Extreme volatility in the global oil prices is leading a tight price war among larger players. The decline in oil prices is resulting in the consolidation of various activities. The industry is also experiencing a shift from conventional operational procedures to innovative operational procedures. Pump manufacturers are tapping this potential with a focus on innovation, remote monitoring and maintenance. Technologies including Industrial Internet of Things (IIoT), Artificial Intelligence (AI), and Big Data are significantly growing with industrial automation.
Reciprocating pump manufacturers are witnessing a digital transformation by integrating AI, IIoT, and Big Data. Usually, the fault in the reciprocating pump is judged by the flow meter and pressure gauge. Identifying the valve in which the problem has occurred is extremely difficult with flow meter and pressure gauge, and this is increasing the maintenance time and workload. This is resulting in the development of connected machines with real-time monitoring in the production line.
Industrial equipment manufacturers are focusing on the integration of low-cost sensors. In-built diagnostic sensing technology is transforming the way of maintaining and managing the reciprocating pumps. These sensors monitor the condition of the pumps and provide massive amount of data in real-time.
Energy companies and oil and gas plants are actively seeking cost-effective alternatives for recurring leakage failure in reciprocating pumps. Connected technologies also alerts managers about the adverse condition providing time to take crucial decisions.
Power generation is expected to increase in the near future. With this, the process of equipment monitoring is also advancing including capturing data, performance testing, maintenance for better flow, and higher efficiencies.
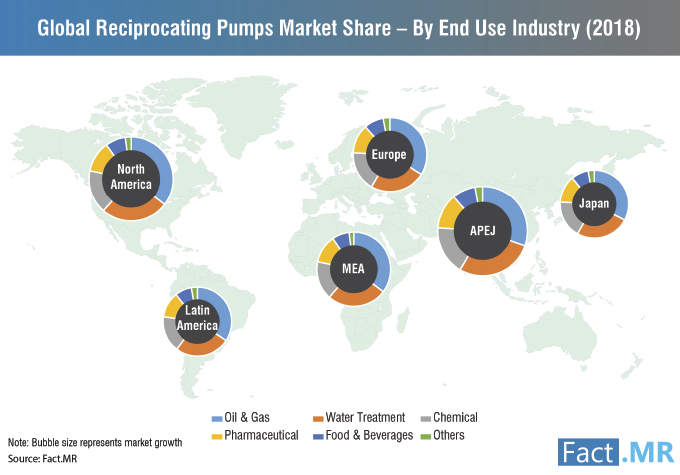
IMPROVING MAINTENANCE WITH SYSTEM MODIFICATION
The pulsating nature of the flow in reciprocating pumps frequently requires pulsation dampeners. Reciprocating pumps consists large number of moving parts, which increases the chances of problems in any part of the pump. Hence, these pumps require regular maintenance, thus, leading to higher maintenance cost.
System modification is an economically viable option, reducing maintenance cost, restore mechanical integrity, and ensure optimum operation. Sensor systems are being integrated into the reciprocating pumps to detect vital pump condition parameters. These sensors are self-powered using pump vibration, pump motion, or another energy source from the pump as a power source.
These sensor systems provide data on the pump condition, indicating abnormal events during pumping. Limited capability to diagnose the scope of failure in the reciprocating pump is one of the common challenges faced by the manufacturers. Pump manufacturers are introducing IIoT monitoring solutions as a part of system modification with critical features such as a monitor and notify pump cavitation, predict pump wear, motor failure, notify excessive vibration, predict seal failure, monitor oil level, and voltage usage.
Oil and gas, water treatment, and chemical companies are investing in the plant modernization activities with an increased focus on IoT monitoring solution. With the growing demand for smart pumps in the oil and gas industry, pump manufacturers are collaborating with software companies to design and develop smart reciprocating pumps for remote monitoring.
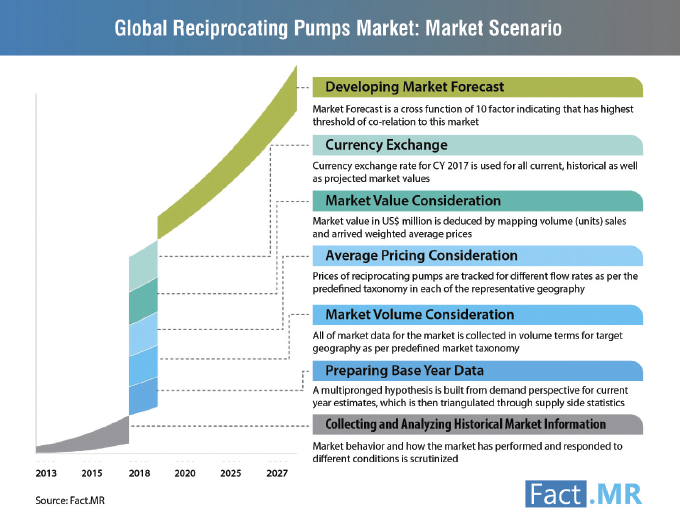
SMART PUMPING SYSTEM INFLUENCING SALES OF RECIPROCATING PUMPS
Rise in oil and gas demand globally is likely to result in significant growth in the reciprocating pumps. The oil demand is likely to reach 104 mb/d by 2023 as per the International Energy Agency (IEA). This rise in demand is expected to accelerate the extracting process of oil and gas resources using reciprocating pumps.
Failure of pumps in oil and gas application is leading to huge financial cost. It also poses environmental and safety hazards. This has made the safety of pumps extremely important. To meet the rising demand and ensuring smooth working of operations. Manufacturers are integrating sensors in reciprocating pumps to predict any failure in the pumps and save time and minimize high maintenance cost.
Minimizing the noise emission from pumps while maintaining the same level of performance is also gaining traction as countries are trying to lower dependence on foreign oil sources. This has forced the companies to produce oil and gas in locations that are considered too close to residential areas. In order to carry-out the process and comply with regulations for operating in such areas, companies are integrating low-noise equipment in their pumping system.
Increasing investment in energy generation is increasing the sales of reciprocating pumps, especially in the Asia Pacific region. With the growing demand for reciprocating pumps in the region, manufacturers are focusing on integrating smart solutions to simplify management and maintenance, enable pump failure prediction, and save cost.
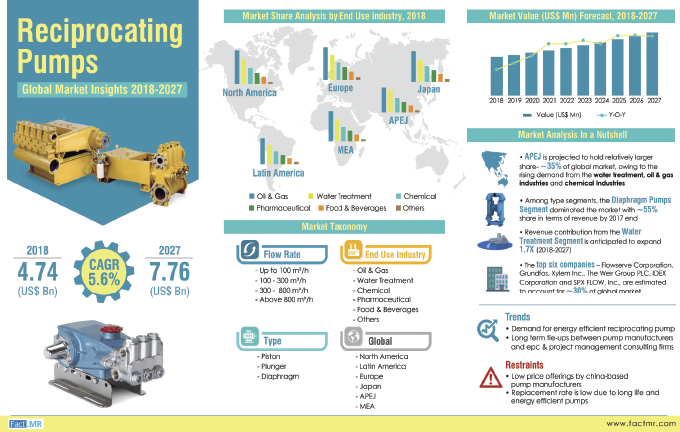
A HOST OF PUMPING CHALLENGES WITH RISE IN OFFSHORE PRODUCTION
According to the International Energy Agency (IEA), by 2040, the energy-related offshore activity is likely to increase. The cost of many offshore oil and gas projects have come down in the recent years. Designs are being simplified and standardized, and the market for offshore equipment and services is also exerting downward pressure on the cost. Digitalization in offshore operations is expected to be the next frontier leading to efficiency and cost-reduction.
Offshore oil producers are depending heavily on the water injection in order to maintain production levels. This is also driving the flow rate and injection pressure, resulting in increased erosion and corrosion challenges. Pumps for offshore oil and gas services are being integrated with sensors to avoid any damage or failure during oil extraction and transportation. Often, diaphragm pumps are installed at offshore oil and gas platforms as extraction requires the application of special chemicals.
With the rise in offshore oil and gas activities, water management has become a key component, emerging as a complex and challenging issue for operators. Smart technologies supporting water management are gaining popularity. Pump data is usually collected with remote monitoring technology, which warns the operators of the fault in a pump and problems such as blocked filters. With advanced technologies and control systems, some of the smart monitoring systems also allows operators to remotely lock or turn-off the pump.
Oil exploration and development companies are also entering into a contract with software companies to install a smart monitoring system for equipment to avoid unnecessary maintenance services and cost apart from altering the traditional maintenance approach. For instance, Aker BP signed a smart service contract with Cognite and Framo Services, providing a real-time access to data on pumps, this helps to predict how pumps will perform in the future.
The trend of rising in sanctioning activity is growing stronger with new offshore projects. Several projects are likely to get an approval in the coming years. Largest projects in key offshore areas including Gulf of Mexico, Brazil, and the North Sea are expected to receive development approval by 2025. To keep these offshore projects competitive, companies and operators are focusing on maintaining the cost saving and avoiding unnecessary faults in equipment by using smart technologies.
Wireless monitoring technologies are gaining increasing demand for pump monitoring owing to the cost-effectiveness and combined predictive analytics offered to identify any faults in the pump in real-time and significantly streamlining maintenance. Wireless solutions are providing diagnostic data at a rapid speed in real-time, this simplifies the maintenance process making it quick and effective.
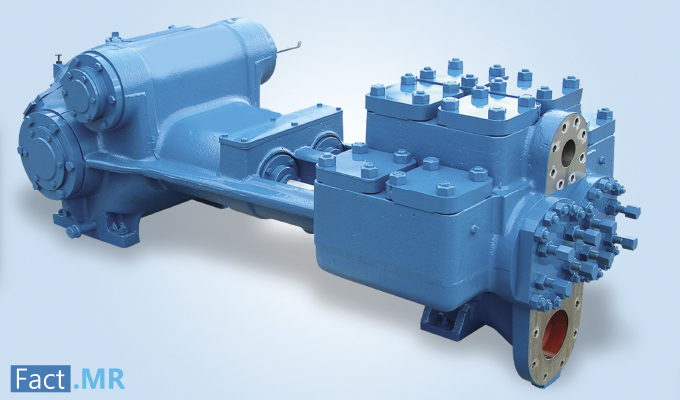
POSITIVE START TOWARDS ADVANCED PUMP MONITORING TECHNOLOGIES
Upstream oil and gas companies are also facing pressure from regulatory to minimize the impact on the environment. This is resulting in a drastic shift towards the deployment of sensors and IoT to minimize the impact of operations and reduce the leakage. With advancement in technologies, autonomous robots are likely to be used in near future to monitor equipment, pumps, and inspect leakages, especially in high risk areas in oil and gas plants for humans.
Non-productive time in oil and gas sector is resulting in loses of billions of dollars every year. Thus, companies are taking a positive step towards connected technologies in pumps and other equipment with access to real-time data and predictive analysis to optimize operations and save on maintenance.
FOR MORE INFORMATION
The insights presented here are from a research study on the reciprocating pumps market by Fact.MR, an independent, pure play market intelligence firm incorporated with an objective to deliver high quality, customized market research solutions that help clients successfully go to the market equipped with actionable insights capable of impacting crucial business decisions. For more information, visit www.factmr.com.
MODERN PUMPING TODAY, May 2019
Did you enjoy this article?
Subscribe to the FREE Digital Edition of Modern Pumping Today Magazine!
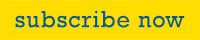