Bradleys, Inc. has recently expanded its world class Hi-Power Electric Motor Load Testing System to include large vertical motor load testing. Bradleys is located just sixty miles from the Eagle Ford Shale play in Gregory, Texas, and is an internationally recognized leader in the electric motor repair and load testing industry. The company’s proximity to the fourth largest deepwater port in the United States, Port of Corpus Christi, and to rail lines and state highways allows the company to serve customers from around the world. The company’s 110,000 square foot production facility offers state of the art electric motor repair and consulting, up to 50,000 horsepower motor rewinding, load testing, climate-controlled motor storage, field services, and new motor sales.
A HISTORY OF QUALITY
Bradleys is committed to providing the electric motor industry with a cradle to grave environment for its customers. This new capability is just one more example of the company’s dedication to the industry. Since 1930, Bradleys has led the electric motor repair industry in unsurpassed capability, quality, and the latest technical advancements.
Five generations of ownership and involvement on the production floor is a testament to our family’s commitment to this company and the industry. Our goal is to exceed our customer’s expectations, every time.
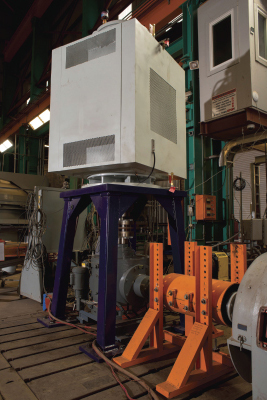
LOAD TESTING: A CLOSER LOOK
Load testing is critical to ensure reliability of motors in the field and in mission-critical situations. Load testing a motor has the following benefits:
- A critical motor recently repaired can be tested to validate the success of a major repair without the expense of installation and start up delays. If a motor has performance issues it may be easier to load test the motor on a different installation to determine if the problem is motor related or site related.
- If a critical motor is destined for a warehouse for many years and high reliability is important, testing has value.
- In today’s world, many used motors are repurposed for different applications. Some of this repurposing requires horsepower and speed changes. Load testing the motor can validate the redesign.
- Some organizations have had serious and expensive startup issues with problematic systems. Load testing a motor and drive system can help minimize the startup problems. Systems can be overloaded to verify trip circuits. VFD systems can have power studies performed to verify compliance with strict power quality requirements. A twenty-four- to forty-eight-hour burn-in test can be performed to help eliminated infant mortality failures.
STAND OPTIONS
To serve the increasing vertical motor load testing needs of customers, Bradleys built two different load test stands. For a motor weighing 50,000 pounds or more, Hi-Power Stand 1 accommodates 0-1,200 rpm up to 2,500 horsepower, and 24,000 lbf foot torque; Stand 2 is designed for motors weighing 15,000 pounds or more; and accommodates 0-3,600 rpm up to 2,000 horsepower and 8,000 lbf foot torque.
These stands are designed with vibration monitoring in mind. All of the typical performance parameters are monitored and recorded during the load test. All power (KW, KVA, Volts, Amps, power factor, efficiency, etc.), temperatures (six stator, two bearing, two ambient, cooling water, etc.), speed, torque, vibration, and other required data points are recorded real time. Data collection of 200 samples per second recording of speed, current, voltage, and torque creates high resolution speed versus current and torque curves. Contact Bradleys to discuss the motor’s size.
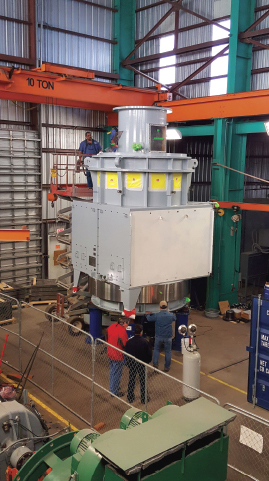
THRUST STANDARDS AND FLEXIBILITY
The required minimum thrust bearing load poses challenges for vertical motors for only a few hours of the load testing process. Many times the internal clearance of a motor can be adjusted to solve the problem. In other cases, the preload load springs are removed; and the internal motor end float is reduced to zero or a light preload is created to facilitate the four-hour load test.
Engineered external thrust load can also be added to the system during the load test. Opposing thrust bearings are loaded hydraulically to simulate the external thrust loads. In-house engineering, fabrication, SolidWorks software draftsmen, and CNC machine shop capabilities enhance Bradleys’ ability to design and manufacture a myriad of special features for load testing.
The flexibility of our Hi-Power Load Testing System enables Bradleys’ to meet its customers unique motor and system testing requirements. Variable voltage supplies of 480V@2,500 amps up to 13.2KV@250 amps are available for a variety of test setups. Water cooled motors are supported with a 150 gallons per minute supply providing up to 200 KW of heat dissipation. Additionally, Bradleys can provide full voltage locked rotor testing up to 1500 horsepower. IEEE 112 Specification is followed. Synchronous motor testing is performed using the IEEE 115 Specification.
KEEPING CUSTOMERS IN MIND
Bradleys encourages all customers to be present and witness their load test. The company’s state of the art customer observation room comfortably accommodates eight people. Perched 10 feet above the load testing stand, a customer can witness the load test from a safe and quiet distance. For long days of testing, high speed internet is available for our guests to stay connected to their offices, if they wish. All real time data is displayed live on dedicated monitors within the customer observation room. A web address can be provided for live data and video camera feeds over the internet if your schedule does not allow you to witness the load test on-site.
Bradleys’ customer observation room is soundproof to provide comfort. The walls are 8-inch thick and reduce 100 decibels test floor noise down to 68 decibels. Comfortable conference room chairs try to make what Bradleys’ hopes to be an uneventful day of load testing more accommodating.
If your application requires testing with a VFD, this service is also available. Bradleys can power up your drive to run the motor under test. The customer is required to provide a drive technician for setup supervision and operation of the drive. Bradleys can provide manpower for handling and wiring of the drive at the direction of the drive technician. Cat 5 or Cat 6 cabling is available so technicians can join the Bradleys staff in the “Mission Control Room” and operate the VFD from the soundproof enclosure. Additional services are also available such as ANSI sound testing can be performed.
LOAD TESTING FOR THE FUTURE
Bradleys’ Hi-Power Load Testing is utilized by most of the OEM and motor manufacturers for design verification. We are dedicated to ensuring our customers have the services available to increase their motors’ reliability. We recognize lost productivity in operations is lost revenue. The Bradleys team is dedicated to adding new capabilities such as vertical motor load testing, to prevent and minimize downtime for our customers.
FOR MORE INFORMATION
Siemens Digital Industries Software, a business unit of Siemens Digital Industries, is a leading global provider of software solutions to drive the digital transformation of industry, creating new opportunities for manufacturers to realize innovation. With headquarters in Plano, Texas, and over 140,000 customers worldwide, we work with companies of all sizes to transform the way ideas come to life, the way products are realized, and the way products and assets in operation are used and understood. For more information, visit www.sw.siemens.com.
Jim Williams is president of Bradleys, Inc. With ninety years of small to 50,000 horsepower motor repair and rewinding experience, 7,000 horsepower full load testing, no load testing, and small and large vertical motor load testing, Bradleys is leading the industry in innovation and experience. Bradleys quality procedures and processes have earned the company ISO 9001: 2015 certification, EASA Accreditation, and Green Motor Rewinds Certification. For more information, visit www.bradleysmotors.com.
MODERN PUMPING TODAY, May 2019
Did you enjoy this article?
Subscribe to the FREE Digital Edition of Modern Pumping Today Magazine!
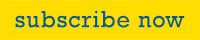