For ready-mixed concrete plant executives, traditional methods of washing out concrete trucks can seriously compromise efficiency and profitability, wasting a significant amount of time on every washout. Fortunately, new high speed washout systems can now complete the task in just minutes, significantly streamlining operations and boosting profitability.
When examining the benefits of better washout management, producers will likely find significant savings can be achieved by changing their current washout process to a faster, more efficient method. Plant operators need to consider the cost savings available from shorter washout times, as well as additional profits that can be generated from greater driver availability, and even the potential for additional work.
For many concrete plants, the financial benefits of faster washouts can be surprisingly substantial. Some calculation tools indicate that total savings and increased revenue from faster washouts can approach $500,000 annually, or even into seven figures, depending on the size of the operation. Even small operators can achieve savings in the hundreds of thousands of dollars each year.
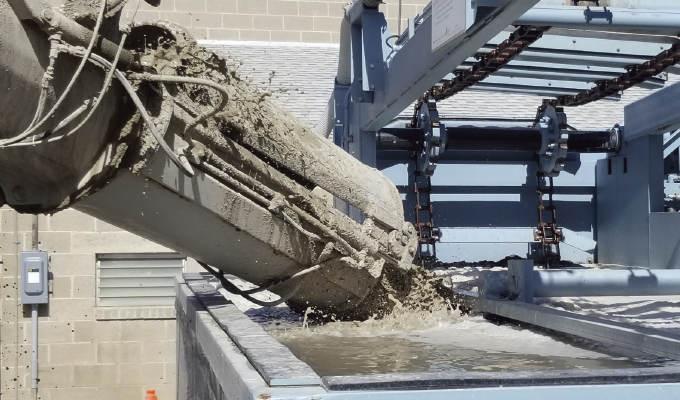
HIGH SPEED WASHOUT EQUIPMENT RECLAIMS TIME, MONEY, AND MATERIALS
After each delivery, washing out trucks and equipment is essential to meet mix specifications, reclaim unused materials, and keep equipment clean. Ideally, washouts should be fast and efficient, and reclaim all reusable materials.
The traditional washout process typically requires drivers to travel to designated washout ponds or pits, sometimes long distances from the plant, to perform washouts. Drivers then manually clean and rinse the truck and discharge the water and concrete into the pit. They then drive back to the plant for the next load. This process can be time consuming and costly.
At some plants, specialized washout equipment is used but the process is often still slow due to the fact that the equipment being used requires concrete to be fed in at a slow rate, again, wasting time.
Today, a much faster, more efficient washout approach is now being utilized. A high speed, self-contained, closed-loop, concrete reclamation and water handling system that can be conveniently located at the plant.
“To perform a washout, the driver backs up to the machine, adds recycled water to the drum, and after mixing, empties the water and concrete into the machine. The system can take eight cubic yards in four minutes, saving producers a significant amount of time.” says Shane Schmutzler, president of Port Washington, Wisconsin-based Jadair International, Inc., a manufacturer of concrete reclaiming and washout systems including the Redi-Claim and Redi-Wash Washout Systems.
He explains that these high-speed washout systems are designed to quickly washout trucks and reclaim the materials. Additionally, the Redi-Wash Washout System clarifies the washout internally, without the use of settling pits or presses. The water is then reused for future washouts. The used cement is discharged separately and can be handled easily by a loader as a dry, clay-like product, reducing mess and saving time.
To help concrete plant executives estimate the potential savings from using a more streamlined washout approach, Jadair offers a savings calculator that evaluates factors such as labor, truck costs, and materials. By inserting these values into the calculator, along with the plant operating hours, the calculator provides insight into the potential savings available from a high speed, automated, washout system when compared to their existing washout method.
With decades of concrete industry experience, Schmutzler offers some illustrative examples of the potential savings for concrete plant executives:
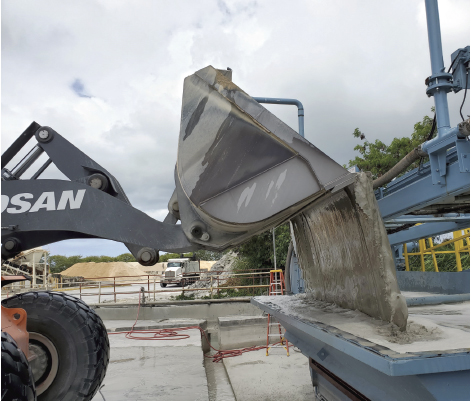
TRUCK AND DRIVER TIME DOWN, ANNUAL SAVINGS UP
Using a high speed, automated, closed-loop concrete reclamation and water handling unit like Jadair’s Redi-Wash Washout System, plants can save as much as $195,000 per year, or more, in mixer truck and driver-related costs.
This figure is derived from an example of a ready-mixed concrete plant with 20 mixer trucks, each washing out twice a day. That equals forty washouts total per day at the plant. With the current washout process, it takes twenty minutes for each driver to washout, including travel to and from the washout pit. Using these figures, the total time taken each day for washouts at this plant is 800 minutes.
In contrast, a high-speed concrete reclamation system can reduce that time significantly. If, with such a system, drivers can now washout in five minutes instead of twenty, then washouts at the plant will only require a total of 200 minutes per day. This puts the total amount of time saved at the plant at 600 minutes per day. A significant number.
If the cost to run a mixer truck is $76/hour, or $1.25/minute, including the driver’s wage, fuel, insurance, etc., this time savings translates into $750/day ($1.25/minute x 600 minutes), for a total of $195,000 per year (260 workdays/year).
This savings is realized by being able to deliver the same amount of concrete each day, with fewer mixer trucks and drivers. The savings calculator available from Jadair details these savings in terms of dollars, as well as in terms of how many fewer trucks can be used at the plant to deliver concrete.
ADDITIONAL DELIVERIES MEAN ADDED REVENUE
With high-speed washout equipment, the plant can deliver the same amount of concrete it currently does while using fewer trucks, thereby saving money. Or, if market conditions permit, plant operators may choose to keep the same number of trucks they currently have, and use the saved time to make extra deliveries, thereby increasing plant revenue. This can be an attractive option.
As an illustration, if the above plant runs ten hours per day, the 600 minutes saved in the previous example is the equivalent of one full workday for one truck and driver. If the plant utilizes this saved time to make extra deliveries, the daily revenue increase could be $3,120.00/day. This is calculated based on the truck delivering an average of four loads/day with an average load size of 6 cubic yards and an average concrete sales price of $130.00/yard. This translates into $811,200/year of additional revenue. Again, a significant number.
“Many ready-mix plants find they can significantly improve operations by using a more efficient concrete washout method. The boost to the bottom line can be even greater if plants make additional deliveries with the extra time freed up from shorter washouts,” says Schmutzler.
RECLAIMED MATERIALS MEANS EVEN MORE SAVINGS
Today, the most advanced high speed washout systems can recover sand and stone for re-sale or re-use, using recycled water in a closed-loop process. This is more environmentally friendly and offers concrete executives the option to sell materials they may have previously paid to haul away.
While reclaimed material is not always suitable for high-spec concrete jobs, it can typically be used in lower-spec mixes such as foundations or used as base material.
“The [concrete reclamation] system separates the clays and cements from the sand and gravel. We could have screened out the three-quarter, three-eighths inch stone from the sand and reintroduced it into our mixes, but choose to sell the material,” says Frank Gelewski, director of operations at Fair Lawn, New Jersey-based Tanis Concrete, Inc., which services major highways, airports, and other state and municipal work throughout Northern New Jersey with three state-of-the-art concrete plants.
Today, these closed-loop, concrete reclamation and water handling units can reclaim virtually all the sand and aggregate from returned loads, generating an additional $25 of savings per cubic yard of processed concrete. The ready-mixed concrete plant in the example might average 20 cubic yards of returned concrete daily for a total savings of $2,500 per week, or $130,000 per year in reclaimed materials.
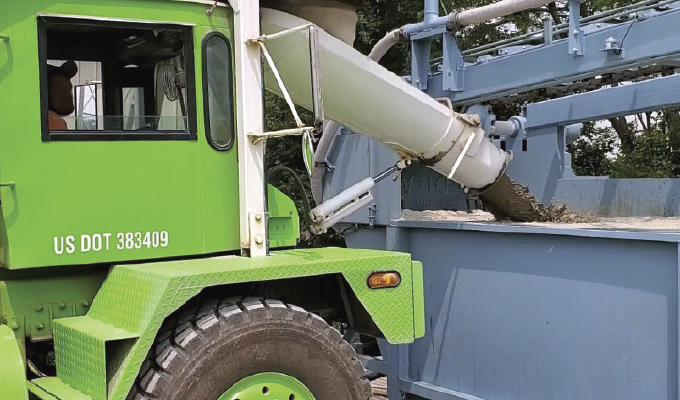
ADDITIONAL SAVINGS IN MAINTENANCE
In washout ponds and pits, the cost to replace make-up water, which is often purchased from a local utility or pumped from wells, can add up quickly.
“We were using metered city water and had to pay for any wasted water,” says Gelewski.
Pond maintenance can also be an issue. Ponds and pits require continual maintenance to remain functional. Ponds need perpetual sludge cleanup and torn pond liners need to be repaired or replaced. Pits fill up with washout material, which must then be excavated and hauled away at additional cost.
“About every three months we had to excavate the pit [of washout material], put it in a stockpile, and let it dry out. The material was mixed with clays, fines, stone, and hydrated cement. It was basically a useless product, so we had to pay to have it hauled away to a concrete recycling facility about 12 miles away. At the time, it cost about $200 a load to dump the material, not counting the truck rental; today, it would cost about $500 a load,” says Gelewski.
Tanis Concrete saved substantially in time, water, and maintenance after installing a three-station, Jadair Redi-Wash Washout System, in their onsite truck garage.
“The water is right there at the washout system. There is no running back and forth from one site to another, so we are saving a significant amount of time compared to the previous washout pit,” says Gelewski.
Since the self-contained, closed-loop, concrete reclamation and water handling system reuses the water, this reduces the need for make-up water typically lost in ponds or pits.
“Our water usage is way down because we are reusing it. We are not wasting water to wash out the trucks only to have it evaporate or hydrate into the ground,” says Gelewski,
Additional savings accrue from eliminating any haul away and disposal fees for unusable materials, which must be excavated and removed from washout pits as part of routine maintenance.
“Now, we no longer need to have a washout pit or a pile of excess material on the side that we have to pay to truck out,” says Gelewski.
SEVEN-FIGURE HIGH SPEED WASHOUT SAVINGS POSSIBLE
When concrete plant executives add up the potential annual savings in truck and driver-related expenses, washout pit maintenance costs, reclaimed material, and the opportunity for increased revenue from extra deliveries, the boost to the bottom line by switching to high speed, automated washout equipment can often total six or even seven figures.
“Altogether we are saving hundreds of thousands of dollars a year in driver’s time, truck time, and trucking material using a modern washout system,” says Gelewski.
Del Williams is a technical writer based in Torrance, California. With over fifty years of industry experience both in the mining and concrete industries, Jadair International Inc. continues to be a leader in the design and development of the highest quality, most capable water clarification and concrete washout and reclaiming systems available. For more information, call 800.669.3411 or visit www.jadair.com.