Recent comments by the American Biogas Council (ABC) on the first Renewable Volume Obligations (RVOs) for the Renewable Fuel Standard (RFS) for 2020, 2021, and 2022 show that the Unites States is finally recognizing the huge potential that anaerobic digestion and biogas has to contribute to a renewable, low carbon economy.
Although the final fuel volumes set out by the Environmental Protection Agency (EPA) may be disappointing and lower than the industry was expecting, the ABC statement contains much to be positive about, not least the high levels of investment and growth in the American biogas sector.
INVESTING IN RENEWABLES IS AS EASY AS ABC
According to the ABC, “new renewable natural gas (RNG) projects have increased by 47 percent in the last year, on—farm projects have increased by 21 percent; and major companies have announced investments in new RNG projects totaling over two billion dollars, twice the industry’s total investment in 2020.”
This level of investment provides a clear message about the technology and its potential. However, it is important with the focus on the production of RNG not to forget about the other output of anaerobic digestion—the production of digestate.
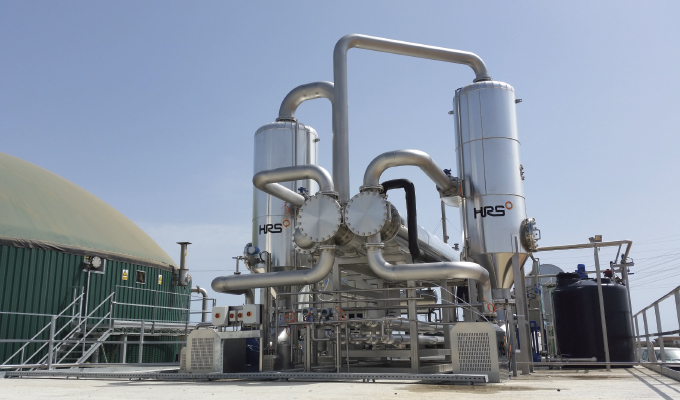
MORE THAN AN AFTERTHOUGHT
Frequently in the United States digestate has been viewed as an afterthought and frequently used as livestock bedding. However, such an approach greatly underestimates the environmental and financial benefits that digestate has when used as a high-quality biofertilizer and soil conditioner for crop production.
The use of digestate as a sustainable biological fertilizer can be improved with pasteurization to prevent the spread of pathogens, weed seeds, and crop diseases. One of the most energy-and cost-efficient methods to pasteurize digestate is the HRS Digestate Pasteurization System (DPS), which is based on heat exchangers rather than tanks with heating jackets. Using heat exchangers means that effective digestate pasteurization is possible using surplus heat while allowing additional thermal regeneration levels of up to 60 percent.
The standard three-tank DPS provides continuous pasteurization, with one tank being pasteurized while one is filling, and another being emptied. The DPS uses a double-tube heat exchanger to heat the digestate to 167 degrees Fahrenheit (75 degrees Celsius) above the required pasteurization temperature. This allows for variation in the sludge consistency and its incoming temperature, making sure that the digestate is always properly pasteurized. The tanks can also be used individually, for example to allow for routine maintenance.
TIME TO CONCENTRATE
Another system to improve the management and handling of digestate is the HRS Digestate Concentration System (DCS), which uses patented technology to reduce the volume of liquid digestate up to 90 percent, raising the concentration of total solids to 20 percent solids while also maximizing the nutrient content, using heat from the AD plant’s CHP engine. Lower water content also means reduced transport costs and field traffic, bringing further benefits in terms of reduced compaction caused by the application of the digestate to land.
Another benefit of the DCS is odor and ammonia control, which helps increase the nutrient content of the digestate. The high temperatures and vacuum conditions needed to concentrate digestate can cause the release of ammonia, largely responsible for the odors associated with digestate. The DCS overcomes this by acid-dosing the digestate with sulfuric acid, thereby decreasing the pH levels. This turns the ammonia into ammonium sulfate, which is not only less odorous, but is also an ideal crop nutrient.
Matt Hale is international sales and marketing director for HRS Heat Exchangers. He began his career in the food and dairy processing sectors in the late 1980s before moving into sales in the mid 90s. He has been involved with heat exchanger systems since 1997 and has held a number of sales roles at senior management level. Hale joined HRS in 2013 as international sales manager, where he utilized his expertise in key account management and distribution. Since 2015 he has had responsibility for the HRS Group’s global marketing. For more information, visit www.hrs-heatexchangers.com.