By Christina Ducey, Fortress Technology
The industrial automation market in food safety and inspection is set to grow by $648.69 million between 2021 and 2025, accelerating at a compound annual growth rate of over 5 percent. Factors such as significant cost savings in operations due to process control and the growing benefits of inspecting bulk foods inline are anticipated to drive the most growth, says a report by Technavio Research, suggesting that demand for high performance gravity metal detectors will continue unabated.
A critical part of most food production processes, inspecting and removing metal contaminants in upstream free-falling dry product applications, Fortress Technology draws attention to several recent enhancements to its robust Stealth Gravity Metal Detector. All designed to advance productivity, enhance safety and maintain HACCP compliance in the busiest of food processing plants.
With productivity being such a critical measurement of output per hour, machine uptime on any fast-moving gravity inspection line is critical. Custom manufactured to accommodate different food factory layouts, including mezzanine floors, ceiling mounts, and between product chutes and hoppers, the Fortress Stealth Gravity Metal Detector is packed full of useful labor- and time-saving features—including automatic testing to eliminate production downtime, plus accurate, high speed reject capabilities.
ADDING VALUE THROUGH SPEED AND SAFETY
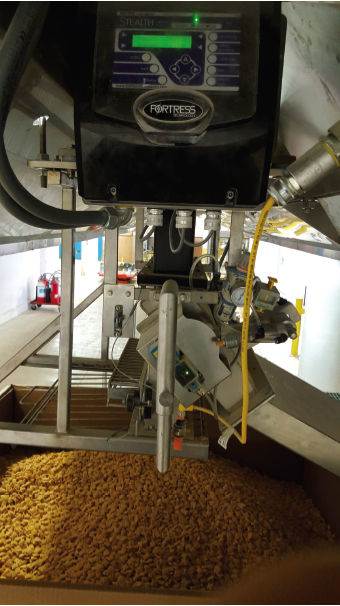
Offering best-in-class detection of magnetic and non-magnetic metals, Fortress Gravity Metal Detectors are an everyday sight on North American flour, rice, cereal, sugar, powder, and grain production lines.
“There is always value to be gained from adding upstream detection systems to most processes,” explains Regional Sales Manager Eric Garr. “Upstream detection often makes it easier to detect contaminants, trace to their source and potentially alert staff to equipment failures before they become catastrophic and potentially trigger huge recalls.”
Scanning raw materials as ingredients come into the factory is prudent for many reasons. Although in most instances these ingredients would be inspected by the supplier, a reinspection will help to doubly ensure that suppliers are complying and hold them accountable for ingredient quality, reaffirms Garr “Of course, the most notable benefit is preventing metal from entering the production process in the first instance. Rejecting at the end of the line is typically the most expensive phase.”
For hazardous locations, such as flour factories or chemical plants where the application presents a combustible explosion risk, Fortress supplies clear ratings to meet the defined hazardous location standards. Always mindful of real factory conditions, the robust Stealth Gravity Metal Detector is built to be sturdy and stable enough to withstand vibrations and temperature changes without compromising performance.
Available in a selection of food-grade anti-static in-feed pipe standard sizes, including 3, 6, and 8 inches, Fortress Gravity Metal Detectors apply powerful digital signal processing technology to identify the smallest of metal fragments. Operatives are instantly alerted to any detection by an audible and visual alarm. A reject confirmation alert verifies that the reject device has operated correctly during every reject.
SMARTER ABOUT SAFETY
To remove metal contaminants from good product flow, many Fortress customers now specify the company’s roll-out easy clean diverter valve reject system. Much faster to sanitize, this design overcomes a longstanding challenge with gravity systems—gaining access to the enclosed flap-style reject mechanism and removing from service for deep cleans and maintenance. By placing on a carriage, processing operatives can quickly disconnect, slide out, gain access to working parts, clean, and slot back into place, with minimal business disruption.
To successfully comply with application-specific production standards, food plants also need an appropriate and effective testing system. Defined by the audit process of industrial metal detectors, tests are typically scheduled throughout the day at hourly intervals to confirm the gravity inspection system is repeatedly identifying all potential metal contaminants.
Manually performing these regular tests on gravity metal detectors can be especially time consuming. Mainly due to challenges of accessing machinery positioned at height. “It is virtually impossible to time and again replicate a metal contaminant passing through the exact center of the product flow within the aperture in free-flowing applications,” notes Garr.
“One of the biggest pitfalls of manual testing in Gravity applications is dropping the test sample from a height, through the center of the product flow where the signal is the least sensitive,” he highlights. With many gravity metal detectors located near product silos above production lines, climbing up to perform this task manually is usually a two-person task and brings with it some significant safety risks.
To solve this dilemma, Fortress created Halo Automatic Testing. An alternative to manual performance testing, Halo mimics the signal disturbance in the center of the aperture, without having to physically pass a metal contaminant through the metal detector or flush out a sample. In addition to reducing operational costs, Halo testing is proven to reduce waste and product rework. Through the incorporation of all these innovative features, Fortress asserts that its popular process-centric inline gravity applications are now internationally regarded among the safest to operate and maintain.
Christina Ducey can be reached at 416.752.2898 ext. 312 or cducey@fortresstechnology.com. Fortress Technology Ltd. is a privately-owned Toronto-based company and is the only metal detection manufacturer that, since its inception in 1996, custom manufactures metal detectors to suit its customers’ needs, application, and specification while ensuring optimal performance. Fortress systems are used widely within a range of food industry sectors including bakery, meats, ready meals, dairy, confectionery, fresh foods, and frozen foods. In addition to product manufacture, the company offers a range of before and after sales service and support services. For more information, visit www.fortresstechnology.com.
MODERN PUMPING TODAY, June 2022
Did you enjoy this article?
Subscribe to the FREE Digital Edition of Modern Pumping Today Magazine!