Vertical turbine pumps (VTPs) are available in a variety of configurations and are used for a number of different applications such as flood control, cooling water, wastewater, and drinking water supply. One of the biggest contributors to pump failures are issues involving the pump bearings. The type of water that lubricates the bearing as it is pumped varies considerably from application to application. Additionally, the amount of abrasives in the pumped water can vary significantly in different regions whereby the amount of abrasives can drastically effect bearing life. It is therefore critical to select the appropriate bearing material for the service as bearing life is influenced by the media being pumped.
The VTP bearings found in the bowl and column assemblies are one of the most critical components of any pump. Bearings not only support the shaft; they also reduce friction on the pumps moving parts. In this series, we’ll begin by looking over some of the most common bearing materials uses in vertical turbine pumps, examine the most frequent causes of bearing failure, and conclude with examples of different Thordon solutions that have met these challenges in the field.
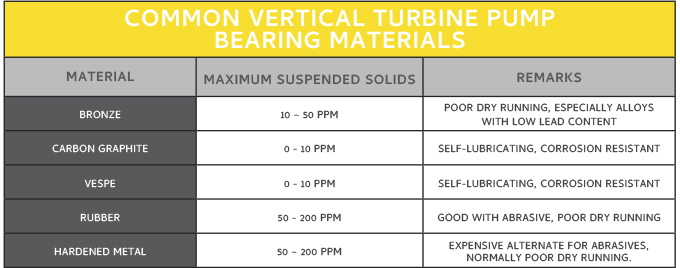
COMMON BEARING MATERIALS USED IN VTPS
Bronze
Bronze is the most popular bearing used in VTPs as it is readily available, easy to machine, and easy to install. However, it has poor abrasion resistance and is malleable and can deform under impact, which can translate into increased shaft clearances. Bronze is also not recommended for dry starts and requires oil or grease, which can contaminate pumped water.
Other limitations include weight and its toxicity. Bronze is seven times heavier than non-metallic bearings making installation of large sizes difficult, and, due to lead content, most bronze bearings are not approved for drinking water. Additionally, bronze can be expensive in large sizes.
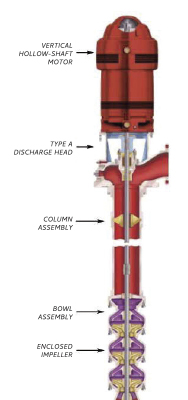
Rubber
Rubber offers good abrasion resistance and accepts some vibration and shock loading but is too soft to install directly into a pump housing and requires a metallic or phenolic carrier to install into the housing. Rubber has a high coefficient of friction, thus dry starts are not recommended. Some manufacturers try to address this by applying a thin layer a nonstick chemical to the bearing. However, while these coatings offer low coefficient of friction, they are often not abrasion resistance so if the pump is running in abrasive water, the coating will wear away and the bearing will lose its dry start capabilities.
Rubber has lower mechanical strength so longer bearing lengths are recommended. Shorter bearings allow abrasives to pass through a bearing quicker and allows water to cool the bearing faster, which can translate into longer bearing life.
Furthermore, rebuilding a pump is difficult with rubber bearings. During the rebuild process the housing and shaft are usually machined and now require a non-standard size. The wall of the metal shell of the bearing is thin to begin with and rubber is difficult to machine so a non-standard size must be ordered. This can lead to long lead times and extra costs. Also, rubber is bonded into the shell, and there are numerous cases of the bond breaking causing catastrophic failures.
Carbon Graphite and Thermoset Laminate
In short, carbon graphite bearings provide good dry running capabilities and temperature resistance, but they offer very poor abrasion resistance. These bearings are typically brittle and can fracture during installation or from thermal shock.
Likewise, thermoset laminate bearings also have poor abrasion resistance and poor dry run capabilities, but are used in some applications due to their low costs. There are many manufacturers and grades of this type of bearing, so physical properties can vary depending on the manufacturer. Most are made with cotton or glass cloth layers impregnated with thermosetting resins.
Another concern arises in the machining of thermoset laminates, which can pose health issues due to fine resin dust being generated during the process. Special breathing apparatus is required. Also, during the machining process, some surface cords may become exposed and leading to significant surface swell which can reduce running clearance causing the pump to bind up.
Thermoplastics
There are many manufacturers of thermoplastic materials using different materials. Some are not preferred for bearing applications—for example, nylon thermoplastics have high moisture absorption and poor abrasion resistance and acetal’s abrasion resistance is worse than nylon and it has poor impact resistance. Polyphenylene sulfide (PPS) has good chemical resistance and thermal properties but can be brittle and crack due to shock or vibration. Due to its chlorine resistance, it is often used as a bearing for applications in water parks and aquariums.
Engineered thermoplastic, such as Vespel and PEEK, are used in many pump applications but are overkill for water-lubricated pumps. More appropriate applications for these materials would be in harsh chemicals or high temperatures.
PEEK has high temperature capabilities combined with good chemical and steam resistance as well as thermal and hydrolytic stability. Most bearing grades are reinforced with carbon fiber or graphite making it challenging to process and machine.
Vespel CR-6100 is a carbon reinforced PFA that can be found in pump applications dealing with harsh chemicals and high temperatures. A specialty product, its higher cost is due to high resin costs and limited number of molds available. AR-1 is another expensive filled PFA, but has lower abrasion resistance and is limited in applications to 100 degrees Fahrenheit (37.8 degrees Celsius).
A LOOK AHEAD: COMMON CAUSES OF BEARING FAILURE
Abrasion resistance and dry start capabilities are the prime causes of bearing failure. Most of the bearing materials mentioned above might be good with one of these issues but seldom are good at handling both. In next month’s conclusion we’ll discus some of the technical factors that create these challenges and the solutions Thordon has been providing to address them.
FOR MORE INFORMATION
Keith Brand is strategic account manager for vertical pumps with Thordon Bearings and has traveled the world training OEM pump engineers how to design non-metallic pump bearings. Thordon Bearings Inc., a Thomson-Gordon Group company, is a family-owned business manufacturing high performance, oil and grease-free bearing systems, seals, and other shaft line products for the global marine, clean power, pump, and industrial markets. For more information, visit www.thordonbearings.com.
MODERN PUMPING TODAY, October 2023
Did you enjoy this article?
Subscribe to the FREE Digital Edition of Modern Pumping Today Magazine!