By Chinmay Shete, Machfu
Rotating equipment, used widely in industrial processes, is relied upon to move fluids and gases through production operations and throughout the supply chain, and transmit power in motors and drives. These systems are designed for handling oil and gas, and other volatile and hazardous chemicals under abrasive conditions and pressure changes, where safety and emissions containment are crucial. Frequently operating in remote locations, such as onshore and offshore oil and gas well sites, and throughout long-distance pipelines, failure of pumps and other rotating equipment can have dire consequences, jeopardizing environmental safety and energy resources. The failure of a single mission-critical pump, fan, blower, or turbo-compressor can interrupt production, resulting in millions of dollars per day in lost throughput revenue.
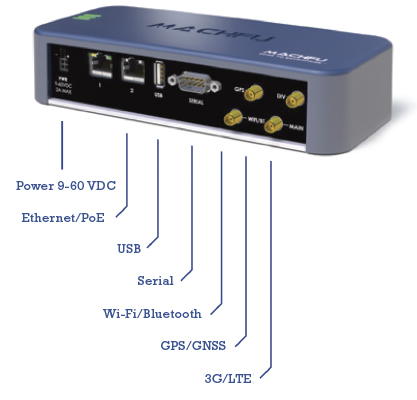
CONDITION-BASED MAINTENANCE
Because industrial plants have processes that contain abrasives and solids within the fluids being pumped, these insoluble liquids are hard on rotating equipment, creating added abrasion and erosion of the components. As with all rotating equipment, component wear is a constant factor requiring monitoring, maintenance, repair, and replacement to keep the equipment operating as required.
However, due to the sometimes thousands of pumps and other rotating equipment needed to be inspected and serviced in a plant, it is inevitable there will be some degree of delayed or missed routine maintenance, or improper system servicing, resulting in equipment failure. Further, frequency-based maintenance protocols are not a guarantee for predicting or identifying early-onset machine disruptions, which eventually precipitate equipment failures.
A growing number of process plants are converting from frequency-based preventative maintenance of their rotating equipment to condition-based maintenance strategies, which provide a higher level of reliability against equipment failures and system downtime. It also enables better asset utilization and system longevity.
- Condition-based maintenance consists of three basic functions:
- analysis of the data to assess machine performance over time, and
- alerting maintenance personnel of machines exhibiting rotating aberration.
CONDITION MONITORING OF VIBRATION
Condition monitoring is essential to a condition-based maintenance protocol. With condition monitoring, data is collected from one or more functions of a rotating machine. These can include vibration, lubrication, temperature, pressure, motor current signature, and electric discharge. This data is collected, either manually or via wireless network, then input directly into a maintenance database, or uploaded to the cloud, for subsequent analysis.
With rotating equipment, vibration is a key factor recorded, and every machine has its own vibration characteristic. Multiple recordings of vibration from a specific machine will enable a baseline to be set for that machine. So, even minor changes in vibration in any singular machine may signal the need for a closer inspection.

i-ALERT® BLUETOOTH EQUIPMENT HEALTH MONITOR
Where many plants are checking and recording vibration signatures in rotating equipment with handheld devices, technology is rapidly supporting the acquisition of machine condition data through wireless monitoring.
ITT, Inc. has developed a machine monitor (sensor) adapted for particular application with rotating equipment, called the i-ALERT® Bluetooth Equipment Health Monitor. This sensor, which mounts directly onto the rotating equipment, tracks tri-axial vibration, tri-axial kurtosis, temperature, and run-time hours 24/7/365. It wirelessly syncs this data to an i-ALERT mobile app, via Bluetooth Smart-enabled devices, then uploads the data to the cloud. Data signatures of the machine are uploaded continuously, and alarms if the equipment is outside of normal operating conditions, visually alerting users, and wirelessly broadcasting an alarm message.
The sensor provides powerful vibration analysis tools similar those found on pro handheld vibration analyzers, with the simplicity that any technician who can operate a smart phone or tablet can easily integrate with the i-ALERT monitor.
IIoT GATEWAY ENABLES CONTINUOUS UPLOAD OF SENSOR DATA TO THE CLOUD
The Industrial Internet of Things (IIoT) is creating new methodologies to collect, process, and push data from the network edge to back-end servers using cloud-based systems. i-Alert monitoring has leveraged some of this technology to enhance its functionality by: a) continuously uploading machine performance information to the cloud; and b) uploading this data without the need of a technician to scan the monitor at the equipment site. This is made possible because of the system’s highly adaptable IIoT application gateway.
Developed by Machfu, the MachGateway® provides a rich set of edge functionality, collecting data by constantly polling the machine sensors at the edge, assessing the system state every second. The information gathered is used to create a data model that can be easily understood by other applications and translated to other protocols, allowing the data to be shared in real time with the ecosystem of emerging IIoT applications, while maintaining connectivity with the plant’s existing SCADA system.
LEVERAGING CELLULAR INFRASTRUCTURE
The MachGateway fully utilizes cellular’s high bandwidth and low latency, using applications such as AWS IoT/ -SparkPlug via MQTT or AWS API Gateway via HTTPS connectivity.
From Sensor to Cloud to Back-End
Instead of processing all of the sensor data in the cloud, the MachGateway processes the data at the edge. Here is the protocol for data transmission:
- i-ALERT sensor monitors machine vibration;
- The sensor sends alarm over Bluetooth if vibrations cross a threshold;
- MachGateway requests complete vibration data;
- The sensor sends requested data;
- The gateway processes vibration data;
- The gateway sends processed data to AWS IoT;
- The data is further processed in AWS infrastructure;
- The processed data is sent to ITT PRO Services® backend;
- Visualization and analysis tools help to identify the problem.
Security
The MachGateway platform has defense-in-depth security built across the layers of the communications stack, all the way up to the application layer. Consequently, it implements the best practices of IT security, considerably exceeding that provided by SCADA systems.
The platform has a secure sandbox for different applications, each with its own crypto-technology for data and sharing of data between applications. Importantly, however, the security built into this gateway does not put a heavy burden on the system.
Adding Sensors
The gateway leverages the new high-performance hardware platforms using a hardware-independent Android/Linux-based software platform. Simultaneously leveraging chip/module-based connectivity solutions that are lowering wireless connectivity costs.
The gateway provides many features that simplify the development of edge applications by reducing the time to create and integrate them. This enables innovative edge applications to be created and rapidly integrated to existing infrastructure and IIoT applications.
LEVERAGING MACHINE ANALYTICS
Data from individual rotating equipment can be used in multiple applications, including overall equipment effectiveness, loss, waste, production efficiency, and even identifying if differences of efficiency exist between similar pumps and compressors.
Within this framework, data can be collected to a big-data cloud database which is designed to efficiently provide information to different applications that are requesting data. This means that a much higher volume of data can be gathered from the machine metrics and made available in a common format, to allow for broader usage and analytics.
FOR MORE INFORMATION
Siemens Digital Industries Software, a business unit of Siemens Digital Industries, is a leading global provider of software solutions to drive the digital transformation of industry, creating new opportunities for manufacturers to realize innovation. With headquarters in Plano, Texas, and over 140,000 customers worldwide, we work with companies of all sizes to transform the way ideas come to life, the way products are realized, and the way products and assets in operation are used and understood. For more information, visit www.sw.siemens.com.
Chinmay Shete is director of embedded software at Machfu. Machfu simplifies the complex landscape of Industrial IoT by easily connecting data at the edge to the cloud and legacy enterprise systems, for business analytics. Its products, the Machfu Platform and Gateway, bring edge-to-enterprise connectivity to existing industrial infrastructure that can be deployed and scaled quickly. Machfu’s gateway platform has the hardware interfaces, device protocol libraries, cloud protocol libraries, and legacy SCADA system connections to enable connecting any industrial device to any back-end system easily. For more information, call 301.540.5372 or visit www.machfu.com.
MODERN PUMPING TODAY, September 2019
Did you enjoy this article?
Subscribe to the FREE Digital Edition of Modern Pumping Today Magazine!
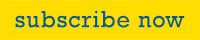