and Connecticut. The business required a reliable system for treating wastewater from equipment washdowns that often contained oil, grease, suspended solids, cleaning chemicals, and heavy metals.
The solution included a 10-gallon-per-minute EconoFlow system equipped with features such as bag filters, polishing vessels, and water storage tanks for reuse. The system integrated HMI capabilities, allowing remote monitoring and adjustment of the equipment when needed. It provided efficient, compliant, and cost-effective one-step wastewater treatment.
WORTH EVERY PENNY
By adopting automated systems and advanced separating agents, manufacturers can greatly simplify wastewater treatment processes, reduce costs, and ensure regulatory compliance.
While these systems require an upfront investment, they are far more economical than the ongoing expenses associated with waste hauling or non-compliance fines. Businesses looking to transform their wastewater management approach will find automated solutions to be both reliable and effective, paving the way for a sustainable and affordable future.
Sal Boutureira is the president of Sabo Industrial Corp., located in Orange County, New York. Boutureira has been in the wastewater treatment industry since 1992. He started Sabo Industrial by developing a single step automated system for safe wastewater treatment using Cleartreat separating agents to significantly reduce the cost of treatment, labor and disposal. He believes that every place, every waste stream, is unique, and he is passionate about finding the best, customized solution for each problem. For more information, call 845.562.5751, email info@saboindustrial.com, or visit www.saboindustrial.com.