By Eric Ford, Graphite Metallizing Corporation
Graphalloy bearings and bushings, manufactured by Graphite Metallizing Corporation, are used in many light hydrocarbon pump applications to help eliminate operational problems. Light hydrocarbons are a difficult pump service for bushing selection because they have low lubricity, poor viscosity, and are prone to flashing.
Graphalloy is a unique family of graphite-metal alloys. The makeup of these materials mean that Graphalloy bushings are non-galling and self-lubricating, which allow the pumps to continue working even when upset conditions occur. Should the pumps run dry for extended periods of time, these same features can protect the pump for significant lengths of time without any liquid film lubrication. Graphalloy is a great match for fluids such as natural gas liquids (NGLs), LNG, CO2, and other light hydrocarbons.
FACING THE CHALLENGE OF LOW LUBRICITY FLUIDS
Light hydrocarbons, LNG, and natural gas liquids (NGLs) can be especially difficult for traditional metal bushings and wear rings because they have low lubricity which means the hydrodynamic film between the shaft and the bushing sometimes is unable to be maintained, which can lead to metal-on-metal contact, frequently galling or seizing the pump. Because of Graphalloy’s unique properties, it eliminates these concerns and protects the shaft of the pump when pumping these fluids. Graphalloy does not gall and it does not seize. This allows Graphalloy bearings and case rings to have tighter clearances, which improves reliability, lowers vibration, and increases efficiency in vertical and horizontal pumps.
Polymer (plastic) materials are used in many pump applications but perform poorly in low lubricity fluids, such as LNG and NGLs. These materials can crack in extremely cold environments and can cause shaft seizure. Graphalloy can handle temperature extremes, from -400 to 1,000 degrees Fahrenheit (240 to 535 degrees Celsius), well outside the range of polymer materials.
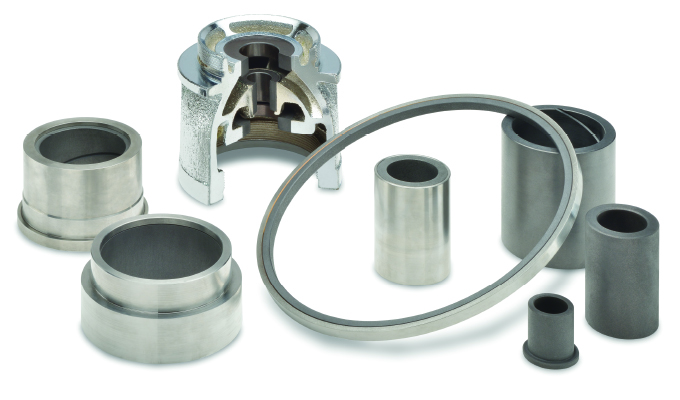
BENEFITS OF SELF-LUBRICATION
Recently, a customer contacted engineers at Graphite Metallizing with a special request. Their company was providing single-stage, axial-split case, double-suction, between bearings pumps for a floating liquid natural gas (FLNG) ship prototype. The customer contacted us because they knew that the non-galling, self-lubricating features of Graphalloy would allow the pumps to continue working even when experiencing run-dry, flashing, or cavitation.
The bushings were needed in a hurry. Because the pumps would be installed at the bottom of the ship, they needed to be in place before further construction could proceed. As the project manager described the situation, “timely completion of a multi-billion-dollar project depends on timely delivery of our pumps.”
FAST AND RELIABLE
The project involved multiple pumps of several different sizes. A further complication was the need for metal holders in both 316 and duplex stainless steels. With tightly coordinated actions, Graphite Metallizing and the customer’s personnel solved the problems of procuring the holders, re-machining the Graphalloy bushings and adjusting the drawings. This was completed within an aggressive time frame so that the customer could honor its delivery commitments to the end user.
FOR MORE INFORMATION
Available in over 100 grades, Graphalloy bearings may be the solution to customers’ toughest bearing, bushing, thrust washer, cam follower, or pillow block bearing design problem. Some Graphalloy bearings have operated for up to twenty years without maintenance. Graphite Metallizing Corporation has many standard designs but most of its products are custom designed to the unique requirements of specific application. For more information, visit www.graphalloy.com.
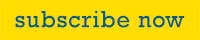
MODERN PUMPING TODAY, December 2019
Did you enjoy this article?
Subscribe to the FREE Digital Edition of Modern Pumping Today Magazine!