By David Steil, Camfil Air Pollution Control
Effectively controlling toxic and combustible dust generated in chemical processing facilities is essential to protecting employee health, maintaining product quality, and preventing devastating explosions. This article examines these dangers, applicable regulatory guidelines, and how to use a high-efficiency dust collector to keep workers safe and facilities in compliance.
DUST HAZARDS IN THE CHEMICAL PROCESSING INDUSTRY
Controlling toxic and combustible dust is a common yet serious challenge in the chemical processing industry. Everyday processes like mixing, conveying, and blending create dangerous dusts that become airborne, endanger air quality, and can create fire and explosion hazards.
Although each processing facility has unique dust issues based on the raw materials used, they must all comply with worker exposure limits, environmental regulations, and combustible dust standards.
Chemical processors must comply with Occupational Safety and Health Administration (OSHA) regulations to protect their employees from exposure to airborne dusts, as well as National Fire Protection Association (NFPA) standards to provide a safe working environment.
OCCUPATIONAL EXPOSURE TO TOXIC DUSTS
Regular exposure to certain types of chemical dust particles can be hazardous and irritate the eyes and skin. Such conditions can cause health problems for workers and may require treatment and protective equipment. Other fine chemical dusts can travel deep into the lungs, becoming embedded and causing serious respiratory conditions such as occupational asthma and even lung cancer.
OSHA regulations govern employers whose processes generate dust, and the agency will issue citations and fines for lack of compliance. Under OSHA, companies must control toxic chemical dust emissions into the indoor workplace atmosphere to comply with the established permissible exposure limit (PEL) for workers. If no legal limits are applicable, then the company is required to define in writing, implement, and measure its own environmental safety plan to comply with the general duty clause.
OSHA REGULATIONS GOVERNING OCCUPATIONAL EXPOSURE
OSHA 1910 is a broad, general standard that covers most industries. It is a comprehensive and complex standard with twenty subsections. OSHA PELs include limits on airborne concentrations of hazardous chemicals in the air for general industry in 1910.1000–Air Contaminants. They are listed by chemical name in Tables Z-1, Z-2, and Z-3. Most OSHA PELs are eight-hour time-weighted averages (TWAs), although there are also ceiling and short-term exposure limits (STELs). Many chemicals include a skin designation to warn against skin contact.
- OSHA 1910.22: Walking-working surfaces is a housekeeping standard that requires all places of employment, passageways, storerooms, service rooms, and walking-working surfaces to be clean, orderly, dry, sanitary, and free from hazards. This means that manufacturers must prevent dust from accumulating on these surfaces.
- OSHA 1910.134: Personal protective equipment (PPE) requirements aim to minimize occupational diseases caused by breathing air contaminated with harmful dusts, fumes, mists, gases, smokes, sprays, or vapors and coming into physical contact with these dusts. It recommends accepted engineering control measures to mitigate these risks as a first step before relying on PPE.
- OSHA 1910:307: Hazardous (classified) locations covers the requirements for electric equipment and wiring in locations where there is a risk of fire or explosion because of the presence of flammable vapors, liquids or gases, or combustible dusts or fibers.
Furthermore, the National Electrical Code (NEC) defines hazardous location types, and many chemical processing facilities are Class II, where there is a sufficient amount of combustible dust present in the air to be explosive or ignitable under normal, everyday operating conditions.
REDUCING WORKER EXPOSURE TO TOXIC DUST
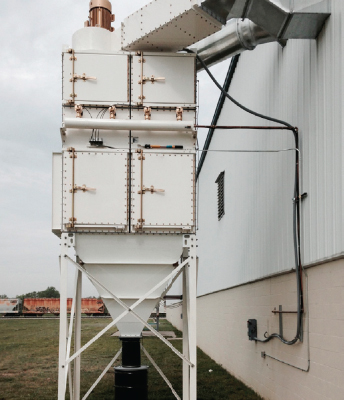
The best way to reduce workers’ exposure to hazardous dusts is to install a dust collection system with high-efficiency primary and secondary cartridge-style filters. It is preferable to capture chemical fumes and dust at their source to prevent them from expanding throughout the plant. This is accomplished by incorporating a hood or extraction arm into the chemical process machinery. Source capture is extremely effective, and it requires the least energy and capital investment.
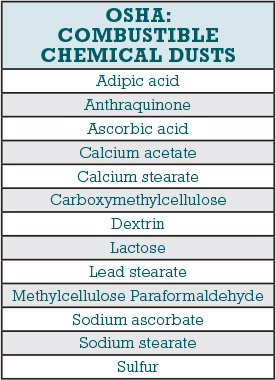
However, once they are captured, dust should be isolated from the rest of the facility and contained in a specific area. For example, a portioned area can be kept under negative pressure. The extracted air is either drawn directly into a local collector or ducted to a dust collector located remotely. In some cases, the filtered air can be safely returned back into the facility to create a push-pull airflow pattern to improve the contaminant control.
A chemical manufacturing facility may also require special options or accessories to improve the safety and reliability of the system. Bag-in/bag-out filters and hopper discharge options can be used to limit exposure and cross-contamination of collected material when performing filter and dust removal maintenance. Additional features such as duct and equipment clean-out doors, stainless steel construction, safety after-filters (HEPA), and FDA-compliant paint are also commonly used with the air filtration unit based on contaminant properties.
TYPES OF FILTERS AND FILTRATION MEDIA
Primary filter media should be selected for each application based on the dust particle size, flow characteristics, quantity, and distribution. If the dust being collected is toxic and the primary filtration system does not use a HEPA filter, it is recommended that a secondary HEPA filter be used downstream. Secondary filters prevent hazardous dusts from discharging to the atmosphere and can be configured to prevent return air ducting contamination and the associated costs of cleaning hazardous dust leakage.
A wide, uniformly pleated filter allows the collected dust to release from the filter, keeping the resistance lower through the filter for a longer period of time. When the pleats of the filter media are tightly packed, the reverse pulse cleaning system of the dust collector will not eject the dust that has settled in between the pleats. Tightly packed pleats increase the resistance of the air through the filters and diminishes airflow, thus shortening filter life.
There are two basic categories of media commonly used in pleated cartridge filters. The choice is usually driven by dust type, operating temperatures and the level of moisture in the process:
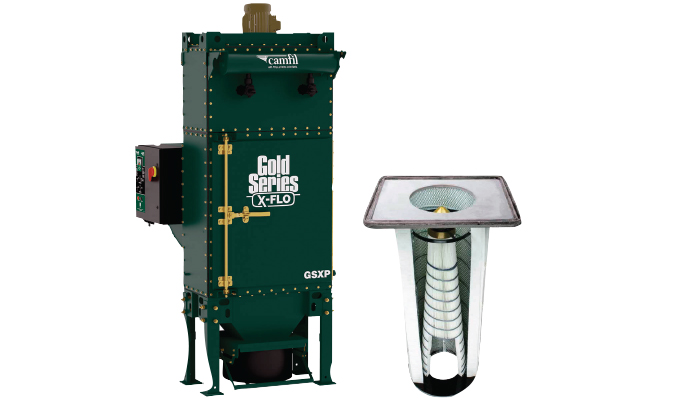
Nonwoven cellulosic blend media is the most economical choice for dry dust collection applications at operating temperatures up to 160 degrees Fahrenheit (71 degrees Celsius).
Synthetic polyester media or polyester-silicon blend is a lightweight, washable media that can handle dry applications with maximum operating temperatures ranging from 180 degrees Fahrenheit (82 degrees Celsius) up to 265 degrees Fahrenheit (129 degrees Celsius). These filters are washable and can recover from a moisture excursion, but they are not intended for wet applications.
Standard and nanotechnology filter media treated with a flame retardant are recommended for applications considered a fire risk. Conductive or anti-static filters may be used where conveyed dusts generate static charges that require dissipation. Cartridge filters with anti-static media can also be used in explosive dust applications, making it possible to conform to NFPA requirements and lessen the risk of ignition sources due to static electricity charges.
High-efficiency dust collection systems also use self-cleaning mechanisms that regularly pulse dust off the filters, allowing units to run longer between filter change-outs. When a layer of nanofibers is applied on top of the base filter media, it promotes surface loading of fine dust and prevents the dust from penetrating deeply into the filter’s base media. This translates into better dust release during cleaning cycles and lower pressure drop readings through the life of the filter.
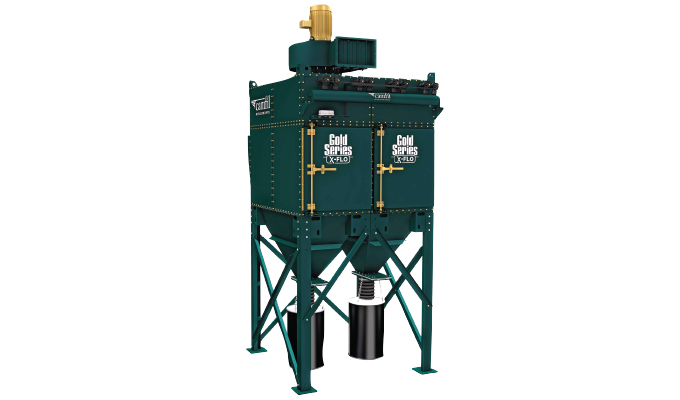
COMBUSTIBLE DUST EXPLOSIONS
A dust explosion occurs when a confined and concentrated combustible dust cloud comes into contact with an ignition source. Many chemical dusts qualify as combustible dusts. These chemical dusts can accumulate on surfaces, where a spark or flame can ignite them, causing a fire or explosion. Common ignition sources are kilns or a welding flame, but they also can be a lit match or cigarette.
Good housekeeping and installing a well-designed dust collection system can prevent airborne dust from building up in the work environment, on electrical equipment and other areas where dust can accumulate, such as false ceilings.
These measures help to negate the risk of a primary and/or secondary explosion. The primary explosion is the first point where an explosion occurs and is usually an isolated incident. A secondary explosion occurs when the primary explosion pressure disturbs the dust collected in the areas mentioned above, creating a far more extensive and potentially deadly explosion.
Dust collectors minimize the amount of combustible dust that can collect on floors and other surfaces, and they contain chemical dust in one area. But the dust collectors themselves can be a fire or explosion hazard if they are designed incorrectly or not equipped with the proper explosion protection controls.
A LOOK AHEAD
In next month’s conclusion, we’ll review the regulations governing combustible dust—from the NFPA, OSHA, and the U.S. Chemical Safety Board—as well as look over techniques for mitigating combustible dust and its exposure. Effectively controlling the dusts generated in chemical processing facilities is an essential life-saving and legal obligation, so these points will be of interest to anyone mindful of reducing hazardous dust.
FOR MORE INFORMATION
Camfil Air Pollution Control is one of the world’s largest manufacturers of industrial dust, mist, and fume collection equipment. As part of the global Camfil Group, we’re represented on six continents and draw upon over five decades of experience and expertise to ensure that our customers are kept safe and productive. Every manufacturing process creates some kind of dust, mist, or fume. These byproducts can be harmful to workers, and they can cause machinery to become less efficient. Camfil APC’s product range is designed to keep your workforce safe and healthy, and ensure that your operations and processes remain as efficient as possible. For more information, visit www.camfilapc.com.
MODERN PUMPING TODAY, May 2021
Did you enjoy this article?
Subscribe to the FREE Digital Edition of Modern Pumping Today Magazine!
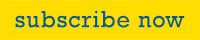