Let’s face it: the average engineer is more willing to embrace the innovations in the new iPhone model than the latest features in a low-flow/low-pressure metering pump.
Why is that? The practical, day-to-day improvements of pump innovation may seem minuscule. The perceived risk of trying new technology also may feel too high, especially when change is slow in the low-flow/low-pressure applications that diaphragm metering pumps are used for.
In fact, the status quo for a pump at this end of the market tends to be to use it until it breaks down or maintenance is required – typically within a year – then simply dispose of the pump and buy a new one.
New standards for low-flow/low-pressure metering pumps
If all this seems a bit shortsighted to you, read on. What companies don’t need, especially today, is boneyards filled with more failed pumps based on flawed, outdated designs. Reliability engineers, plant managers, engineering consultants, and other pump buyers deserve a better set of choices. For some, this may require a shift in expectations, but the total cost of ownership and efficiency benefits can be substantial and hard to argue.
Here’s what we see as five modern technology requirements that buyers should seek out in the often underserved low-flow/low-pressure metering pump market.
Immediate rupture awareness. Sandwich diaphragm technology should ensure immediate detection of a diaphragm rupture while maintaining pump operation. Look for diaphragm monitoring that detects fluid ingress between diaphragm layers. This allows operators to plan a controlled shutdown, ensuring system integrity, safety, and minimal process disruption.
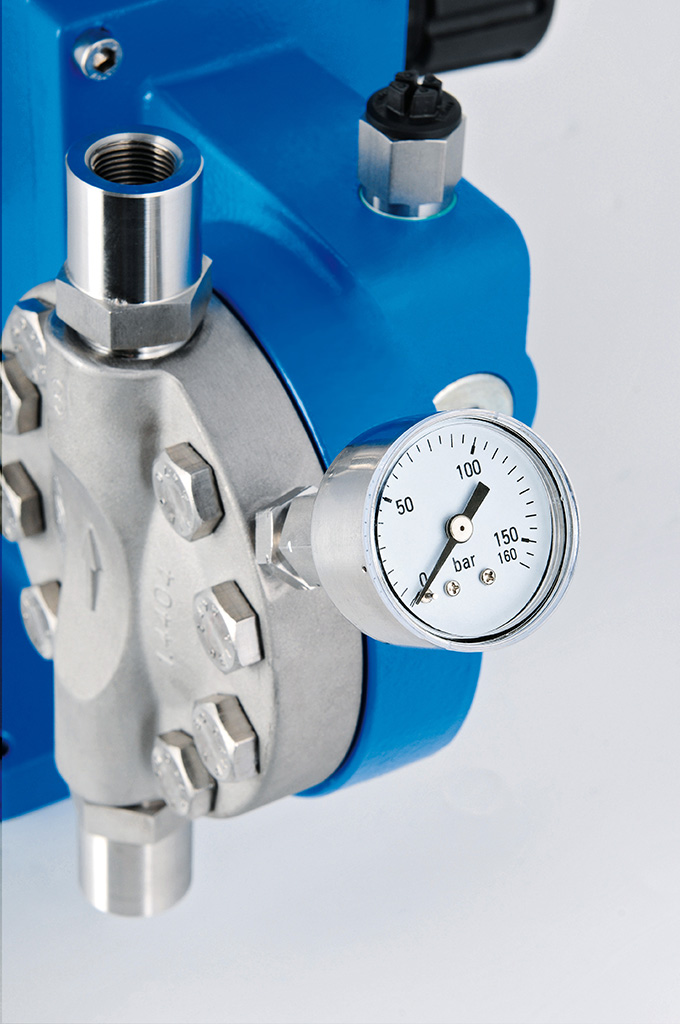
High performance under more conditions. Having a spring assist inside the pump chamber that pulls the diaphragm back means you don’t need as much suction pressure. And because you don’t have to worry about process conditions being perfect, your pump can perform independently while helping you meter more precisely.
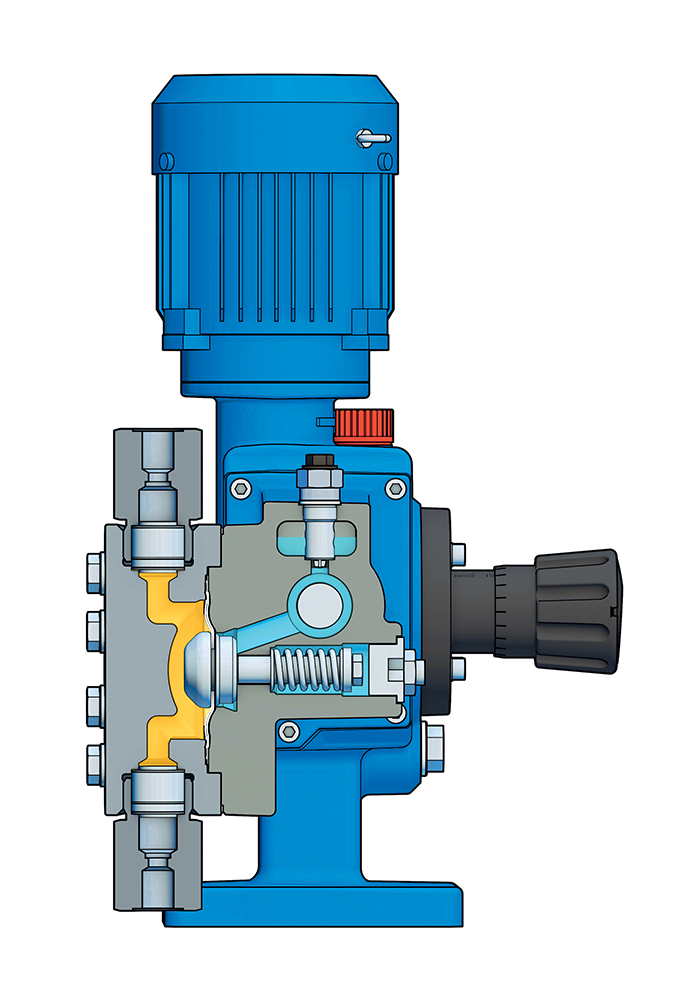
Easy maintenance. Servicing a pump should be fast and easy and not require a major slowdown in production. If the diaphragm comes pre-built with easy bolt removal and is ready to be threaded back on after service, maintenance can take minutes and the pump is much less likely to be tossed after a diaphragm rupture. This is a much simpler operation than having to align different parts of the diaphragm or having to completely drain the pump’s oil before servicing, which can turn into a half-day operation.

Uncompromising accuracy. Accurate chemical dosing is essential to ensure efficiency and cost savings. The check valves, one on the suction side and one on the discharge side, play a critical role in maintaining precision. These valves prevent backflow and ensure that each stroke of the pump delivers a consistent, metered volume of fluid. Without properly functioning check valves, issues like inaccurate dosing, pulsation, and flow irregularities can arise, leading to inefficiencies and potential equipment damage.
Quantifiable repeatability. You should always know exactly how much fluid is being displaced in your pump. Controlling stroke length precisely yields absolute (versus relative) measurement of how much the diaphragm is moving and the pump is displacing. Another way to increase that confidence? Haptic feedback on the pump’s flow knob that clicks to indicate you’re at exactly the flow you want.
An investment, not a cost
In 2025, we believe that there should be better options out there for operational leads and engineers to get the critical precision dosing they need from a pump without having to sacrifice affordability, ease of maintenance, or performance.
Also, it should go without saying that if a pump is designed around the modern user’s needs and built with uncompromising quality, it should come with a lengthy warranty – one that communicates that you are unlikely to be tossing out a pump every year or so. Shouldn’t we be moving beyond such short useful life?
Jorge Guevara is an Aftersales & Technical Services Manager at LEWA America. Brad Schard is a Sales Manager, Texas and GOM Offshore, at LEWA America. LEWA’s trendsetting products and innovative technologies have set benchmarks for diaphragm pumps and metering systems for over 70 years.
For more information about LEWA’s innovative and surprisingly affordable ecosmart® diaphragm metering pump, which comes with the industry’s only 10-year warranty, visit https://shop.lewa.com/us/configurator.